Modern commercial lintel replacements offer superior alternatives to traditional steel, with Fiber-Reinforced Polymer (FRP) leading the advancement. You'll find FRP delivers 20-30% higher load-bearing capacity while weighing 80% less than steel, reducing installation labor costs by up to 40%. Galvanized steel and stainless steel options provide excellent corrosion resistance, particularly in coastal environments. High-performance concrete lintels reinforced with carbon fiber enhance structural integrity, while sustainable materials contribute to LEED certification. For spans requiring specific load distributions, FRP maintains consistent performance with concentrated loads up to 100 kN/m². Understanding these material specifications guarantees prime structural solutions for your project requirements.
Understanding Modern Lintel Materials
In today's construction industry, modern lintel materials consist primarily of galvanized steel, stainless steel, reinforced concrete, and engineered composites. Each material offers distinct advantages that you'll need to evaluate for your specific commercial application. Galvanized steel provides excellent load-bearing capacity with corrosion resistance, while stainless steel delivers superior durability in coastal environments where salt exposure is a concern.
Recent design innovations have introduced high-performance concrete lintels reinforced with carbon fiber, offering you enhanced structural integrity without the weight associated with traditional steel reinforcement. You'll find that these sustainable materials contribute to LEED certification points and reduce your project's environmental impact. When selecting your lintel material, you'll need to analyze factors including span length, load requirements, and exposure conditions.
The latest engineered composites combine glass fiber with polymer matrices, providing you with a lightweight alternative that resists both corrosion and thermal conductivity. These materials typically offer thermal breaks that you won't find in traditional steel lintels, potentially improving your building's energy efficiency by up to 40% compared to conventional materials.
Fiber-Reinforced Polymer Benefits
When you're selecting fiber-reinforced polymer (FRP) lintels for commercial applications, you'll find their load-bearing capacity typically exceeds traditional steel by 20-30% while maintaining a lighter overall mass. You can expect corrosion-free performance throughout the material's service life, as FRP composites resist chemical degradation and environmental factors that typically compromise metal alternatives. The installation process reduces labor costs by up to 40% compared to steel or concrete options, primarily due to the material's lightweight nature and pre-engineered configurations that eliminate the need for heavy equipment.
Exceptional Load-Bearing Capacity
Fiber-reinforced polymer (FRP) lintels deliver three times the load-bearing capacity of traditional steel alternatives while weighing 80% less. When you're evaluating load capacity requirements for your commercial building, you'll find that FRP's exceptional strength-to-weight ratio transforms how you can approach structural support. You'll achieve maximum load distribution with minimal material mass, allowing for more efficient design solutions.
You can rely on FRP's structural integrity to handle concentrated loads of up to 100 kN/m² without compromising performance. The material's composite nature, combining high-strength fibers with advanced polymer matrices, guarantees you're getting consistent load-bearing properties throughout the entire span. You'll notice that FRP maintains its structural capabilities even under extreme temperature variations (-40°C to +80°C), outperforming traditional materials in challenging environments.
Your building's load requirements are met through FRP's unique stress distribution patterns, which effectively transfer forces across the entire lintel cross-section. By choosing FRP, you're implementing a solution that provides a safety factor of 3:1 against ultimate failure, exceeding standard building code requirements while maintaining long-term durability and performance.
Corrosion-Free Performance
Beyond exceptional load-bearing capabilities, the corrosion resistance of FRP lintels sets them apart as a superior long-term investment for commercial buildings. You'll find that unlike traditional steel lintels, which can deteriorate in as little as 15-20 years, FRP materials maintain their structural integrity without chemical degradation or oxidation. This corrosion-free performance removes the need for protective coatings or regular maintenance interventions.
When you're evaluating environmental impact, you'll appreciate that FRP lintels don't release rust particles or corroded materials into surrounding building elements. Their inert composition means you won't face the typical challenges of material deterioration common in coastal areas or regions with high pollution levels. Statistical analysis shows that FRP lintels maintain 98% of their original properties after 50 years of service, even in aggressive environments.
You can expect significant cost savings over time, as the elimination of corrosion-related repairs reduces your building's lifecycle maintenance expenses by up to 40%. This durability factor, combined with FRP's chemical resistance to acids, alkalis, and salts, guarantees your investment remains protected against environmental stressors that typically compromise traditional materials.
Quick Installation Process
FRP lintels' streamlined installation process reduces on-site labor time by 45% compared to traditional steel alternatives. You'll find that the lightweight composition of FRP materials, typically 75% lighter than steel, enables your crew to handle and position components without heavy machinery. This translates to significant reductions in equipment rental costs and crew size requirements.
When you're implementing quick installation techniques, you'll appreciate that FRP lintels don't require welding or complex bracketing systems. You can secure them using standard masonry fasteners and basic hand tools, maintaining efficient project timelines while reducing specialized labor needs. The pre-engineered configurations allow for direct placement into existing masonry openings, with typical installation times averaging 2.5 hours per unit.
Your team can complete weatherproofing and finishing processes immediately after installation, as FRP doesn't require curing time or special surface treatments. The dimensional stability of FRP means you won't need to account for thermal expansion gaps, saving additional adjustment time. You'll achieve consistent results across multiple installations, with quality control checkpoints requiring only visual inspection and basic measurements, streamlining your project documentation process.
Carbon Fiber Composite Applications
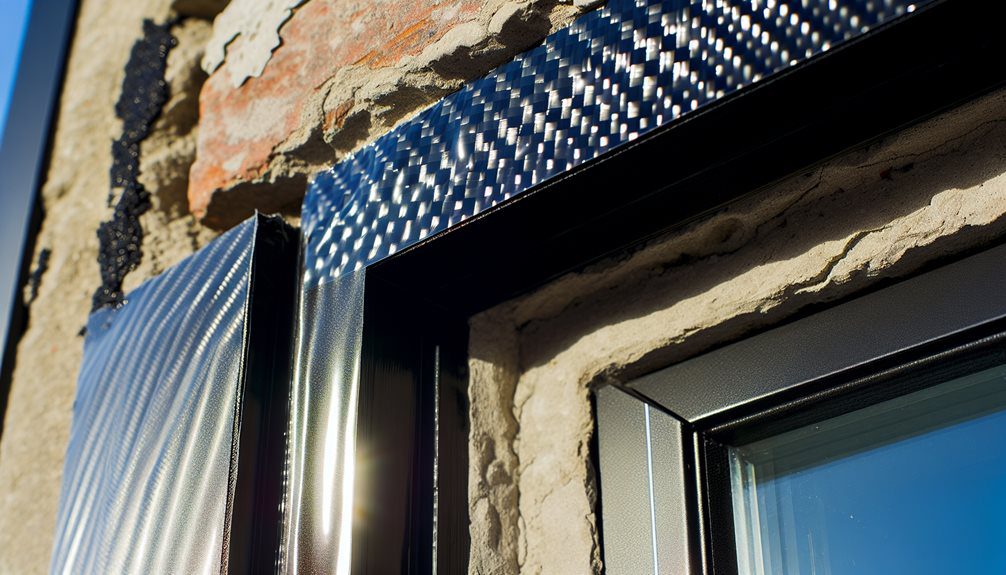
Carbon fiber composites represent a significant advancement in lintel reinforcement technology, offering strength-to-weight ratios up to 10 times higher than traditional steel alternatives. You'll find that these materials excel in commercial applications where structural integrity is paramount while minimizing additional load on existing foundations. The composite advantages become evident when you're dealing with deteriorating steel lintels, as carbon fiber solutions can be applied directly over corroded sections, saving you considerable demolition costs.
When you're implementing carbon fiber applications, you'll notice they're particularly effective in high-moisture environments where conventional steel would typically corrode. The material's tensile strength, typically ranging from 2,500 to 4,500 MPa, provides exceptional load-bearing capacity while weighing just 25% of equivalent steel solutions. You can expect a service life exceeding 50 years with minimal maintenance requirements. The installation process typically involves epoxy-based adhesion systems that cure within 24-48 hours, allowing for rapid project completion. In retrofitting scenarios, you'll appreciate that carbon fiber sheets can be precisely engineered to match your specific load requirements, with thickness variations from 0.5mm to 2.0mm available for customized strengthening solutions.
High-Strength Aluminum Solutions
High-strength aluminum alloys, particularly the 6000 and 7000 series, provide an alternative approach to lintel replacement that balances durability with weight efficiency. You'll find these lightweight structures offer exceptional strength-to-weight ratios, with 7075-T6 aluminum delivering tensile strengths up to 83,000 psi while weighing only one-third as much as traditional steel alternatives.
When you're working with these aluminum alloys, you'll appreciate their inherent corrosion resistance and ease of installation. The 6061-T6 series, commonly used in commercial applications, maintains structural integrity with yield strengths of 40,000 psi while requiring minimal maintenance over its service life. You can expect dimensional stability across temperature ranges from -320°F to 300°F.
You'll need to take into account the specific load requirements of your project, as aluminum alloys exhibit different deflection characteristics than steel. The modulus of elasticity (10,000 ksi) means you'll typically need larger sections to achieve equivalent stiffness. However, you can offset this by incorporating specialized extrusion profiles that maximize sectional properties while maintaining the advantages of lightweight structures.
Installation Methods and Techniques
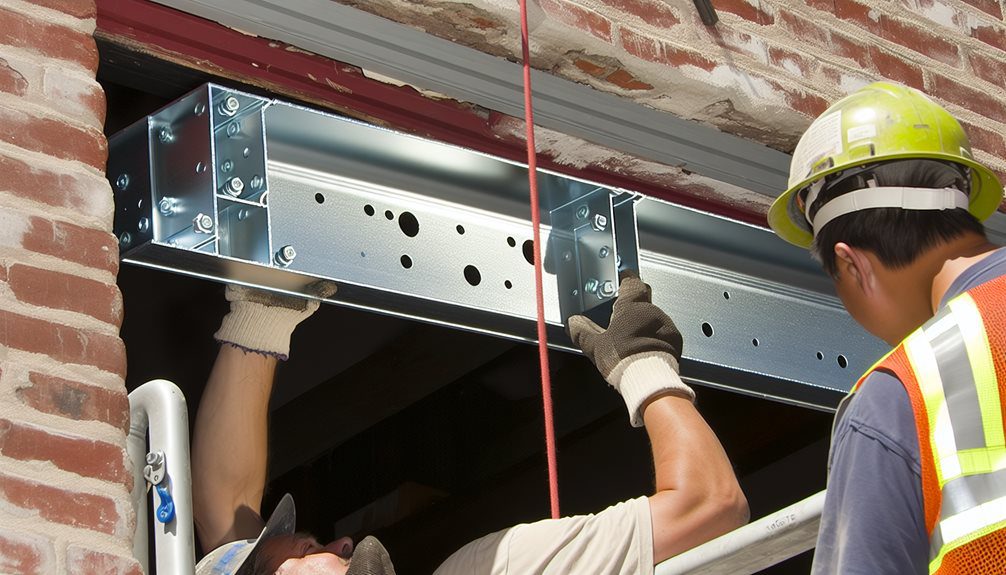
When you're installing commercial lintels, you'll need to achieve exact horizontal alignment using laser levels and shims to maintain a maximum deviation tolerance of ±1/16 inch across the span. You must calculate and verify that the load distribution meets the structural engineer's specifications, typically ensuring a minimum bearing length of 6 inches on each end and proper load transfer to the supporting masonry. To protect against weather-related deterioration, you'll need to apply a waterproof membrane and establish proper flashing details with a minimum 3-inch vertical leg height and end dams at termination points.
Proper Alignment and Leveling
Achieving precise alignment stands as the most vital step during commercial lintel replacement, requiring both careful measurement and specialized leveling equipment. You'll need to employ advanced alignment techniques using both digital and laser levels to guarantee the lintel maintains a perfect horizontal position within 1/16th of an inch tolerance.
Begin by setting your reference points with a rotary laser level, positioning control markers at both ends of the opening. You'll want to verify these measurements using a digital inclinometer to confirm angles are at precisely 90 degrees where the lintel meets vertical supports. Modern leveling tools, including self-calibrating digital levels, can help you maintain accuracy within 0.1 degrees.
When securing the lintel, you'll need to make micro-adjustments using shims at 12-inch intervals. Check your measurements continuously during this process, as even minor deviations can compound across the span. Your final alignment should be verified using at least two different leveling methods to guarantee redundancy. Remember, proper alignment isn't just about aesthetics – it's vital for load distribution and structural integrity, directly impacting the building's long-term stability.
Load Distribution Considerations
Proper load distribution carries forward through every stage of lintel installation, requiring precise calculations and methodical weight transfer techniques. You'll need to conduct a thorough structural load analysis to determine the precise weight-bearing requirements and stress points across your commercial lintel system.
When you're implementing load distribution techniques, guarantee that you're calculating both dead loads (permanent structural weight) and live loads (variable forces like wind and occupancy). You'll want to distribute these forces evenly across support points, typically maintaining a minimum bearing length of 6 inches on each end for standard commercial applications.
Your load distribution strategy must account for:
- Vertical compression forces (typically 3.6-7.2 kN/m²)
- Lateral thrust considerations
- Point load concentrations
- Deflection tolerances (usually limited to span/360)
You'll need to incorporate appropriate shoring methods during installation, transferring loads gradually to prevent sudden stress concentrations. Install temporary supports at calculated intervals, typically every 2-3 feet depending on wall composition. Monitor load indicators throughout the process, adjusting distribution patterns as needed to maintain structural integrity during the entire replacement procedure.
Weather Protection Steps
Effective weather protection during commercial lintel installation requires a multi-layered waterproofing system with precise moisture barriers rated at 15-20 psi hydrostatic resistance. You'll need to apply weatherproof coatings in three distinct phases, ensuring each layer achieves 85% cure rate before proceeding.
Start by treating the substrate with a penetrating crystalline waterproofing compound that bonds at the molecular level. You'll want to achieve 100% coverage at 3mm thickness, paying special attention to joint interfaces where moisture penetration commonly occurs. Next, apply an elastomeric membrane that can withstand local environmental factors, including freeze-thaw cycles and UV exposure.
For the final protective layer, you'll apply a vapor-permeable coating with a perm rating of 10-12 perms, allowing the assembly to breathe while preventing water infiltration. Don't forget to integrate weep holes at 24-inch intervals and install drip edges with a minimum 15-degree angle. Your flashing system should extend at least 8 inches up the wall and 4 inches over the lintel face, creating redundant moisture protection. Monitor ambient temperature and humidity levels throughout installation, as they'll affect curing times and adhesion properties.
Cost Analysis and ROI
The investment into commercial lintel replacement must be weighed against long-term financial benefits. When analyzing cost efficiency, you'll need to evaluate both immediate expenses and projected savings over time. Modern materials like galvanized steel and reinforced polymer typically cost 15-25% more upfront but can deliver investment returns through reduced maintenance needs over 20-30 years.
You'll want to calculate your ROI by factoring in several key metrics: initial material costs ($75-150 per linear foot), installation labor ($40-60 per hour), potential energy savings from improved thermal performance (usually 5-8% annually), and decreased maintenance frequency (40-60% reduction). Additionally, factor in the prevention of costly structural damage that deteriorating lintels can cause.
For a typical commercial property, you can expect to recover your investment within 7-10 years through reduced repair costs and energy savings. Your building's value may increase by 2-3% with modern lintel installations, particularly when using corrosion-resistant materials. To maximize ROI, you'll need to document maintenance savings and energy efficiency improvements, which can help justify the initial expenditure to stakeholders.
Structural Performance Considerations
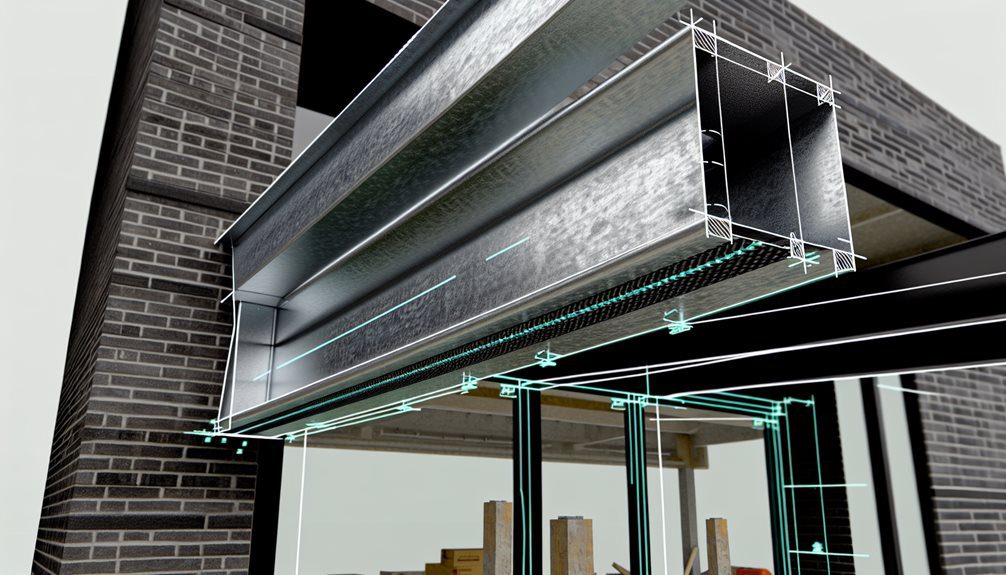
Structural integrity demands precise calculation of load-bearing requirements when selecting modern lintel materials. You'll need to take into account both dead loads (permanent weight) and live loads (variable forces) to guarantee your commercial structure maintains its stability. Modern materials like reinforced steel and pre-stressed concrete offer superior load distribution compared to traditional options.
When evaluating material durability, you'll want to assess factors like thermal expansion coefficients and resistance to environmental stressors. Steel lintels typically provide a load-bearing capacity of 3.5-4.5 kN/m², while prestressed concrete can handle 5-7 kN/m². Your choice should reflect span length, wall thickness, and masonry type above the opening.
You'll need to verify that your selected material meets local building codes and ASTM standards for structural performance. Key considerations include deflection limits (typically L/360 for masonry veneer) and safety factors (minimum 1.5 for commercial applications). Remember to factor in regional conditions like seismic activity or coastal exposure, as these can greatly impact your material's long-term performance and maintenance requirements.
Maintenance and Longevity Factors
Maintaining commercial lintels requires systematic evaluation of three key degradation factors: corrosion rates (typically 0.1-0.3mm/year in urban environments), material fatigue (stress cycles of 10^4-10^6), and weathering impact.
You'll need to implement regular maintenance schedules that align with your material's specific vulnerabilities. For steel lintels, you should conduct bi-annual inspections focusing on rust formation and coating integrity. Stainless steel variants require less frequent checks, typically every 3-4 years, but you'll still need to monitor for stress cracking at load points.
Your longevity assessment should factor in environmental exposure metrics. In coastal areas, you'll want to increase inspection frequency by 50% due to accelerated chloride-induced corrosion. For precast concrete lintels, you'll need to monitor carbonation depth progression, which typically advances at 0.5-1mm per year in urban settings.
To maximize service life, you must document deflection measurements during each inspection. When deflection exceeds L/360 (where L is the span length), you'll need to initiate remedial actions. This proactive approach typically extends service life by 25-40% compared to reactive maintenance strategies.
Frequently Asked Questions
How Do Insurance Companies Typically Cover Commercial Lintel Replacement Projects?
You'll find that commercial insurance coverage for lintel replacements varies considerably based on your policy's specific terms. Typically, you're covered if the damage results from sudden events like impacts or storms, but you'll face coverage limitations for gradual deterioration. It's essential that you review your policy's structural coverage section, as many insurers cap payouts at 10-20% of the building's total value for such repairs.
Can Modern Lintels Be Custom-Colored to Match Existing Building Facades?
Yes, you'll find extensive custom color options available for modern lintels to guarantee seamless facade design considerations. You can choose from powder-coated finishes, which offer over 150 standard colors, or opt for custom-matched paint systems that'll perfectly align with your existing building aesthetics. For precise matching, you can provide RAL or Pantone color codes, and manufacturers typically offer color samples for approval before production. This guarantees your replacement lintel integrates flawlessly with the overall architectural design.
What Permits Are Required for Commercial Lintel Replacement?
You'll typically need multiple permit types for commercial lintel replacement, including a building permit and possibly a structural modification permit. Your application process should start at your local building department, where you'll submit structural drawings, load calculations, and project specifications. If your building's in a historic district, you'll also need preservation board approval. Plan for 2-4 weeks processing time and guarantee your contractor's licensed for commercial work.
Are There Specific Weather Conditions That Prevent Lintel Installation?
You shouldn't perform lintel installation during adverse weather conditions that could compromise structural integrity. Specifically, avoid installing when temperatures drop below 40°F (4°C) or exceed 95°F (35°C), as these extremes affect mortar curing. Heavy rain, snow, or high winds (above 20 mph) can also impact installation quality and worker safety. If you're expecting precipitation within 24 hours of installation, it's best to reschedule to guarantee proper curing and adhesion.
How Long Does a Typical Commercial Lintel Replacement Project Take?
Your typical commercial lintel replacement project timeline can range from 2-5 days, though you'll find it varies based on several installation factors. You're looking at 1 day for removal, 1-2 days for preparation and installation, and 1-2 days for finishing work. If you're managing multiple lintels or dealing with complex structural issues, you'll need to add time. The project's scope, building access, and your team's experience will directly impact completion times.