To select the right caulking material for your commercial property, you'll need to match specific sealant properties with your application requirements. Silicone sealants offer superior weather resistance for exterior joints, while polyurethane provides excellent adhesion for high-movement areas. For interior work, consider low-VOC acrylic or latex options that prioritize air quality and paintability. Factor in joint movement capabilities—silicone handles ±50% movement, while polyurethane manages ±25%. You'll also want to evaluate environmental impact, building codes, and long-term maintenance costs. Understanding these key factors will guarantee ideal performance and ROI for your specific application needs.
Common Types of Commercial Sealants
Commercial sealants are essential components in building maintenance and construction, available in several formulations designed for specific applications. You'll find silicone sealants offering superior weather resistance and flexibility, making them ideal for exterior joints and windows. Polyurethane sealants provide excellent adhesion and durability, perfect for high-movement areas and concrete applications.
For interior finishing, you've got options like acrylic sealants and latex sealants, which are paintable and easy to work with. Acrylic variants work well for minor gaps and cracks, while latex types offer good flexibility for general-purpose sealing. Hybrid sealants combine the best properties of silicone and polyurethane, delivering enhanced UV resistance and paintability.
When you're working with metal flashings or dealing with water infiltration, butyl sealants are your go-to choice. For specialized applications, you'll need firestop sealants that meet specific fire-rating requirements and acoustic sealants designed to minimize sound transmission between spaces. Each type serves a distinct purpose in your commercial property's maintenance strategy, ensuring proper sealing and protection based on your specific requirements.
Environmental Impact Considerations
Sustainability concerns increasingly influence sealant selection for building projects. As you evaluate caulking materials for your commercial property, you'll need to take into account both their environmental impact and performance capabilities. Modern sustainability practices now emphasize low-VOC (volatile organic compound) formulations that help maintain indoor air quality and reduce harmful emissions during application and curing.
When selecting eco-friendly options, you'll find several alternatives to traditional petroleum-based sealants. Water-based acrylic caulks offer lower environmental impact and easier cleanup, while silicone sealants made from naturally occurring materials provide durability with reduced ecological footprint. You'll also want to take into account products with recycled content and those that support LEED certification requirements.
Pay attention to disposal requirements and lifecycle assessments. Some newer sealants feature biodegradable properties or can be more easily separated from other materials during demolition. You'll benefit from choosing products with minimal packaging waste and those manufactured using renewable energy sources. Additionally, select sealants that require less frequent replacement, as this reduces both maintenance costs and environmental impact over your building's lifetime.
Indoor Vs Outdoor Applications
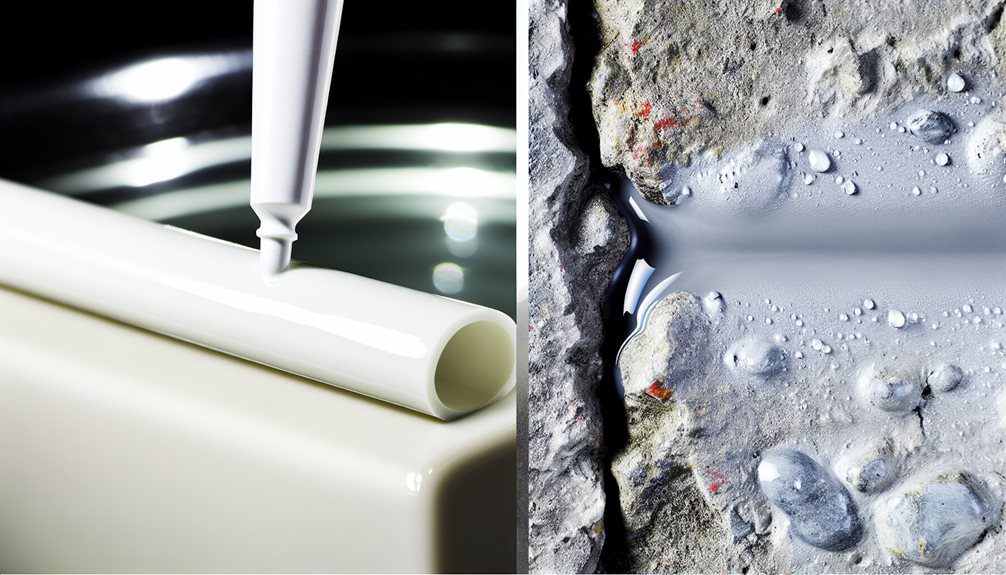
A caulk's intended location greatly impacts your material selection, as indoor and outdoor environments present distinct challenges and requirements. For interior spaces, you'll want to focus on low-VOC products that prioritize air quality and occupant comfort. Silicone and acrylic latex caulks work well for indoor applications, offering excellent adhesion for baseboards, trim work, and around fixtures while maintaining flexibility during subtle building movements.
For exterior environments, you'll need products that can withstand harsh weather conditions, UV exposure, and extreme temperature fluctuations. Choose polyurethane or advanced silicone caulks that offer superior water resistance and durability. These materials maintain their seal integrity despite expansion and contraction cycles common in outdoor settings.
Consider your specific application requirements when selecting between indoor and outdoor caulks. Interior applications typically demand aesthetics and paintability, while exterior uses require maximum weather resistance and joint movement capability. You'll find that some manufacturers offer hybrid products that work in both settings, but it's crucial to verify their performance ratings match your specific needs. Always check the product specifications to ascertain compatibility with your substrate materials and environmental conditions.
Cost Analysis and ROI
Several factors influence the total cost-benefit analysis when selecting commercial caulking materials, including initial product costs, labor requirements, longevity expectations, and maintenance cycles. While premium silicone caulks might cost 30-40% more upfront than basic acrylic options, they'll typically deliver superior cost efficiency through extended service life and reduced maintenance needs.
You'll find that investment returns often correlate directly with material quality. A high-grade polyurethane caulk might last 15-20 years, compared to 5-7 years for standard latex varieties, effectively reducing your long-term maintenance budget. Consider that labor costs typically represent 60-70% of any caulking project, so choosing materials that require less frequent replacement greatly impacts your bottom line.
To maximize ROI, you'll need to evaluate your property's specific requirements. External applications facing harsh weather conditions warrant premium materials, while interior applications might allow for more economical options. Factor in your building's maintenance schedule, environmental conditions, and usage patterns. You can calculate your expected return by comparing the total cost of installation and maintenance over the material's lifespan against potential repair costs and energy savings from improved sealing.
Weather and Temperature Factors

Weather conditions and temperature fluctuations play critical roles in determining the most effective caulking materials for your commercial property. You'll need to take into account your region's specific climate patterns and seasonal variations when selecting the appropriate sealant to guarantee long-term performance and durability.
In areas with significant temperature extremes, you'll want to choose caulking materials with high flexibility ratings that can expand and contract without cracking or separating from surfaces. Silicone-based caulks typically offer the best performance in these conditions, maintaining their elastic properties from -60°F to 400°F, while polyurethane sealants work best between 30°F and 120°F.
Humidity levels also affect your caulking choice. If you're managing property in high-moisture environments, you'll need moisture-cured sealants that resist mildew growth and maintain their adhesive properties. For coastal properties, think about sealants specifically formulated to withstand salt exposure and constant moisture. Remember to check the manufacturer's temperature application guidelines, as most caulking materials require specific temperature ranges during installation to cure properly and achieve maximum bonding strength.
Installation Best Practices
You'll achieve ideal caulking results by following a systematic surface preparation process that includes thorough cleaning, priming when needed, and ensuring surfaces are completely dry. Proper application techniques require consistent pressure on the caulking gun while maintaining a 45-degree angle, with steady movement to create an even bead width. For best results, you should tool the caulk immediately after application, using appropriate smoothing tools and removing masking tape before the material begins to skin over.
Surface Preparation Steps
Prior to applying any caulking material, proper surface preparation stands as the most critical step for guaranteeing long-lasting results. You'll need to begin with a thorough surface cleaning, removing all traces of dirt, oil, old caulk, and loose debris. Use appropriate solvents or cleaners based on your substrate type, and verify the surface is completely dry before proceeding.
Start your substrate evaluation by checking for structural integrity and damage. You'll want to inspect for cracks, spalling, or deterioration that could compromise the caulk's adhesion. If you find any issues, address them before moving forward with the caulking project.
For ideal adhesion, follow these essential steps:
- Remove all existing caulk and sealants completely
- Clean joints with a wire brush to eliminate loose particles
- Apply primer when required by manufacturer specifications
- Install backing material to control sealant depth
- Mask adjacent surfaces with painter's tape
- Confirm surface temperature falls within recommended range
- Verify moisture levels meet manufacturer requirements
Remember to document your surface preparation process for warranty purposes and maintain consistent preparation standards across all application areas.
Application Techniques And Tips
Effective caulk application requires mastering several key installation techniques to confirm excellent performance and longevity. You'll need to maintain a consistent angle of 45 degrees while applying the caulk and move the gun steadily along the joint. This positioning guarantees superior material distribution and adhesion to both surfaces.
When applying caulk, you'll want to control your speed and pressure to achieve a uniform bead size. Professional caulking techniques include pulling the gun toward you rather than pushing it away, which provides better visibility and control. If you're working with wider joints, apply enough material to create slight convex crowning for proper joint movement capabilities.
Your application tools should include a high-quality caulking gun with a smooth pressure release mechanism. You'll find that using a caulk finishing tool or your finger (while wearing disposable gloves) helps create a smooth, professional finish. When tooling the joint, apply consistent pressure and complete the smoothing process in one continuous motion. Remember to remove masking tape immediately after tooling, before the caulk begins to skin over, to achieve clean, sharp edges.
Maintenance and Longevity
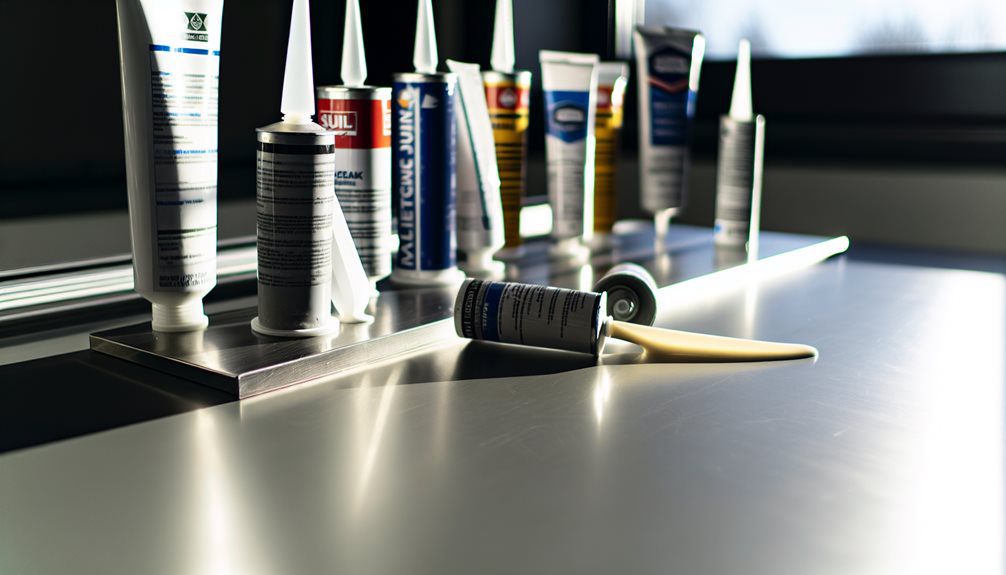
You'll need a systematic approach to maintain your commercial property's caulking, starting with quarterly visual inspections to catch early signs of degradation or separation. Your maintenance team should clean the caulked areas with appropriate solvents and guarantee surrounding surfaces remain free from dirt, mold, and debris that can compromise seal integrity. When you notice gaps, cracks, or hardening, plan your reapplication efforts during moderate weather conditions, guaranteeing complete removal of old material before installing new caulking.
Regular Inspection Schedule
Regular caulking inspections serve as the cornerstone of preventive maintenance for commercial properties, with quarterly visual assessments recommended as a baseline schedule. You'll need to adjust your inspection frequency based on your building's specific conditions, including age, climate exposure, and occupancy type. During each inspection, you should document any signs of deterioration, separation, or discoloration in the caulking materials.
Create a systematic maintenance schedule that includes detailed checklists for each inspection zone. You'll want to pay special attention to high-stress areas such as expansion joints, window perimeters, and areas exposed to extreme temperature fluctuations. It's vital to track changes between inspections, noting any patterns that might indicate underlying issues.
Record keeping is significant – maintain a digital or physical log of all inspections, including photographs and detailed notes about problem areas. You'll find this documentation invaluable when planning repairs or demonstrating due diligence to stakeholders. Consider implementing a mobile inspection app that allows your maintenance team to input data directly on-site, ensuring consistent monitoring and timely response to emerging issues.
Cleaning and Surface Care
Proper surface care protocols form the foundation of long-lasting caulk performance in commercial buildings. You'll need to establish consistent surface cleaning procedures before applying new caulk or maintaining existing installations. Start by removing all traces of old caulk, dirt, and debris using appropriate solvents or mechanical methods specific to your surface material.
Your maintenance routines should include regular inspection of caulked areas for signs of deterioration, focusing on high-stress points where building materials meet. When you're preparing surfaces for new applications, ascertain they're not only clean but also completely dry – moisture trapped beneath caulk will compromise its adhesion and longevity. You'll want to use surface-appropriate primers when recommended by manufacturers.
For ongoing care, avoid harsh cleaning agents that could degrade the caulk's molecular structure. Instead, opt for pH-neutral cleaners and soft brushes when removing accumulated dirt. You'll find that establishing a documented cleaning protocol helps maintain consistency across your maintenance team's efforts. Remember to keep detailed records of cleaning activities, including dates, methods used, and any observed changes in caulk condition.
Reapplication Best Practices
In accordance with industry standards, successful caulk reapplication depends on timing and technique. You'll need to monitor your commercial property's caulking conditions and establish a reapplication frequency that aligns with the manufacturer's recommendations, typically every 5-7 years for exterior applications and 7-10 years for interior work.
Before proceeding with reapplication, you must completely remove the old caulking and verify surface conditions are ideal. Your surfaces should be clean, dry, and free from any loose material. When temperatures fall between 40-80°F (4-27°C), you'll achieve the best adhesion results. You'll want to avoid applying new caulk during periods of extreme humidity or when precipitation is expected within 24 hours.
Your reapplication technique should include proper tooling to guarantee the new caulk makes full contact with joint surfaces. You'll need to maintain consistent pressure when applying the bead, and you should tool immediately after application. Remember to verify joint width-to-depth ratios meet specifications – typically 2:1 for most commercial applications. These practices will help maximize your caulking's service life and maintain your building's integrity.
Building Code Requirements
Building codes consistently mandate specific requirements for commercial caulking applications to confirm occupant safety and building integrity. You'll need to ascertain your caulking materials meet local compliance standards, particularly for fire-rated assemblies and weatherization requirements. Most jurisdictions follow the International Building Code (IBC) guidelines, which specify minimum performance criteria for different applications.
When selecting caulking materials, you'll want to verify they meet ASTM standards and have appropriate fire ratings for your specific use case. Fire-rated caulks must achieve specific ratings (typically 1-4 hours) when tested according to ASTM E814 or UL 1479. For exterior applications, you're required to use materials that meet ASTM C920 weatherization standards.
Remember to document your compliance by maintaining product data sheets and installation records. You'll find that many municipalities require inspection of caulking installations, especially in fire-rated assemblies and expansion joints. To avoid costly corrections, consult your local building department before starting major caulking projects, as requirements can vary markedly by location and building type. If you're working on historic properties, you may face additional preservation requirements that affect your caulking material choices.
Joint Movement Capabilities
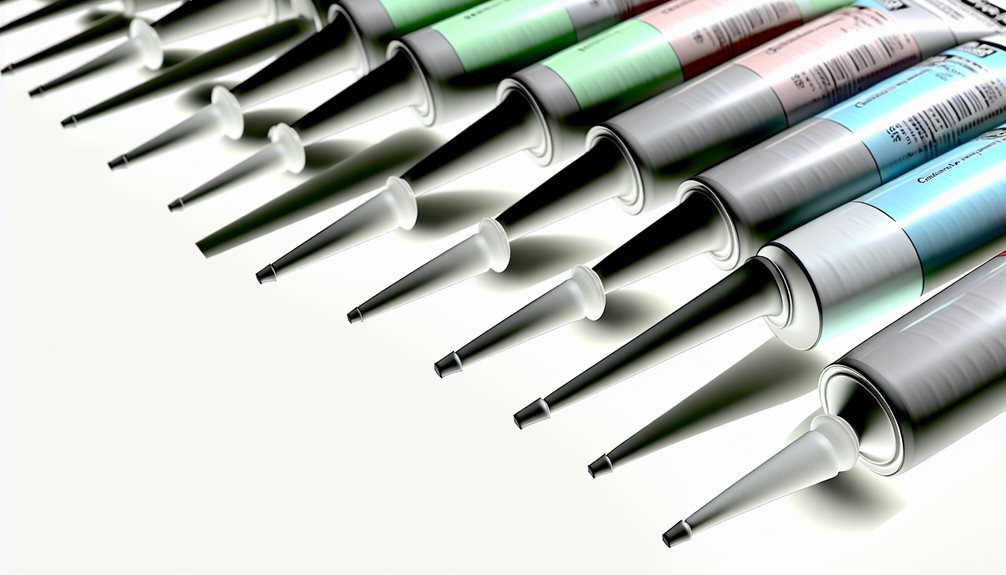
Understanding joint movement capabilities remains essential when selecting commercial caulking materials, as different sealants accommodate varying degrees of expansion, contraction, and shear forces. You'll need to conduct a joint flexibility assessment to determine the expected movement range your building's joints will experience throughout seasonal changes and structural shifts.
When you're evaluating movement accommodation techniques, consider that high-performance silicone sealants typically offer ±50% movement capability, while polyurethane sealants provide ±25%. You'll find that acrylic latex caulks only accommodate ±7.5% movement, making them suitable solely for minimal-movement applications. To guarantee proper performance, you should multiply your expected joint movement by a safety factor of 1.5 when selecting your sealant's movement rating.
During your selection process, factor in the joint's width-to-depth ratio, as it directly affects the sealant's ability to handle movement. For maximum performance, maintain a 2:1 width-to-depth ratio for joints experiencing significant movement. Remember that improper movement accommodation can lead to adhesion failure, cohesive splitting, or compression set, compromising your building's weatherproofing system.
Material Performance Testing
Testing caulking materials for your commercial project requires evaluation of key parameters including adhesion strength, UV resistance, and temperature cycling performance. You'll need to conduct accelerated weathering tests using standardized ASTM methods to assess long-term durability and material degradation patterns. ASTM C719 and C1519 test protocols will help you verify the caulking material's performance through stretch-compression cycles and environmental exposure conditions that simulate real-world applications.
Key Testing Parameters
Material performance testing relies on several standardized parameters that determine a caulking product's suitability for commercial applications. When you're evaluating material testing methods, you'll need to focus on key performance indicators that directly impact your building's integrity and maintenance requirements.
You'll want to assess elongation capacity, which measures how far the caulk can stretch without failing. Test the adhesion strength by examining the caulk's ability to bond with various substrate materials common in your facility. Movement capability testing will show you how well the product handles joint expansion and contraction, while weathering resistance reveals its durability against UV exposure and moisture.
Don't overlook the importance of cure time and temperature stability testing. You'll need to verify that the caulk maintains its properties across your region's temperature range. Shore hardness measurements will tell you about the cured material's firmness, while tensile strength testing demonstrates its resistance to tearing. These parameters work together to confirm you're selecting a product that meets your building's specific demands and complies with industry standards.
Durability Assessment Methods
Building on those key testing parameters, specific durability assessment protocols help you determine long-term material performance. You'll want to conduct thorough durability testing through accelerated aging processes, which simulate environmental stressors your caulking will face over time. These tests typically involve UV exposure chambers, thermal cycling units, and moisture resistance evaluations.
To guarantee accurate longevity evaluation, you should implement both static and dynamic testing methods. Static tests measure the caulking's ability to maintain adhesion and flexibility while remaining stationary, while dynamic tests assess performance during repeated joint movement cycles. You'll need to monitor key indicators such as adhesion retention, elasticity maintenance, and resistance to environmental degradation.
Your testing protocol should include exposure to site-specific conditions that your commercial property experiences. This means subjecting samples to your local temperature extremes, typical UV intensity, and expected chemical exposures. Document changes in material properties, including hardness, elongation capacity, and recovery rates. By analyzing these results against industry benchmarks, you can make informed decisions about which caulking materials will provide the best performance for your specific application.
Frequently Asked Questions
Can Caulking Be Painted Over Immediately After Application?
You'll need to wait before painting over fresh caulk for best results. Most silicone and latex caulks require 24-48 hours of curing time, depending on humidity and temperature. For paint compatibility, choose paintable caulks specifically labeled for this purpose. You can speed up application timing by using fast-drying acrylic latex caulks, which may be paintable in 2-4 hours. Always check your product's specific instructions for recommended dry times.
How Long Should Caulk Cure Before Exposing It to Water?
You'll need to allow proper cure time before exposing your caulk to water. Most silicone and latex caulks require 24-48 hours to fully cure, but you should check your product's specific instructions. If you're working in high-humidity areas, you might need to extend this time. For the best results, wait at least 24 hours before any light water exposure and a full 72 hours before subjecting the seal to prolonged water contact.
Are There Caulking Materials Specifically Designed for Fire-Rated Assemblies?
Yes, you'll find specialized firestop caulking products designed specifically for fire-rated assemblies. These materials are engineered to maintain the fire resistance rating of walls, floors, and joints by expanding when exposed to heat, creating an effective barrier against flame and smoke. When you're working with fire-rated construction, you'll need to use UL-listed firestop caulking that matches your assembly's requirements and follows local building codes.
What Safety Equipment Is Required When Removing Old Caulking Materials?
You'll need to wear safety goggles to protect your eyes from debris and chemical exposure while removing old caulking. Always use protective gloves that are chemical-resistant to prevent skin contact with potentially harmful substances. It's also smart to wear a dust mask or respirator, especially when working with older materials that might contain hazardous components. Work in a well-ventilated area and keep a vacuum handy to collect loose particles as you work.
How Do Different Colored Caulks Affect the Final Appearance After Aging?
You'll find that color stability varies considerably among different caulk types. Premium silicone and acrylic caulks maintain their original color longer, while lower-quality options show noticeable fading effects within months of exposure to UV rays. Dark-colored caulks typically show more dramatic aging, often becoming chalky or discolored. To maintain your project's aesthetic appeal, you'll want to choose UV-resistant formulations and lighter colors that'll mask any inevitable aging or discoloration.