Proper waterproofing can greatly extend your commercial building's lifespan while protecting your investment from costly water damage. You'll find that an integrated waterproofing system, comprising multiple defensive layers from exterior barriers to interior sealants, serves as your first line of defense against moisture threats like basement seepage, pipe condensation, and roof membrane failures. By implementing thorough waterproofing solutions, you'll reduce repair costs by 80-85% compared to addressing major water damage after the fact. Professional installation and regular maintenance of these systems guarantee peak performance and compliance with building codes. Understanding the full scope of waterproofing benefits can transform your approach to building preservation.
Understanding Commercial Waterproofing Systems
Commercial waterproofing systems comprise multiple integrated components that work together to protect building structures from water damage and moisture infiltration. When you're selecting a waterproofing system for your facility, you'll need to understand how various waterproofing methods complement each other to create extensive protection.
Your building's waterproofing system should include multiple layers of defense, starting with exterior barriers like membrane systems and moving inward to interior sealants and coatings. System integration is vital – each component must seamlessly connect with others to prevent weak points where water might penetrate. You'll find that modern waterproofing methods include positive-side barriers applied to exterior surfaces, negative-side treatments for interior walls, and blind-side solutions for areas with limited access.
The effectiveness of your waterproofing system depends on proper installation sequence and compatibility between materials. You'll want to ascertain that drainage systems, vapor barriers, and waterproof membranes work in concert to direct water away from vulnerable areas. Understanding these relationships helps you make informed decisions about maintenance schedules and system upgrades, ultimately protecting your investment in the building's infrastructure. Additionally, implementing techniques such as siloxane clearcoat can enhance the waterproofing effectiveness without altering the appearance of masonry surfaces.
Common Moisture Threats
Three major moisture threats can compromise your commercial building's integrity: basement wall seepage from hydrostatic pressure and poor drainage, hidden pipe condensation that accelerates metal corrosion and promotes mold growth, and roof membrane failures that lead to costly structural damage. You'll need to monitor these issues systematically, as moisture intrusion often manifests through multiple pathways simultaneously. Your building's defense strategy must incorporate proper drainage systems, pipe insulation protocols, and regular roof membrane inspections to prevent these common water-related problems from escalating into major structural concerns. Additionally, implementing waterproofing solutions can significantly enhance your building's resilience against moisture damage.
Basement Wall Seepage Issues
Several persistent moisture threats plague commercial basement walls, making professional waterproofing essential for structural integrity. You'll find that hydrostatic pressure constantly pushes against foundation walls, while water tables fluctuate seasonally, creating varying degrees of moisture exposure. When you're dealing with these issues, it's vital to implement thorough basement drainage solutions before structural damage occurs.
Your building's vulnerability to seepage often stems from inadequate moisture barrier installation during initial construction or deteriorating waterproofing systems. You'll need to watch for telltale signs: efflorescence on walls, dampness around floor-wall joints, and musty odors that indicate active water infiltration. These symptoms typically worsen during heavy rainfall or spring thaws.
To protect your investment, you'll want to address both interior and exterior waterproofing measures. This includes installing proper drainage systems, applying crystalline waterproofing compounds, and ensuring adequate surface grading. Additionally, a certified masonry professional can help assess and remedy any existing waterproofing issues effectively. When you're maintaining commercial property, remember that basement wall seepage isn't just about water damage – it's about preserving your building's structural integrity and protecting your tenants' assets from moisture-related complications.
Hidden Pipe Condensation Problems
While basement seepage often draws immediate attention, pipe condensation represents an equally significant moisture threat lurking within your building's infrastructure. You'll find this issue particularly prevalent in areas where temperature differentials cause water vapor to collect on cold pipe surfaces, leading to persistent dripping and potential structural damage.
Your building's hidden moisture detection systems should focus on areas where condensation commonly occurs: mechanical rooms, ceiling voids, and wall cavities containing plumbing runs. You're likely to encounter the most severe condensation problems where uninsulated cold water pipes pass through warm, humid spaces. Without proper condensation control measures, you're risking not only physical deterioration of building materials but also the growth of harmful mold and mildew.
To protect your investment, implement a thorough pipe insulation strategy and install moisture sensors at critical points throughout your building's plumbing network. You'll want to pay special attention to areas where HVAC ducts intersect with water lines, as these junctions often create ideal conditions for condensation formation. Regular infrared scanning can help you identify developing moisture issues before they escalate into costly repairs. Additionally, consider waterproofing services to further enhance your building's protection against moisture intrusion.
Roof Membrane Failure Risks
On commercial roofs, membrane failures represent one of the most destructive sources of moisture infiltration you'll encounter. When your building's roof membrane loses its integrity, you're facing potential structural damage that can cascade throughout your facility. The most common membrane failure points occur at seams, penetrations, and areas where mechanical stress concentrates.
You'll need to watch for telltale signs of impending roof leaks, including blistering, splitting, and membrane shrinkage. These issues often develop when thermal cycling causes repeated expansion and contraction, gradually compromising membrane durability. Your maintenance team should regularly inspect flashings, as they're particularly vulnerable to separation and weathering.
Don't overlook the impact of standing water, which can accelerate membrane deterioration. If you're noticing ponding that persists for more than 48 hours after rainfall, your drainage system likely requires immediate attention. Poor installation practices, such as inadequate membrane attachment or improper seam welding, can also lead to premature failure. By identifying these risks early and implementing preventive measures, you'll protect your investment and avoid costly emergency repairs that disrupt operations.
Financial Benefits of Early Prevention

Investing in early waterproofing prevention delivers substantial returns that greatly outweigh initial costs. You'll discover that proactive waterproofing measures typically cost 15-20% of what you'd spend on major repairs after water damage occurs. This cost savings extends beyond immediate repair expenses, encompassing reduced insurance premiums and decreased maintenance budgets over your building's lifecycle.
Your risk management strategy should prioritize early detection and prevention of water infiltration. When you implement thorough waterproofing solutions during initial construction or early maintenance phases, you're protecting your investment from structural deterioration, mold remediation, and tenant displacement costs. You'll avoid business interruption losses that often exceed $10,000 per day in commercial settings. Additionally, regular inspections and maintenance can help ensure compliance with municipal code violations that may arise from water damage.
Building Code Requirements
Building codes for commercial waterproofing exist at both national and local levels, with your jurisdiction's requirements potentially exceeding the International Building Code's baseline standards. You'll need to comply with essential safety regulations that specify minimum membrane thicknesses, drainage requirements, and hydrostatic pressure resistance ratings for below-grade applications. Your building must pass rigorous testing protocols, including flood testing for horizontal surfaces and spray testing for vertical installations, to verify the waterproofing system's effectiveness. Additionally, it's crucial to ensure that the waterproofing methods align with masonry restoration practices to maintain structural integrity.
Local vs. National Standards
Multiple waterproofing standards exist across local jurisdictions and national building codes, creating a complex framework that commercial building owners must navigate. You'll need to comply with both local regulations and national guidelines, as they often complement each other but can sometimes conflict in their requirements.
When you're planning your commercial building's waterproofing system, you'll discover that local standards frequently exceed national minimums to address region-specific challenges like heavy rainfall, flooding, or seismic activity. Your local building department might require additional moisture barriers or specific installation methods that aren't mentioned in national codes.
National guidelines, such as those from the International Building Code (IBC) and ASTM standards, provide your baseline requirements. However, you must verify your local jurisdiction's specific demands, which could include enhanced below-grade waterproofing, specialized roof membrane specifications, or particular testing protocols. You'll find that working with a local waterproofing consultant who understands both sets of standards will help guarantee your building meets all applicable requirements while achieving ideal protection against water intrusion. Additionally, investing in professional masonry services can further enhance the durability and waterproofing effectiveness of your building's structure.
Essential Safety Regulations
Under current building codes, commercial waterproofing must adhere to specific safety regulations that protect both occupants and property. You'll need to guarantee your waterproofing systems meet both federal and state-mandated safety standards, which typically include proper drainage requirements, moisture barrier specifications, and structural integrity guidelines.
When you're implementing waterproofing measures, you'll find that regulatory compliance involves multiple layers of protection. You must install vapor barriers that meet minimum thickness requirements, typically 10-15 mil for commercial applications. Your drainage systems should handle water volumes specified by local watershed calculations, and you'll need to maintain detailed documentation of all installations and inspections.
As a building owner or manager, you're required to schedule regular inspections of your waterproofing systems. These assessments must be performed by certified professionals who'll verify that your moisture protection meets current codes. You'll also need to maintain updated safety certificates and inspection records. If you're retrofitting an existing structure, you must bring all waterproofing components up to current standards, even if they were compliant when originally installed. Additionally, ensuring proper brick repair is crucial for the overall effectiveness of your waterproofing systems.
Required Testing Protocols
Commercial waterproofing systems require rigorous testing protocols to verify their effectiveness and code compliance. You'll need to follow established testing methods that assess water penetration resistance, hydrostatic pressure tolerance, and membrane integrity. These protocols aren't optional – they're mandatory requirements that protect your investment and guarantee regulatory compliance.
Your testing program must include thorough inspection guidelines that cover both installation quality and material performance. You'll need to conduct water testing using standardized procedures like AATCC Test Method 127 for hydrostatic pressure and ASTM D5957 for seam strength. Don't forget to document flood testing results, which typically require a minimum 24-hour observation period with 2 inches of standing water.
Remember that you're required to verify the entire system's performance, not just individual components. This means you'll need to test all critical junctions, penetrations, and changes. Your testing protocol should also include adhesion testing, thickness measurements, and electronic leak detection when applicable. By following these standardized testing procedures, you're confirming your waterproofing system meets industry standards and building code requirements while protecting your structure's integrity.
Modern Waterproofing Technologies
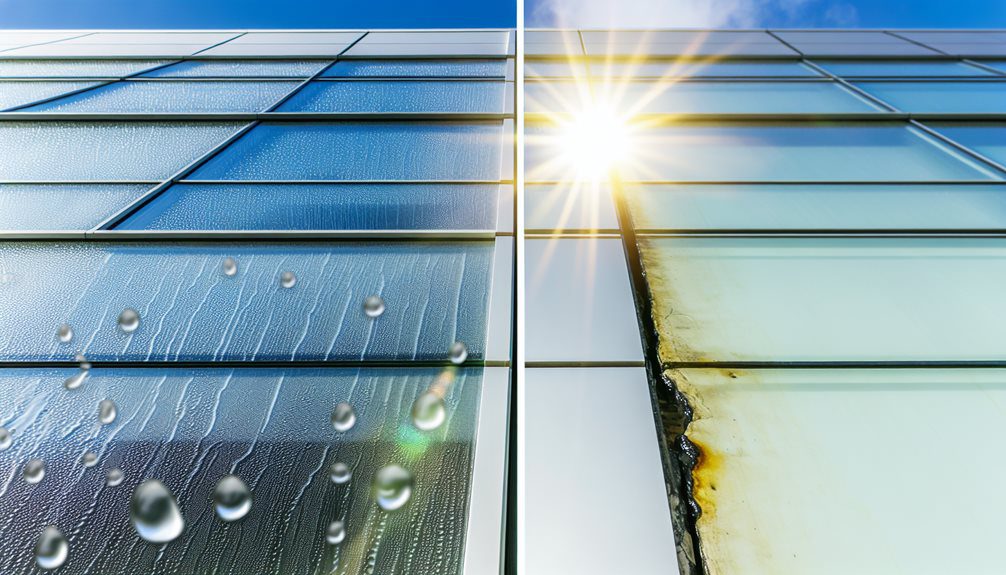
Recent advancements in waterproofing technologies have revolutionized how we protect commercial structures from water damage. You'll find that today's advanced coatings offer unprecedented protection while meeting stringent environmental standards. These innovative solutions include crystalline waterproofing additives, thermoplastic membranes, and nano-engineered materials that penetrate deep into substrate surfaces.
When you're selecting modern waterproofing systems, you'll want to evaluate sustainable solutions that combine durability with eco-consciousness. Smart membrane systems now feature self-healing properties and real-time moisture detection capabilities. You can monitor your building's moisture levels through integrated sensors that alert you to potential breaches before they become problematic.
Polyurethane-modified bitumen systems have emerged as a leading choice, offering superior flexibility and durability compared to traditional materials. You'll benefit from their seamless application and extended service life. Additionally, spray-applied elastomeric coatings provide excellent adhesion and can conform to irregular surfaces, making them ideal for complex architectural details. These technologies aren't just improvements on old methods – they're completely new approaches to keeping your commercial building dry and protected.
Signs of Water Damage
Detecting water damage early in your commercial building requires vigilant monitoring of key warning signs. You'll want to regularly inspect walls, ceilings, and floors for water stains, which often appear as yellowish-brown discolorations with irregular patterns. These telltale marks typically indicate water infiltration from above or behind the affected surface.
As a property manager, you're likely aware that mold growth serves as another significant indicator of moisture problems. Look for dark spots or patches, especially in corners, behind furniture, and around windows. You'll also need to pay attention to subtle changes like peeling paint, bubbling wallpaper, or warped building materials. These issues often suggest ongoing water penetration that's compromising your building's integrity.
Don't overlook less obvious signs like musty odors, increased humidity levels, or unexplained increases in utility bills. Your HVAC system may work harder to compensate for excess moisture, leading to higher energy consumption. If you notice concrete spalling, rusted metal fixtures, or deteriorating mortar joints, you're likely dealing with serious water intrusion that requires immediate professional assessment and remediation. Additionally, it's crucial to consider waterproofing solutions as a proactive measure to protect your building from potential damage.
Preventive Maintenance Strategies
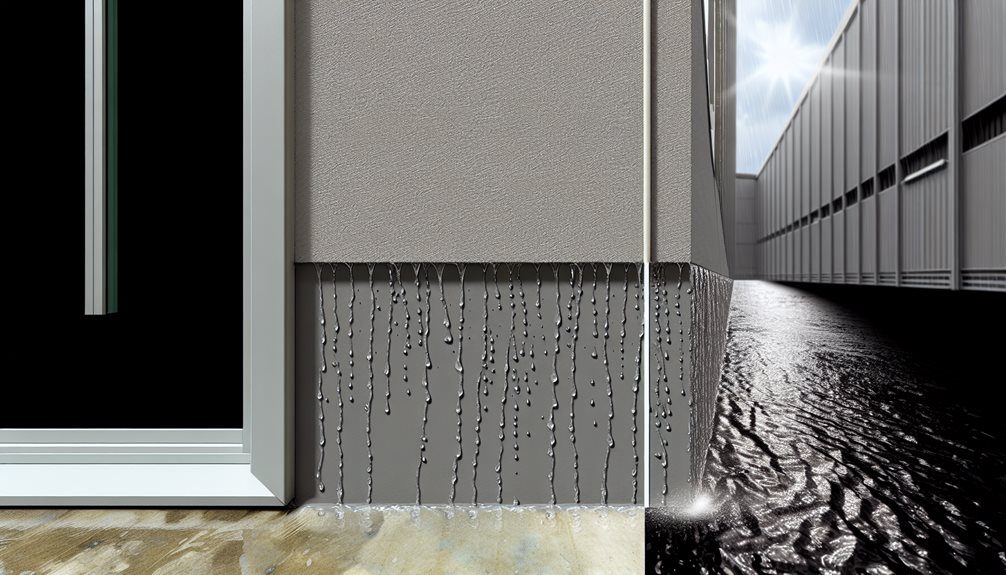
In accordance with industry best practices, implementing an extensive preventive maintenance program stands as your first line of defense against water damage. You'll need to establish routine inspections that encompass your building's entire envelope, including roofing systems, foundation walls, and drainage components. By joining other successful property managers who've adopted systematic maintenance schedules, you're protecting your investment while becoming part of a community that values proactive facility management.
Your maintenance strategy should include quarterly assessments of all waterproofing membranes, sealants, and flashings. You'll want to document any signs of deterioration and address them before they escalate into costly repairs. It's vital to keep detailed records of all inspections and repairs, as you're building a valuable database that'll inform your future maintenance decisions. Additionally, consider incorporating professional tuckpointing services to enhance the durability of your building's masonry.
Don't forget to clean your drainage systems regularly – gutters, downspouts, and storm drains require monthly attention. You'll also need to test your sump pumps and backup systems every quarter. When you follow these proven maintenance protocols, you're joining ranks with building owners who consistently achieve superior protection against water infiltration.
Environmental Impact Considerations
Modern waterproofing practices must balance building protection with environmental responsibility. When you're selecting waterproofing solutions, you'll need to evaluate their full environmental impact, from manufacturing to disposal. Today's sustainability practices emphasize using eco-friendly materials that minimize harm to both the environment and human health.
You'll want to prioritize water-based sealants and VOC-compliant membranes that don't release harmful chemicals into the atmosphere. These products aren't just better for the environment; they'll also help you comply with increasingly stringent building codes and environmental regulations. Contemplate implementing green roofing systems that complement your waterproofing strategy while reducing urban heat island effects.
As part of our industry, you'll find that recycled and renewable materials are becoming more prevalent in waterproofing applications. Look for products made from recycled rubber or sustainable plant-based polymers. When you're planning your waterproofing project, factor in the product's lifecycle assessment, including its durability and eventual disposal impact. By choosing materials that last longer and can be recycled, you're contributing to reduced landfill waste while maintaining effective building protection.
Material Selection and Application
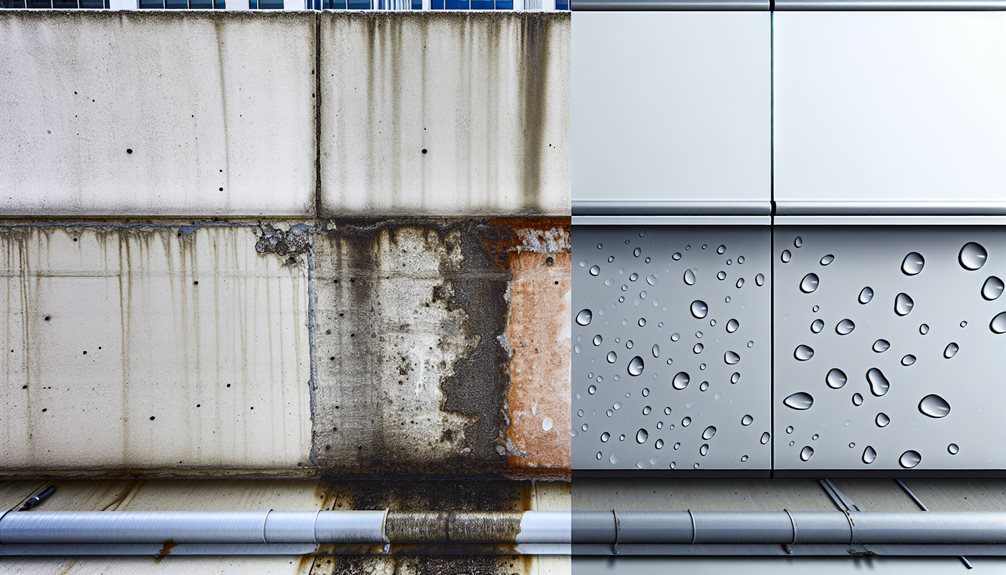
When selecting waterproofing membranes for your commercial building, you'll need to assess product specifications for tensile strength, elongation properties, and chemical resistance to guarantee peak performance in your specific environment. You must thoroughly prepare surfaces by addressing cracks, removing debris, and achieving proper moisture content before applying any waterproofing materials. The success of your waterproofing system depends on precise application techniques, including maintaining consistent membrane thickness and guaranteeing proper overlap at seams.
Choosing Quality Membrane Products
Selecting appropriate waterproofing membrane products stands as the cornerstone of effective building envelope protection. You'll need to evaluate several key factors to verify you're choosing the right solution for your commercial structure. Consider membrane durability as your primary criterion, focusing on products that offer proven resistance to UV exposure, temperature fluctuations, and mechanical stress.
When you're reviewing membrane options, you'll want to examine the manufacturer's technical data sheets for essential performance metrics. Look for products with elongation properties exceeding 300%, tensile strength ratings appropriate for your climate zone, and documented resistance to puncture and tear. Installation techniques will greatly impact your membrane's effectiveness, so you'll need to select products that align with your team's expertise and available equipment.
Don't overlook the membrane's compatibility with your building's substrate materials and existing waterproofing systems. You'll find that self-adhering membranes often provide excellent adhesion and simplified installation, while heat-welded options deliver superior seam strength. Remember to verify warranty terms and ascertain the manufacturer provides thorough technical support for your specific application requirements.
Surface Preparation Techniques
Proper surface preparation serves as the foundation for successful waterproofing membrane installation. You'll need to guarantee your substrate is clean, dry, and structurally sound before applying any waterproofing materials. Surface preparation methods include mechanical grinding, shot blasting, or pressure washing to remove contaminants, loose materials, and previous coatings.
Begin your surface cleaning techniques by addressing visible defects. You'll want to repair cracks, holes, and spalled areas using appropriate patching compounds. It's critical to achieve the correct moisture content – test the substrate using moisture meters and perform calcium chloride testing when necessary. For concrete surfaces, you must reach a minimum compressive strength of 3000 psi and allow proper curing time.
Remove all dirt, dust, and debris using industrial vacuums. If you're dealing with oil or grease contamination, use specialized degreasers and follow with thorough rinsing. Don't forget to protect adjacent areas that won't receive waterproofing treatment. Check weather conditions before starting, as temperature and humidity can affect adhesion. You'll also need to verify that the substrate's pH levels fall within the manufacturer's specified range.
Warranty and Insurance Implications
Most commercial waterproofing systems come with extensive warranty coverage, but the specific terms can greatly impact your building's insurance requirements and long-term liability protection. You'll need to carefully review warranty documentation to understand coverage limitations, maintenance requirements, and conditions that could void your protection. Standard warranties typically range from 5 to 20 years, though you'll find that premium systems may offer up to 30-year guarantees.
When you're evaluating warranty options, you'll want to take into account how they align with your insurance provider's requirements. Many insurers offer reduced premiums for buildings with thorough waterproofing warranties, as these systems minimize the risk of water damage-related insurance claims. You'll need to maintain detailed records of installation, inspections, and any repairs to guarantee warranty compliance and support potential claims. It's vital to understand that most warranties won't cover damage resulting from improper maintenance or unauthorized modifications. You should also verify that your chosen waterproofing contractor maintains adequate liability insurance and is authorized to install the specified system, as unauthorized installation can invalidate manufacturer warranties and complicate future insurance claims.
Frequently Asked Questions
How Long Does a Professional Waterproofing Inspection Typically Take to Complete?
You'll find that a professional waterproofing inspection duration typically ranges from 2-4 hours, though it'll depend on your building's size and complexity. During this professional assessment, you can expect the inspector to examine foundations, walls, joints, and drainage systems. They'll use moisture meters and thermal imaging to identify potential issues. For larger commercial properties, you might need to allocate a full day to guarantee every critical area receives thorough attention.
Can Waterproofing Be Done During Winter Months in Cold Climates?
While you can perform winter waterproofing, you'll need to carefully consider cold climate considerations. Most waterproofing materials require specific temperature ranges (typically above 40°F/4°C) to cure properly. You'll want to use specialized cold-weather products and guarantee surfaces are completely dry and frost-free. If you're working with liquid membranes, you'll need to create a controlled environment using heated enclosures. It's often more challenging and costly, but it's not impossible.
What Qualifications Should I Look for When Hiring Waterproofing Contractors?
When selecting waterproofing contractors, you'll want to verify their contractor experience spanning at least 5-10 years in commercial waterproofing specifically. Confirm they hold proper state licensing requirements and certifications from recognized industry bodies. You should also look for contractors who carry extensive insurance, can provide detailed project portfolios, and offer references from similar projects. Don't forget to check their standing with the Better Business Bureau and local contractor associations.
How Does Landscaping Around Buildings Affect Waterproofing Performance Over Time?
Your landscape design greatly impacts your building's waterproofing effectiveness. You'll need proper landscape drainage that slopes away from foundations, typically 6 inches of fall within 10 feet. Your plant selection matters too – avoid deep-rooted species near foundation walls, as they can damage waterproofing membranes. You're better off choosing shallow-rooted plants and maintaining a 2-foot clearance between vegetation and walls to prevent moisture accumulation and root intrusion.
Are There Specific Waterproofing Requirements for Buildings in Earthquake-Prone Regions?
You'll need to meet specific seismic design considerations when waterproofing buildings in earthquake zones. It's crucial to use flexible, earthquake resistant materials that can withstand ground movement without cracking or separating. You should install expansion joints and flexible membrane systems that can accommodate structural shifts. Like other building professionals, you'll want to verify your waterproofing details comply with local seismic codes while maintaining watertight integrity during and after seismic events.