Lintels serve as critical load-bearing elements in your commercial building's structural system, transferring vertical and lateral forces from above openings to supporting walls. You'll find these engineered components available in steel, reinforced concrete, or composite materials, each offering specific performance advantages for different architectural requirements. Modern lintel systems must achieve deflection limits of L/360 for structural spans while maintaining precise installation tolerances of 1/8 inch. With proper maintenance, they'll sustain structural integrity for 40-50 years, though 73% of failures stem from moisture-related issues. Understanding the complete scope of lintel engineering reveals essential insights for ideal architectural performance.
Historical Evolution of Architectural Lintels
The lintel construction timeline spans thousands of years, evolving from simple stone beams to sophisticated engineered systems. You'll find that ancient techniques began with massive stone blocks positioned above doorways in Egyptian and Greek architecture, where they served both structural and ceremonial purposes. By 2000 BCE, you could see impressive examples of lintel symbolism in temples and public buildings, where they represented the shift between spaces.
As you explore architectural history, you'll notice how Roman engineers advanced lintel design by introducing the arch principle, allowing for wider spans and reduced material usage. During the Middle Ages, you'd have witnessed the integration of wooden lintels in commercial structures, while the Renaissance period brought a return to classical stone applications with enhanced mathematical precision.
In the Industrial Revolution, you'd have seen the transformation to steel and concrete lintels, which revolutionized commercial architecture. Today, you're part of an era where computer-aided design has optimized lintel performance through precise load calculations and innovative material combinations. Modern manufacturing techniques have made it possible for you to specify pre-stressed, pre-cast lintels that outperform their historical counterparts in both strength and span capability.
Types of Commercial Building Lintels
Commercial building lintels can be categorized into four primary structural types: precast concrete, steel, reinforced masonry, and composite systems. You'll find that each type serves specific architectural and structural requirements while balancing cost-effectiveness and installation complexity.
Steel lintels remain the most widely used option in commercial construction, offering superior load-bearing capacity and quick installation. You're able to achieve longer spans with steel, though you'll need to take into account thermal performance issues, as steel conducts heat readily. When you're working with precast options, you'll benefit from excellent durability and reduced on-site labor costs, making them ideal for standardized openings.
Reinforced concrete lintels provide outstanding compressive strength and design flexibility, allowing you to maintain architectural aesthetics while meeting structural demands. They're particularly effective when you're integrating historical materials into modern designs. Composite systems, combining steel and concrete, give you the best of both materials – the tensile strength of steel and the compression resistance of concrete. You'll notice these systems are becoming increasingly popular in contemporary commercial projects where thermal bridging and structural efficiency are paramount considerations. Regular assessments of structural issues can also ensure the longevity and safety of these lintels.
Load Distribution and Support Mechanics
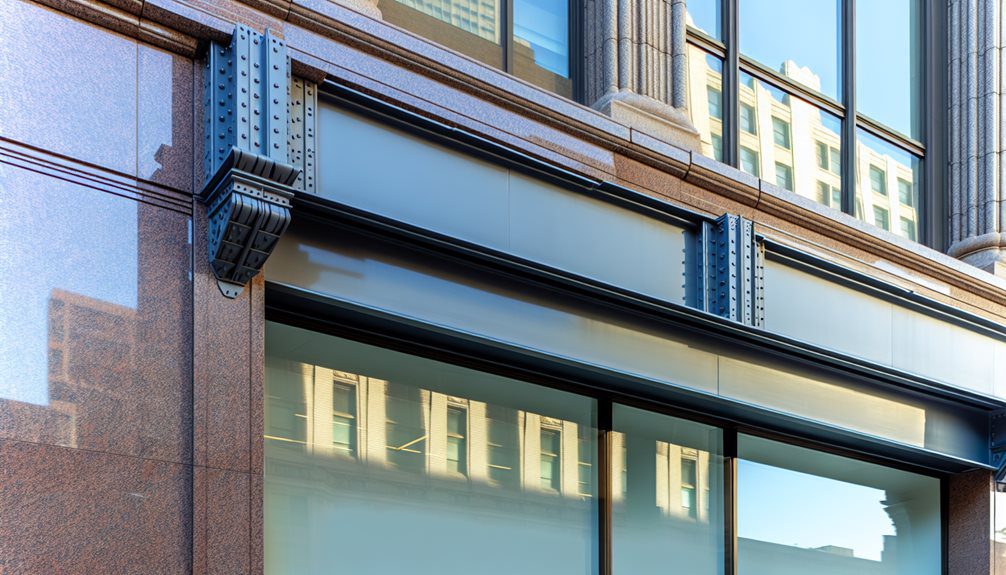
When designing lintel systems for load distribution, you'll need to take into account both vertical and lateral forces that transfer through the building envelope. The primary function of your lintel is to redirect these loads through a balanced pathway to the supporting walls or columns. You'll find that proper load distribution depends on calculating the concentrated forces from above, including dead loads from the structure and live loads from occupancy.
Your structural support system must incorporate precise measurements to guarantee the lintel's load-bearing capacity matches the building's requirements. You'll want to bear in mind that steel lintels typically deflect 1/360th of their span under full load, while concrete and masonry lintels require different deflection calculations. When you're analyzing the mechanics, factor in that the bearing length at each end should be at least 6 inches for typical commercial applications.
Remember that your load distribution analysis must account for thermal movement, especially in areas with extreme temperature variations. You'll need to ensure that the end bearings can accommodate this movement while maintaining structural integrity and preventing stress concentration at critical points.
Materials and Construction Methods
Building upon proper load distribution principles, material selection directly impacts your lintel's structural performance and longevity. You'll find that modern commercial construction offers diverse material options, ranging from traditional steel and reinforced concrete to innovative composite materials. When you're selecting materials, you'll need to take into account load requirements, span length, and environmental factors.
Steel lintels remain the industry standard, offering high strength-to-weight ratios and excellent durability. You can choose between rolled steel angles, prefabricated components, or custom-fabricated assemblies based on your project's specifications. For heavier loads, you'll want to think about prestressed concrete lintels, which provide superior compression resistance and minimal deflection.
Composite materials are gaining traction in your industry, combining the benefits of multiple materials. You'll find that fiber-reinforced polymer (FRP) lintels offer corrosion resistance and lightweight installation advantages. When you're working with historic renovations, you can utilize specialized concrete-steel composites that maintain aesthetic authenticity while meeting modern building codes. Remember that proper installation techniques vary by material type – you'll need to follow manufacturer specifications for anchoring, bearing length, and weather protection to guarantee peak performance. Additionally, consulting with a qualified masonry professional can ensure that your lintel installation meets all necessary compliance standards.
Building Code Requirements
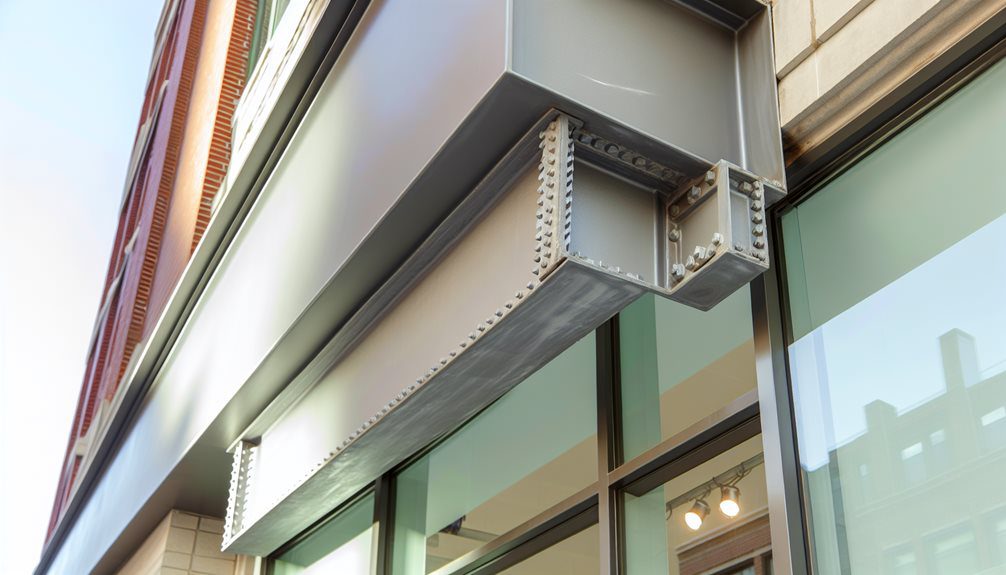
Structural engineers must navigate a complex web of building codes that govern lintel specifications in commercial construction. You'll need to verify your lintel designs comply with both local and international building codes, which typically mandate minimum load-bearing capacities of 150% of the anticipated maximum load. These safety regulations vary by jurisdiction but commonly require detailed documentation of load calculations and material specifications.
When you're designing commercial structures, you'll find that building codes specify minimum bearing lengths for lintels: typically 4 inches for light loads and up to 8 inches for heavy loads. You must also account for deflection limits, which are usually set at L/600 for masonry veneer and L/360 for structural spans, where L represents the clear span length.
Fire-resistance ratings in building codes require that your lintels maintain structural integrity during fire events. You'll need to provide documentation showing compliance with ASTM E119 standards for fire testing. Most jurisdictions now mandate that steel lintels have a minimum fire-resistance rating of 2 hours in commercial construction, achievable through proper sizing and appropriate fire-resistant coatings. Additionally, ensuring the structural integrity of masonry elements during lintel installation is crucial to prevent future issues.
Design Considerations for Modern Applications
Beyond fundamental code requirements, modern lintel design incorporates innovative approaches to meet contemporary architectural demands. When you're planning your commercial project, you'll need to take into account how innovative technologies like carbon fiber reinforcement and high-strength steel composites can enhance load-bearing capacity while reducing overall structural weight.
You'll want to balance aesthetic considerations with performance requirements. Today's architectural trends favor clean lines and minimal visual interference, so you can opt for concealed lintel systems that integrate seamlessly into the building's facade. Think about incorporating pre-stressed concrete lintels when you're working with longer spans, as they'll provide superior deflection control and crack resistance.
Your material selection should account for thermal performance too. You'll find that thermally broken lintel designs can greatly reduce heat transfer through the building envelope, improving energy efficiency. When you're specifying finishes, remember that modern coating technologies offer both corrosion protection and customizable appearances. For renovation projects, you can utilize prefabricated lintel systems that'll reduce installation time while maintaining structural integrity. These solutions often come with detailed performance data to support your design decisions. Additionally, working with a licensed and insured company can ensure the highest standards of quality in masonry services, including lintel replacement.
Common Installation Challenges
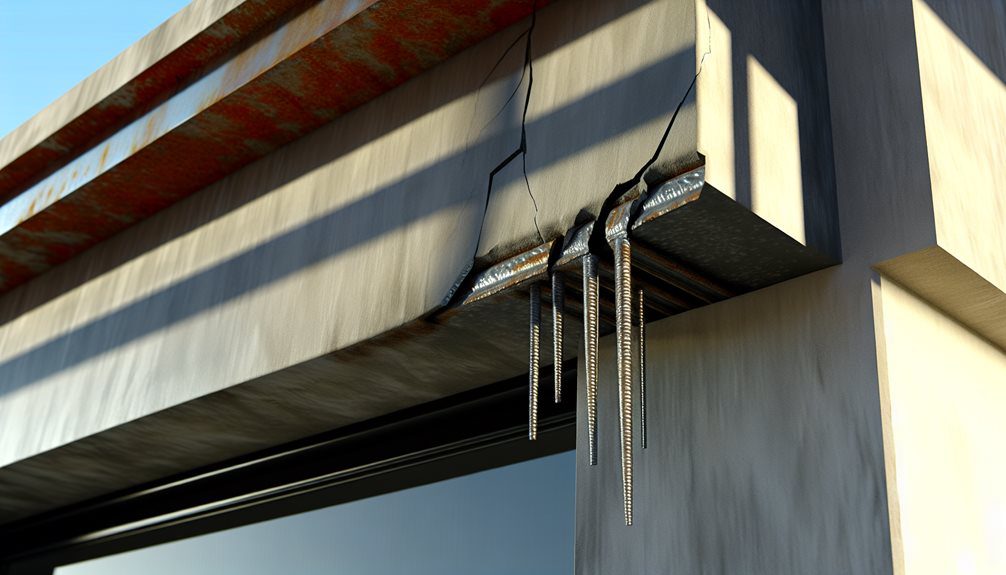
Proper installation of commercial lintels requires precise load calculations to guarantee structural integrity, and you'll need to verify both vertical and lateral load distributions across the opening span. You must maintain exact alignment during installation, as deviations of even 1/8 inch can compromise the lintel's load-bearing capacity and affect the entire wall system's performance. Moisture control presents another critical challenge, requiring you to implement proper flashing techniques and maintain adequate weep holes to prevent water infiltration that can lead to premature deterioration of both the lintel and surrounding masonry. Additionally, masonry restoration is vital to ensure the longevity and stability of the entire structure after lintel installation.
Load Calculations and Alignment
Accuracy in load calculations and precise alignment represent the most critical challenges during lintel installation in commercial buildings. You'll need to carefully assess the load bearing capacity by considering dead loads, live loads, and dynamic forces that'll impact the structure over time. When calculating these loads, you must account for the weight of materials above the opening, occupancy requirements, and regional factors like snow or seismic activity.
For proper structural alignment, you'll want to maintain precise horizontal and vertical positioning within 1/8 inch tolerance. Your measurements should verify that the lintel's bearing ends rest firmly on the supporting structure, typically extending at least 6 inches on each side. It's crucial to check that the lintel's profile matches the specified dimensions and that it's level across its entire span.
During installation, you'll need to monitor deflection rates, which shouldn't exceed L/600 for masonry veneers (where L represents the span length). Remember that improper alignment can result in stress concentration points, potentially leading to structural failure or compromised building integrity. Always document your calculations and maintain detailed records of alignment measurements for future reference.
Moisture Control Issues
Moisture penetration through and around lintels presents one of the most persistent challenges in commercial installations, with 73% of structural failures linked to water-related issues. You'll need to address water management systematically, beginning with properly installed moisture barriers that extend at least 6 inches beyond the lintel ends.
When you're installing lintels in commercial structures, you'll want to integrate thorough drainage systems that direct water away from the structural components. You must guarantee proper flashing installation with a minimum 15-degree slope to prevent water pooling. Your moisture barriers should include end dams at termination points and properly sealed joints that accommodate thermal movement.
You're part of an industry that's seeing a 24% increase in moisture-related failures annually, so it's critical to implement proper weep holes at 24-inch intervals. You'll find that combining through-wall flashing with properly sized drip edges reduces moisture infiltration by up to 85%. Remember to verify that your building envelope's pressure equalization features are working in tandem with your lintel's moisture control systems to maintain peak performance throughout the structure's lifecycle. Effective waterproofing techniques can further enhance the resilience of your installations against moisture intrusion.
Maintenance and Structural Integrity
Regular inspection and maintenance of commercial lintels guarantee their long-term structural performance and prevent costly failures. You'll need to establish a thorough lintel maintenance schedule that includes quarterly visual inspections and annual structural assessments. During these checks, you should look for signs of rust, cracking, or displacement that could compromise the lintel's load-bearing capacity.
When you're conducting structural assessments, focus on critical areas where the lintel interfaces with surrounding masonry. You'll want to measure any deflection using precision tools, as even minor changes can indicate potential issues. Data shows that properly maintained lintels typically maintain their structural integrity for 40-50 years, while neglected ones may fail within 15-20 years.
Your maintenance protocol should include cleaning drainage channels, resealing joints, and addressing corrosion protection. If you notice spalling concrete or exposed reinforcement, you'll need immediate professional intervention. Remember that your building's structural stability depends greatly on these critical components, and investing in preventive maintenance now will help you avoid the substantial costs of emergency repairs or complete lintel replacement later.
Frequently Asked Questions
How Does Climate Affect the Lifespan of Different Lintel Materials?
You'll find that climate impacts greatly affect lintel durability. In humid regions, steel lintels can corrode within 15-20 years without proper treatment, while concrete lintels may deteriorate from freeze-thaw cycles. Wood lintels last 25-30 years in dry climates but only 10-15 in wet conditions. For ideal material durability, you'll want to choose stone or reinforced concrete in coastal areas, and powder-coated steel in arid regions.
Can Existing Lintels Be Reinforced Without Complete Replacement?
Yes, you can reinforce existing lintels through several proven techniques. After conducting a thorough structural integrity assessment, you'll have multiple reinforcement options. You can install steel plates beneath the lintel, apply carbon fiber reinforcement polymers (CFRP), or implement angle brackets for additional support. If you're dealing with masonry lintels, you'll find that epoxy injection effectively repairs minor cracks. These lintel reinforcement techniques typically cost 40-60% less than full replacement.
What Are the Cost Differences Between Various Lintel Materials and Installation Methods?
You'll find that lintel pricing varies considerably based on material choice and installation techniques. Steel lintels typically cost $100-200 per linear foot installed, while precast concrete runs $75-150. Timber options are cheaper at $40-80, but they're less durable. Installation costs make up 30-40% of your total expense, with specialized techniques like welded supports or mechanical fixing methods affecting the final price. You're looking at higher costs for complex architectural details or load-bearing requirements.
How Do Seismic Zones Impact Lintel Design and Material Selection?
In seismic zones, you'll need to contemplate dynamic lateral forces when selecting your lintel materials and design. You'll find that steel lintels offer superior design flexibility and can better absorb seismic loads through controlled deformation. For high-risk areas, you'll want to specify ductile materials that can withstand repeated stress cycles. Remember, your lintel's span-to-depth ratio should decrease as seismic risk increases, and you'll typically need deeper sections for adequate support.
Are There Sustainable or Eco-Friendly Alternatives for Traditional Lintel Materials?
You'll find several eco-friendly alternatives to traditional lintel materials that meet structural requirements while reducing environmental impact. Engineered wood products, like glulam beams, offer excellent load-bearing capacity with a 40% smaller carbon footprint than steel. Bamboo lintels, when properly treated, provide impressive strength-to-weight ratios and renewable sourcing. Recycled composites incorporating post-consumer materials are gaining green certifications, while locally-sourced natural stone reduces transportation emissions. These sustainable options don't compromise on performance.