To avoid common tuckpointing mistakes in commercial projects, you'll need to master five critical aspects. Start by guaranteeing precise mortar color matching through multiple test panels and documented mixing ratios. You must prepare joints to proper depth (at least twice the width or 3/4 inch minimum) and clean them thoroughly. Schedule work in temperatures between 40°F and 90°F, avoiding rain exposure. Use appropriate, well-maintained tools that match joint widths, and thoroughly clean surfaces before beginning work. Mastering these fundamentals will help prevent costly repairs and guarantee your project's long-term success. These key principles form just the foundation of expert tuckpointing technique.
Poor Mortar Color Matching
The improper matching of mortar colors ranks among the most visible and problematic mistakes in commercial tuckpointing projects. When you're working on historic or existing buildings, achieving the right color match isn't just about aesthetics—it's vital for maintaining architectural integrity and client satisfaction.
To avoid color matching failures, you'll need to implement proven mortar selection strategies. Start by collecting samples of the existing mortar and analyzing them under different lighting conditions. You'll find that natural sunlight reveals subtle color variations that artificial lighting might mask. Consider creating multiple test panels with different pigment ratios before committing to a final mix.
Your color blending techniques should account for aging factors and environmental conditions. You'll want to remember that new mortar typically appears lighter when cured and will darken over time. It's important to mix larger batches of mortar at once to maintain consistency throughout the project. When you're working with multiple walls or elevations, you should document your mixing ratios meticulously—this guarantees uniformity across the entire project and helps your team maintain professional standards that your peers in the industry respect. Additionally, proper mortar joint repair is crucial to ensure that your tuckpointing efforts last and remain visually appealing over time.
Incorrect Joint Preparation
While matching mortar colors sets the foundation for quality tuckpointing, proper joint preparation determines the long-term success of your commercial restoration work. You'll need to guarantee that all deteriorated mortar is completely removed to achieve the correct joint depth, which should typically be twice the joint's width or a minimum of 3/4 inch.
When you're preparing joints, you must remove all loose debris and dust before applying new mortar. Using the wrong tools or improper techniques can damage the surrounding masonry and compromise material compatibility. Don't rely on power tools exclusively – while they're efficient, they can create micro-cracks in the brick faces and cause uneven joint depths.
You'll want to test the hardness of existing mortar to determine the appropriate removal method. After grinding out the old mortar, thoroughly clean the cavity with compressed air or water. Remember that proper joint preparation isn't just about depth – it's about creating a clean, sound surface that will bond effectively with your new mortar. If you rush this critical step, you're likely to face premature joint failure and costly repairs down the line. Additionally, understanding the importance of masonry restoration services can help ensure the longevity of your tuckpointing project.
Weather Timing Mistakes
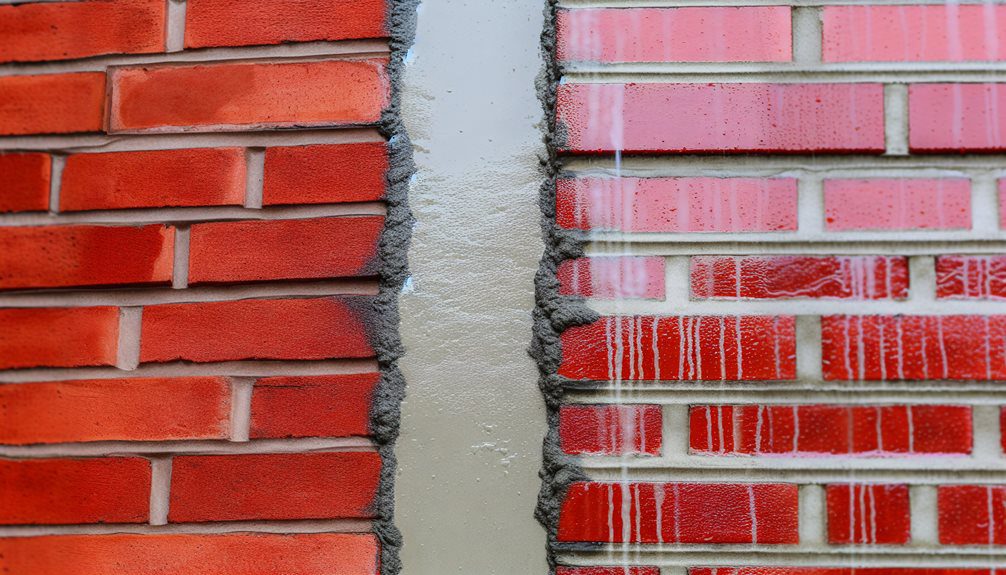
Scheduling tuckpointing work around adverse weather conditions stands out as one of the most critical factors in commercial masonry restoration. You'll find that failing to account for weather patterns can lead to compromised mortar curing, adhesion issues, and costly rework.
When you're planning your tuckpointing project, don't make the mistake of ignoring seasonal planning considerations. You'll want to avoid working in temperatures below 40°F (4°C) or above 90°F (32°C), as these extremes can affect mortar hydration and strength development. Rain exposure within 24 hours of application can wash out fresh mortar joints, while strong winds can cause rapid moisture loss and improper curing.
You should schedule your work during moderate temperature periods, typically spring or fall, and always check extended weather forecasts before beginning. It's crucial to protect fresh tuckpointing work using appropriate covers or shields when unexpected weather threatens. Remember that proper timing isn't just about avoiding rain – you'll need to take into account humidity levels, daily temperature fluctuations, and the building's exposure to direct sunlight. These factors directly impact your mortar's curing process and the project's long-term success. Additionally, consider applying waterproofing techniques to enhance the durability of your tuckpointing work against future weather challenges.
Wrong Tools and Techniques
Selecting proper tools and techniques represents a cornerstone of successful tuckpointing in commercial masonry restoration. When you're working on large-scale projects, you can't afford to use improper joint raking tools or rely on outdated mortar application methods. You'll find that inexperienced contractors often make the mistake of using angle grinders without proper dust control or choosing the wrong sized joint tools for the mortar joints they're repairing.
You'll need to guarantee your team uses appropriate pointing irons that match the joint width precisely. Don't fall into the trap of using damaged or worn tools that can create inconsistent joint profiles. If you're seeing irregular mortar depths or uneven finishing, it's likely due to inadequate training in proper tool handling techniques. Your tuckpointing professionals should understand the distinct differences between various joint styles and the specific tools required for each.
Remember that power tools, while efficient, aren't always the best choice for historic masonry work. You'll want to maintain a balance between mechanical efficiency and preservation requirements. When you're investing in tools, focus on quality pointing irons, joint rakers, and proper mixing equipment to guarantee consistent results across your commercial projects. Additionally, using certified and insured contractors can help ensure that the tools and techniques employed meet industry standards and project expectations.
Inadequate Surface Cleaning
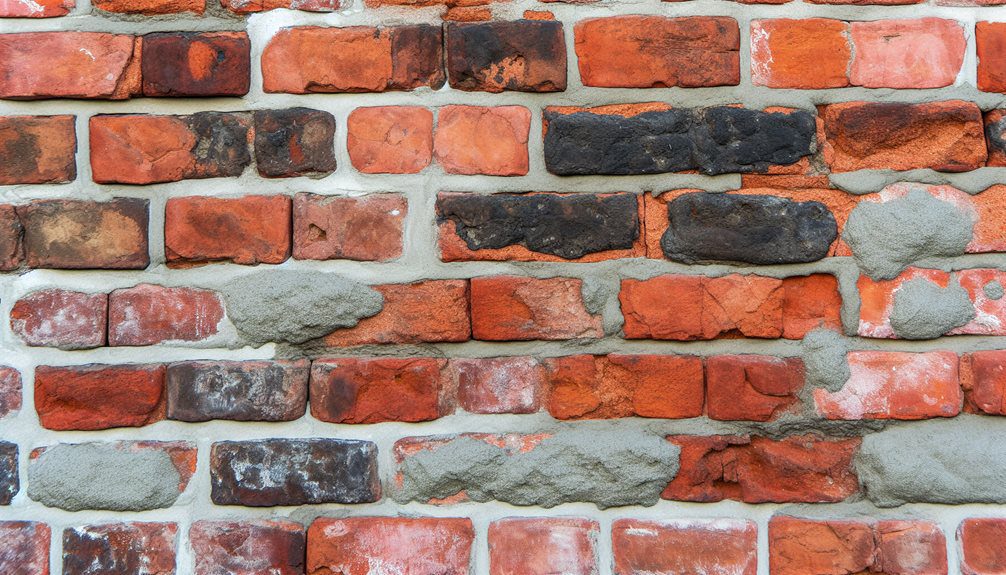
Even the best tools and techniques can't compensate for poorly prepared surfaces in tuckpointing projects. When you skip proper surface preparation, you're setting yourself up for adhesion failures, moisture infiltration, and premature deterioration of your repairs. You'll need to remove all loose mortar, dirt, debris, and biological growth before beginning any tuckpointing work.
Your surface cleaning methods should align with industry standards and the specific conditions of your commercial project. You'll want to start with dry cleaning techniques like wire brushing and compressed air to remove loose material. For stubborn deposits, you'll need to progress to appropriate wet cleaning methods, making sure you don't oversaturate the masonry. Don't make the common mistake of rushing through this critical step.
Remember that inadequate cleaning compromises not just the immediate repair but the entire building envelope's integrity. You must achieve a clean, sound substrate that's free from contaminants and ready to bond with new mortar. When in doubt, test your cleaning methods on a small, inconspicuous area first to verify they won't damage the existing masonry or surrounding materials. Additionally, proper surface cleaning is essential for ensuring the longevity of your repairs and maintaining the structural integrity of the building.
Frequently Asked Questions
How Long Should Tuckpointing Last Before Needing Maintenance?
You can expect your tuckpointing to last between 20-30 years when properly installed. However, the tuckpointing lifespan varies based on your climate conditions, weather exposure, and initial workmanship quality. It's best to establish a maintenance schedule that includes annual inspections to catch early signs of deterioration. You'll want to look for cracking, crumbling, or missing mortar joints. Regular checks help you address issues before they become major problems.
What Is the Average Cost per Square Foot for Commercial Tuckpointing?
When you're planning your commercial tuckpointing project, you'll find that pricing typically ranges from $7 to $15 per square foot. However, your actual costs can fluctuate based on several factors. Building height, accessibility, and mortar deterioration levels will impact your final estimate. For commercial contracts, you're often looking at volume pricing, which might reduce your per-square-foot costs. You'll also need to factor in regional labor rates and material costs.
Can Tuckpointing Be Done During Winter Months With Proper Precautions?
While you can perform tuckpointing in winter, you'll need to implement specific winter preparations to guarantee success. The mortar must maintain a minimum temperature of 40°F (4°C) for at least 48 hours after application. You'll want to use heated enclosures, thermal blankets, and appropriate admixtures for cold weather masonry work. Temperature considerations are essential – monitor both ambient and surface temperatures throughout the process to prevent freeze-thaw damage to fresh mortar.
Are There Building Codes Specific to Tuckpointing in Commercial Structures?
Yes, you'll find specific tuckpointing regulations for commercial buildings in most jurisdictions. These standards typically fall under masonry codes in the International Building Code (IBC) and local building ordinances. You'll need to comply with commercial standards regarding mortar composition, joint depth, and structural integrity. It's crucial to check with your local building department, as requirements can vary by region and building type. Many municipalities also require licensed contractors for commercial tuckpointing work.
Should Buildings Remain Operational During Large-Scale Tuckpointing Projects?
You'll need to carefully evaluate whether to keep your building operational during tuckpointing work. While it's possible to maintain operations, you'll face operational challenges like noise, dust, and restricted access. You should create a detailed phasing plan that minimizes building disruptions and guarantees occupant safety. It's best to coordinate work during off-peak hours and communicate extensively with tenants about temporary inconveniences. Consider sectioning off work areas to maintain business continuity.