You'll encounter several critical issues with industrial chimneys that require immediate attention. Common problems include structural cracks, creosote buildup, draft malfunctions, liner deterioration, and environmental damage. To address these concerns, implement regular professional inspections, establish systematic maintenance protocols, and document all findings. Schedule quarterly cleanings to prevent hazardous deposit accumulation, and monitor pressure systems to avoid dangerous backdrafting. Don't attempt repairs without certified specialists, as improper interventions can compromise safety. Understanding the full scope of industrial chimney maintenance will greatly enhance your facility's operational safety and compliance.
Structural Cracks and Deterioration
Cracks and deterioration in your chimney's structure pose serious safety risks that require immediate attention. As a facility manager, you'll need to implement regular crack detection protocols to identify issues before they become catastrophic. Look for vertical, horizontal, or diagonal fissures in the masonry, particularly around stress points where the chimney meets the building structure.
When you spot early signs of deterioration, you'll want to document their location, size, and progression rate. Your maintenance team should examine mortar joints, brick faces, and foundation areas where water infiltration commonly occurs. Don't overlook hairline cracks, as they'll often expand during freeze-thaw cycles.
Modern repair techniques vary based on damage severity. You might need to evaluate tuckpointing for mortar joint issues, while more substantial cracks may require steel reinforcement or partial rebuilding. If you're dealing with spalling bricks, they'll need replacement to maintain structural integrity. Remember, your industrial chimney's stability affects workplace safety and operational efficiency. By addressing structural issues promptly, you're protecting your team and maintaining compliance with industrial safety standards. Always work with certified industrial chimney specialists who understand the complexities of large-scale industrial stacks. Additionally, regular inspections are essential to identify early signs of damage that could lead to more severe issues.
Creosote and Chemical Deposits
Beyond structural integrity concerns, the accumulation of creosote and chemical deposits inside your chimney presents significant fire and health hazards. When you're operating industrial heating systems or processing equipment, you'll notice that creosote buildup occurs gradually as a natural byproduct of combustion. This sticky, tar-like substance adheres to your chimney's inner walls and can ignite if temperatures rise too high.
You'll need to implement a regular inspection schedule to monitor deposit levels and chemical corrosion. For industrial chimneys, you should conduct professional cleanings at least quarterly, though your specific schedule will depend on usage patterns and the materials being burned. If you're noticing a strong, acrid smell or seeing black, oily residue around your chimney's outlet, you're already facing dangerous accumulation levels.
To protect your facility and team, make certain you're using appropriate fuel types and maintaining ideal combustion temperatures. Install monitoring systems to track flue gas composition and temperature. You'll also want to document all cleaning procedures and maintain detailed inspection records to guarantee compliance with safety regulations and insurance requirements.
Draft and Ventilation Problems
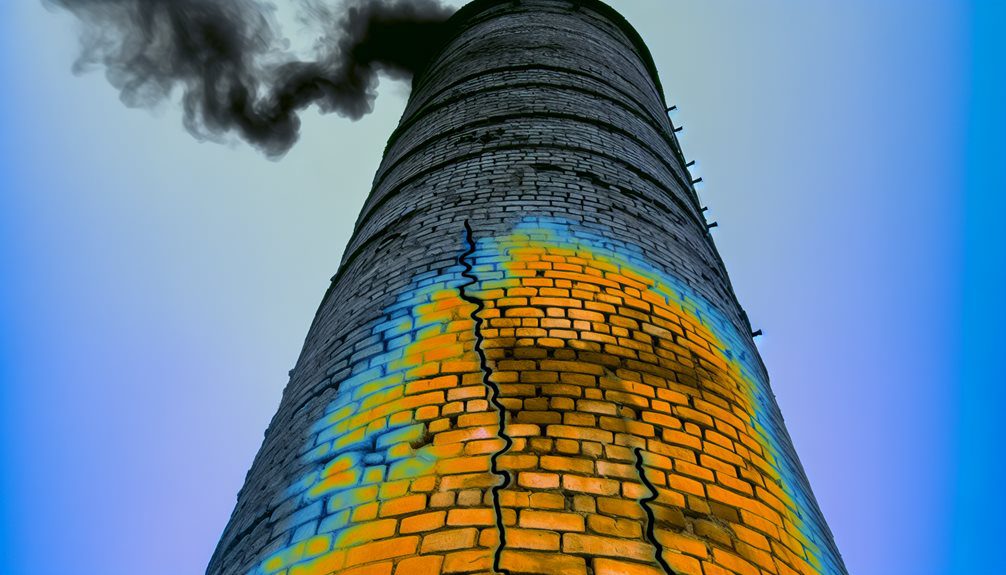
Your home's chimney draft issues can stem from negative air pressure when appliances like bathroom fans or kitchen hoods compete for air, causing smoke to back up into living spaces. Insufficient stack height prevents proper exhaust flow, as chimneys must extend above the roof's highest point to create adequate draw and maintain safe venting conditions. Blocked exhaust flow, often caused by debris, bird nests, or deteriorating chimney liners, disrupts the critical upward movement of combustion gases and requires immediate professional attention.
Negative Air Pressure Effects
Many homeowners experience negative air pressure problems in their chimneys, which can disrupt proper ventilation and create potentially hazardous conditions. When your home's air pressure becomes lower than the outdoor pressure, you'll notice smoke and combustion gases being pushed back into your living space instead of rising up the chimney.
You can identify negative pressure issues through several warning signs: smoke entering your room, difficulty starting fires, or unusual odors coming from your fireplace. Modern homes with tight seals and multiple exhaust appliances are particularly susceptible to these problems. Your kitchen hood, bathroom fans, and clothes dryer all compete for air, potentially creating negative pressure zones.
To address these issues, you'll need to guarantee proper air supply to your home. Consider installing an air intake vent near your fireplace or adding a makeup air system. You should also check that your chimney cap isn't restricting airflow and that your flue is properly sized. Regular maintenance of your ventilation system will help maintain ideal air quality and prevent dangerous backdrafting. If you're unsure about your home's pressure balance, consult a certified chimney professional for an evaluation.
Insufficient Stack Height Issues
Determining proper chimney stack height stands as a critical factor in maintaining ideal draft performance and ventilation efficiency. You'll find that insufficient stack height can lead to serious operational issues, including poor combustion, backdrafting, and potential code violations. When your stack height doesn't meet minimum requirements, you're likely to experience reduced draft pressure and compromised ventilation.
To address these concerns, you'll need to conduct a thorough stack performance analysis. This evaluation should account for surrounding buildings, terrain, and local weather patterns that might affect airflow. You'll want to guarantee your stack height complies with current emission regulations while providing adequate draft for your specific application.
If you're experiencing draft issues, consider these key indicators: smoke spillage at appliance connections, excessive soot buildup, or poor combustion efficiency. You can improve performance by extending your stack height, but you'll need to calculate the proper elevation based on technical factors like flue gas volume, temperature, and building configuration. Remember that modifications must align with local building codes and environmental standards. Working with certified professionals guarantees your stack height modifications meet both operational needs and regulatory requirements.
Blocked Exhaust Flow Problems
A chimney's blocked exhaust flow represents one of the most dangerous ventilation issues homeowners face, often resulting in carbon monoxide buildup and compromised draft performance. You'll need to recognize common blockage sources, including creosote buildup, bird nests, fallen debris, and collapsed liner materials that notably reduce exhaust efficiency.
To identify blocked airflow problems, watch for warning signs like smoke backing up into your home, unusual odors, or soot accumulation around your fireplace or appliance vents. If you're experiencing these symptoms, it's essential to take immediate action to protect your household's safety.
You can prevent many blockage issues through regular maintenance. Schedule annual inspections by a certified chimney professional who'll check for obstructions and clean your system as needed. They'll also verify that your chimney cap remains intact and properly positioned to prevent debris and animals from entering while maintaining proper ventilation. Additionally, consider investing in waterproofing solutions to protect your chimney from moisture damage that could contribute to blockages.
Don't attempt to clear major blockages yourself, as this can be dangerous and may damage your chimney system. If you suspect a blocked exhaust flow, shut down your heating appliance immediately and contact a qualified professional for assessment and repairs.
Liner System Damage
Damage to your chimney's liner system poses significant safety risks and requires immediate professional attention. When you notice deterioration in your industrial chimney liner, you'll need to assess several liner replacement options based on your facility's specific requirements. The most common materials include stainless steel, aluminum, and ceramic, each offering distinct advantages for different industrial applications.
You'll want to evaluate the extent of the damage through professional inspection, which typically involves camera monitoring and pressure testing. If you've got cracking, flaking, or separation in your current liner, you're at risk for dangerous gas leaks and potential structural compromise. Modern installation techniques have evolved to include cast-in-place systems and thermocured liners that provide superior protection against corrosive byproducts.
Your maintenance team should document any changes in draft performance, as this often indicates liner system issues. When selecting a replacement system, you'll need to take into account factors like flue gas temperatures, fuel types, and condensation levels. Remember that proper sizing and professional installation are essential for maintaining your facility's safety compliance and operational efficiency. Regular inspections will help you identify potential problems before they become critical failures.
External Environmental Impact
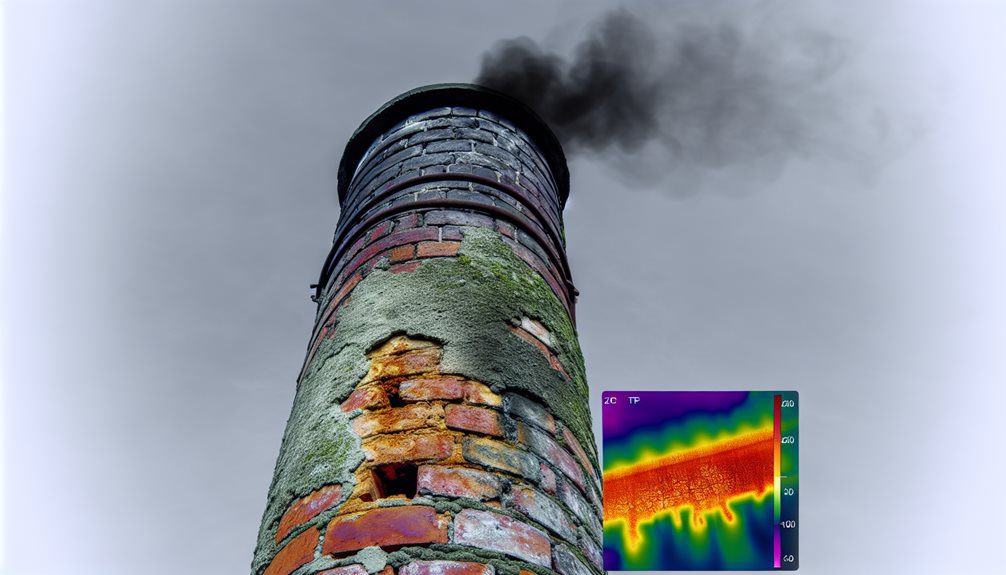
Environmental factors constantly assault your chimney's exterior, leading to accelerated deterioration and potential structural risks. You'll notice that weather effects like freeze-thaw cycles, acid rain, and extreme temperature fluctuations can compromise your chimney's structural integrity. Wind-driven rain penetrates brick and mortar joints, while UV exposure gradually breaks down protective sealants.
As part of your industrial facility team, you'll need to monitor pollution impact carefully. Acidic industrial emissions from neighboring facilities can accelerate masonry deterioration, especially in dense manufacturing zones. Salt air exposure in coastal locations intensifies corrosion of metal components and deterioration of mortar joints. You're also likely to encounter biological growth such as moss and algae, which trap moisture against surfaces and accelerate decay.
To protect your investment, implement a regular inspection schedule focusing on exterior damage patterns. You'll want to document weather-related wear, check for efflorescence (white mineral deposits), and assess pollution staining. Don't wait for visible damage – proactive maintenance, including waterproofing and surface treatments, will help your chimney withstand these environmental challenges and maintain compliance with safety regulations. Additionally, applying a siloxane clearcoat can significantly enhance your chimney's resistance to moisture penetration.
Maintenance and Inspection Protocols
Regular maintenance and inspection protocols form the backbone of effective chimney management. You'll need to establish a systematic approach that includes both routine checks and detailed assessments to guarantee your industrial chimney's peak performance and longevity.
Start by implementing preventive measures through a structured maintenance schedule. You should conduct monthly visual inspections of accessible components, checking for visible cracks, deterioration, or unusual deposits. Your quarterly inspections must include thorough examinations of liner conditions, damper operations, and cap integrity.
Create thorough inspection checklists that cover all critical components. You'll want to document: structural integrity, draft performance, interior surface conditions, and exterior masonry status. Don't forget to monitor your emission control systems and verify that all safety devices are functioning correctly.
Schedule professional assessments annually, focusing on areas you can't easily access. You're responsible for maintaining detailed records of all inspections, repairs, and modifications. These records will help you track deterioration patterns and anticipate potential issues before they become critical problems. Remember to update your protocols based on inspection findings and changing regulatory requirements. Additionally, it's crucial to include chimney repair as part of your maintenance strategy to prevent leaks and deterioration.
Frequently Asked Questions
How Long Does a Typical Industrial Chimney Last Before Requiring Replacement?
You'll find that industrial chimney lifespan factors typically indicate a 15-30 year service life, though well-maintained systems can last up to 50 years. Your maintenance schedules play a vital role: regular inspections, cleaning, and repairs can greatly extend longevity. As part of your facility team, you'll want to monitor key indicators like deterioration, cracks, or liner damage. Remember, harsh operating conditions and frequency of use will impact your chimney's lifespan.
Can Industrial Chimneys Be Retrofitted With Modern Emission Control Systems?
Yes, you can retrofit your industrial chimneys with modern emission control systems to achieve emission compliance. The process typically involves installing scrubbers, filters, or catalytic converters within your existing stack system. During chimney retrofitting, you'll need to assess structural integrity, calculate proper dimensions, and guarantee adequate support for the new equipment. It's essential to work with certified engineers who'll help you meet current environmental regulations while maintaining ideal stack performance.
What Certifications Do Industrial Chimney Inspectors Need?
You'll need specific certification requirements to become an industrial chimney inspector. The key qualifications include NACE (National Association of Corrosion Engineers) certification, API (American Petroleum Institute) credentials, and ASNT (American Society for Nondestructive Testing) Level II or III certification. You should also obtain confined space training and OSHA safety certifications. Many employers will require that you're certified through the International Code Council (ICC) as a commercial building inspector.
How Often Should Industrial Chimney Temperature Monitoring Systems Be Calibrated?
You'll need to calibrate your industrial chimney temperature sensors at least every 12 months to maintain accuracy and safety compliance. However, if you're operating in harsh environments or running high-temperature processes, you should increase your calibration frequency to every 6 months. Don't forget to document each calibration for regulatory purposes. Remember, you're part of a community that prioritizes safety – many of your fellow facility managers follow these same calibration schedules to guarantee peak performance.
Are There Specific Insurance Requirements for Industrial Chimney Maintenance?
You'll find that most insurance providers require strict adherence to maintenance standards for industrial chimneys to maintain valid coverage. You should review your policy carefully, as it'll typically mandate annual inspections, documented maintenance logs, and compliance with OSHA regulations. Your insurance coverage might also specify required safety certifications for maintenance personnel and emergency protocols. Don't forget to keep detailed records of all maintenance activities, as they're often necessary for claims processing.