To maintain load-bearing brick walls in commercial buildings, you'll need a systematic approach focused on regular inspections and preventive maintenance. Schedule bi-annual inspections during spring and fall, increasing to quarterly checks for structures over 50 years old. Monitor for vertical fissures exceeding 1/8 inch, stair-step cracks wider than 1/4 inch, and moisture content below 16%. Implement waterproofing measures costing $2-$4 per square foot and maintain relative humidity between 35-45% in adjacent spaces. Professional structural assessments every 36 months using non-destructive testing methods will help you identify potential issues before they compromise your wall's 1,500-2,000 pounds per linear foot load capacity. Exploring thorough maintenance strategies can reduce your long-term repair expenses by up to 40%.
Load-Bearing Wall Construction Fundamentals
Through careful engineering and proper construction techniques, load-bearing brick walls serve as critical structural elements that transfer weight from the roof and upper floors to the foundation. You'll find that these walls require precise calculations to determine their load capacity, which typically ranges from 1,500 to 2,000 pounds per linear foot, depending on the brick wall types and construction methods used.
When you're working with load-bearing walls, you'll need to understand that they're constructed using specific brick patterns, or bonds, that maximize structural integrity. The most common brick wall types for load-bearing applications include solid masonry walls and cavity walls. You'll see that solid walls are typically 8 to 12 inches thick, while cavity walls incorporate an air space between two separate wythes of brick.
To guarantee proper load distribution, you'll want to verify that your foundation is designed to handle 1.5 times the anticipated load. The mortar joints, typically 3/8 inch thick, must be fully filled and properly cured to achieve maximum compressive strength. You'll also need to include appropriate steel reinforcement and lateral support systems to meet building code requirements for your specific application. Regular maintenance, including masonry restoration, can help prevent issues that may compromise the integrity of these vital structures.
Common Signs of Structural Damage
In accordance with structural engineering standards, identifying early warning signs of brick wall deterioration can prevent catastrophic failures. You'll need to monitor your load-bearing walls regularly, focusing on specific indicators that suggest potential structural compromise.
During your crack detection process, you'll want to document any vertical fissures exceeding 1/8 inch in width, as these often indicate foundation settlement issues. Stair-step cracks along mortar joints, particularly those wider than 1/4 inch, require immediate professional evaluation. You should also watch for horizontal cracks, which may signal serious structural instability from lateral pressure.
Your moisture assessment should include checking for efflorescence (white mineral deposits), which suggests water infiltration within the wall system. Look for damp patches exceeding 12 inches in diameter, especially after rainfall. You'll need to measure any brick displacement beyond 1/4 inch from the vertical plane using a plumb bob, as this could indicate serious structural movement. When you notice mortar deterioration extending deeper than 1/4 inch, it's time to consult a structural engineer, as this compromises the wall's load-bearing capacity. Additionally, consider scheduling regular masonry restoration to address any emerging issues promptly.
Preventive Maintenance Best Practices
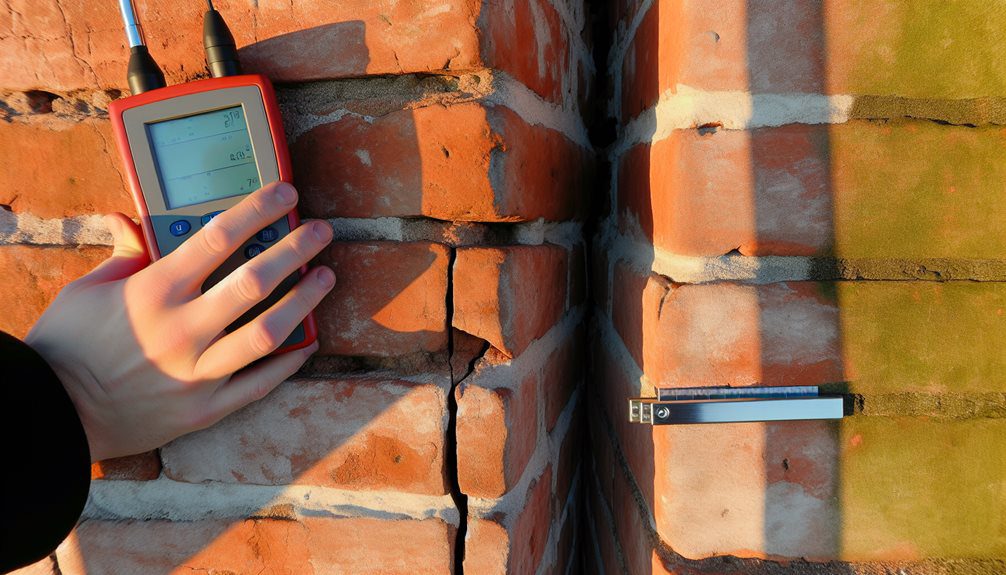
Regular preventive maintenance protocols can help you avoid the costly structural repairs identified in the previous section. Your maintenance schedules should incorporate quarterly visual inspections of mortar joints, brick surfaces, and structural alignment, with thorough evaluations conducted annually by qualified structural engineers.
Implement preventive strategies by monitoring moisture levels using calibrated meters, maintaining readings between 12-15%. You'll need to address water infiltration immediately by repointing deteriorated mortar joints and applying water-resistant sealants rated for commercial masonry. Schedule tuckpointing every 25-30 years, depending on environmental exposure, and guarantee proper drainage with functional gutters positioned at 1-foot intervals per 100 square feet of wall surface.
Document all inspections using standardized checklists that track changes in crack widths (measured to 0.1mm accuracy), brick displacement, and joint deterioration. Your maintenance team should calibrate monitoring equipment bi-annually and maintain detailed records of all remedial actions. When you integrate these systematic approaches into your building's maintenance program, you'll greatly extend your wall's structural lifespan while protecting your investment. Additionally, consider incorporating waterproofing techniques to further enhance your building's resilience against moisture damage.
Inspection Schedules and Protocols
Professional inspectors establish thorough schedules that specify critical evaluation points throughout the year. You'll need to implement biannual inspections during spring and fall, when temperature variations most notably affect brick structures. Your inspection frequency should increase to quarterly checks if your building is over 50 years old or located in severe weather zones.
Your documentation standards must include detailed photographic evidence, precise measurements of crack widths (using crack width gauges), and moisture readings at predefined control points. You'll want to maintain digital records that track changes over time, with particular attention to:
- Mortar joint deterioration (measured in millimeters)
- Brick displacement (documented to 0.1mm accuracy)
- Water penetration depth (using moisture meters)
- Thermal expansion joint conditions
- Load distribution patterns
Establish clear protocols for each inspection point, including specific equipment requirements and calibration standards. You should conduct load-bearing capacity tests every 36 months using non-destructive testing methods, such as ultrasonic pulse velocity testing. Remember to integrate your findings into your building's maintenance management system for trend analysis and predictive maintenance planning. Incorporating waterproofing techniques is essential to protect brick walls from moisture intrusion, ensuring their long-term integrity.
Weather Impact on Brick Walls
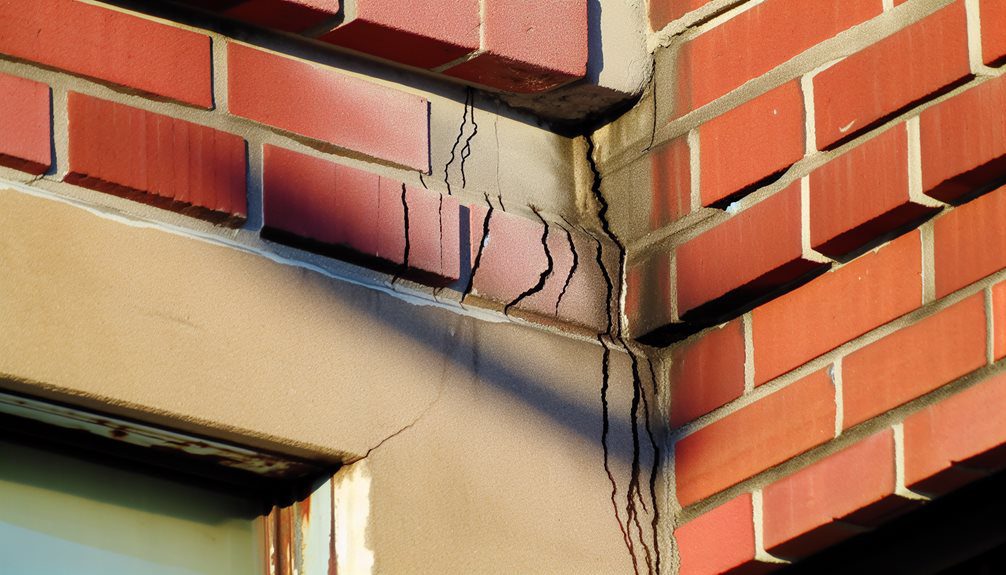
Severe weather conditions can impact load-bearing brick walls through multiple degradation mechanisms. You'll need to understand how temperature fluctuations cause thermal expansion and contraction cycles, which can create stress points at mortar joints. During freeze-thaw cycles, moisture trapped within bricks can expand by up to 9%, potentially causing spalling and internal structural damage.
Your brick wall's weather resistance depends largely on proper drainage and ventilation systems. You'll find that wind-driven rain can penetrate up to 6 inches into poorly maintained masonry, leading to efflorescence and deteriorating mortar joints. In coastal environments, salt crystallization can accelerate brick deterioration by 40% compared to inland locations.
Monitor your wall's thermal performance, as extreme temperature variations of 60°F or more within 24 hours can cause differential movement between exterior and interior wythes. You should pay special attention to corner sections and areas around openings, where thermal stress concentrates. Installing proper expansion joints every 20-25 feet can help accommodate these movements and prevent cracking. Regular assessment of your wall's weather resistance features will help maintain structural integrity and prevent costly repairs. Additionally, engaging in regular masonry maintenance can significantly extend the lifespan of your brick walls.
Professional Repair Methods
Expert repair methods for load-bearing brick walls break down into three primary intervention categories: mortar joint restoration, brick replacement, and structural reinforcement. When you're addressing mortar deterioration, you'll need to implement tuckpointing, which involves removing damaged mortar to a depth of at least 3/4 inch and replacing it with new mortar that matches the original composition.
For brick wall restoration, you'll often encounter scenarios requiring individual brick replacement. You'll need to carefully remove damaged units without compromising surrounding bricks, then install new ones that match both the dimensional and compressive strength specifications of the original masonry. The replacement process must maintain proper spacing and alignment to guarantee structural integrity.
Structural reinforcement masonry repair techniques include the installation of helical ties at 16-inch intervals and the application of carbon fiber mesh in high-stress areas. You'll want to integrate steel plates or angles when addressing major structural issues, especially at corners and openings where load concentration is highest. Remember to regularly monitor these interventions through quantitative assessment methods, including deflection measurements and crack monitoring gauges. Additionally, it's important to consult with professionals experienced in masonry restoration to ensure the best practices are followed throughout the repair process.
Cost-Effective Maintenance Strategies
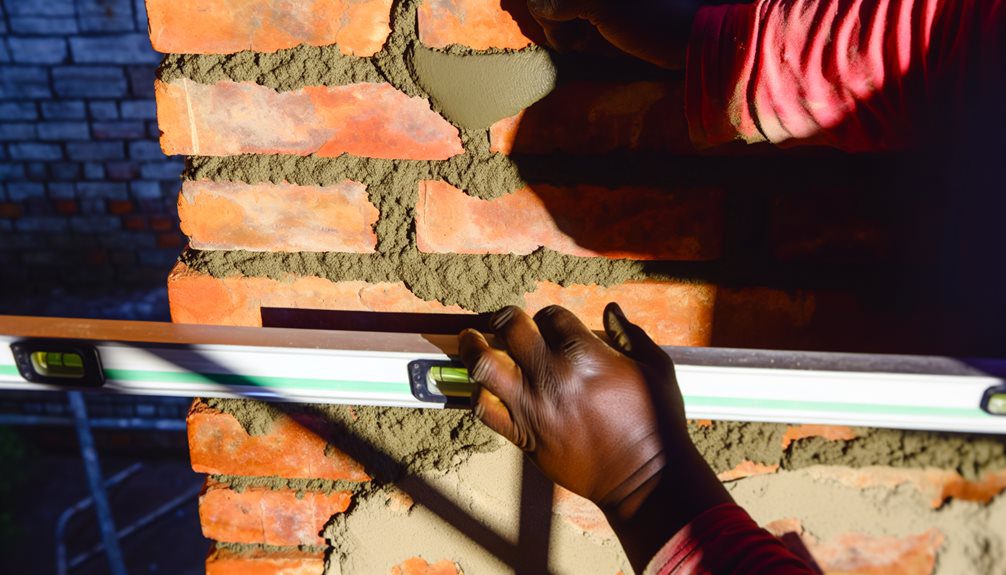
While professional repairs can be costly, implementing preventive maintenance strategies can reduce your long-term repair expenses by up to 40%. You'll find that scheduling bi-annual inspections and addressing minor issues promptly helps prevent major structural problems from developing.
To implement cost-effective repairs, start by establishing a maintenance calendar that includes monthly visual inspections of mortar joints, brick surfaces, and water drainage systems. You'll want to clean your gutters quarterly and make sure downspouts direct water at least 3 feet away from the wall's foundation. When you spot deteriorating mortar, apply budget-friendly upgrades like spot repointing before moisture can penetrate deeper.
Document all maintenance activities and create a spreadsheet to track expenses, helping you identify patterns and optimize your maintenance budget. Consider investing in moisture meters ($100-$300) and thermal imaging cameras ($500-$2,000) to detect potential issues before they become visible. These tools, while initially expensive, typically pay for themselves within two years through early problem detection. Install moisture barriers during any repair work, as this $2-$4 per square foot investment can prevent thousands in future water damage repairs. Additionally, partnering with a professional masonry restoration company can provide expert guidance and support for maintaining the integrity of load-bearing walls.
Structural Assessment Techniques
Begin your structural assessment of load-bearing brick walls by conducting systematic visual inspections that target critical failure points, including mortar joints, wall intersections, and load transfer zones. You'll need to document and measure visible cracks exceeding 3mm, with particular attention to patterns that indicate structural movement or settlement. To quantify wall stability, implement standardized load testing protocols that measure deflection rates under controlled pressure applications of 1.5x the designed load capacity. Additionally, consider incorporating tuckpointing techniques to restore mortar joints, which can significantly enhance the durability of the wall structure.
Visual Inspection Methods
Regular visual inspections form the cornerstone of structural assessment for load-bearing brick walls. You'll need to conduct these inspections quarterly, utilizing essential visual inspection tools like crack monitors, measuring tapes, and high-resolution cameras to document any changes in the wall's condition. Start by establishing a systematic inspection checklist that covers critical areas from foundation to roofline.
When you're examining the walls, you'll want to focus on specific indicators of structural issues. Look for vertical or diagonal cracks exceeding 3mm in width, bulging sections that deviate more than 25mm from plumb, and deteriorating mortar joints deeper than 6mm. Document spalling brick faces, efflorescence patterns, and any displacement at wall intersections or corners.
Your inspection should include examining the wall's exposure to moisture, noting any compromised flashings, damaged copings, or deteriorated sealants. Check for signs of foundation settlement, indicated by stepped cracking patterns or separation at building corners. Record your findings systematically, including measurements and photographs, to establish a baseline for monitoring changes over time and identifying developing structural concerns. Additionally, consider integrating professional tuckpointing services as needed to maintain the integrity of mortar joints and overall wall strength.
Load Testing Protocols
Professional load testing protocols serve as critical assessment tools for evaluating a brick wall's structural integrity. You'll need to follow standardized procedures that incorporate both non-destructive and semi-destructive testing methods to obtain accurate load capacity evaluation data. When you're conducting these tests, it's crucial to measure both vertical and lateral loads using calibrated hydraulic jacks and pressure sensors.
Your stress distribution analysis should include measuring deflection at multiple points along the wall's surface. You'll want to utilize digital strain gauges placed at 1-meter intervals, recording data at predetermined load increments of 0.5 kN/m². As you're monitoring the wall's response, pay particular attention to any deviation from linear elastic behavior, which typically indicates the onset of structural concerns.
Document all test results using real-time data logging systems, ensuring you've captured both loading and unloading cycles. You'll need to compare these measurements against established baseline values for similar brick wall systems. When you interpret the results, factor in environmental conditions such as temperature and humidity, as these variables can greatly impact load-bearing capacity measurements. Additionally, consider consulting with professionals in commercial tuckpointing to ensure any necessary repairs are performed accurately and efficiently.
Waterproofing and Moisture Control
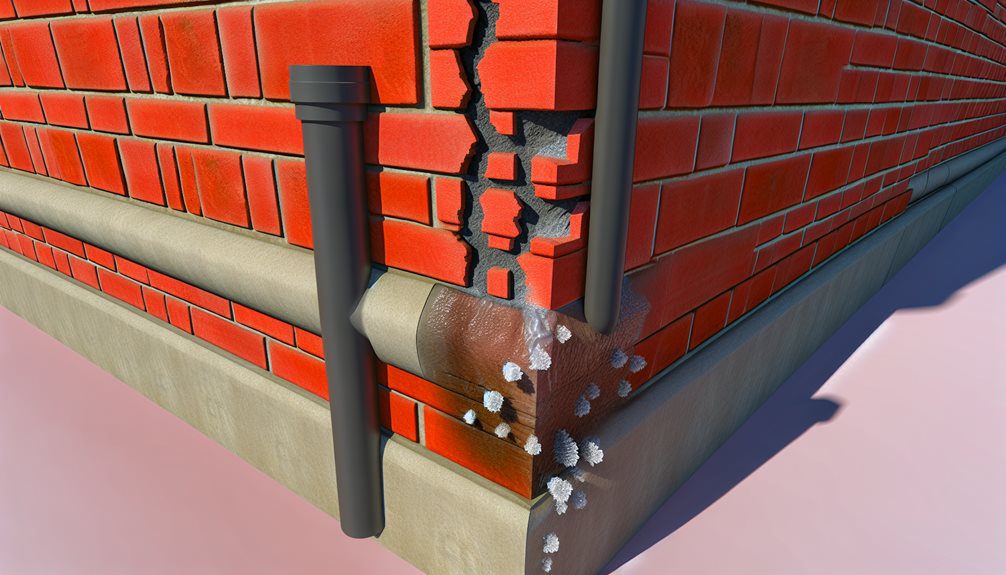
Proper waterproofing and moisture control represent critical factors in preserving load-bearing brick walls' structural integrity. You'll need to implement thorough moisture barriers that protect against both surface water and rising damp, which can compromise your wall's load-bearing capacity by up to 40% when left unchecked.
Install drainage systems at critical points where water accumulation typically occurs, particularly at the wall's base and around window openings. You'll want to confirm your through-wall flashing extends at least 0.5 inches beyond the wall face, creating an effective drip edge. When you're retrofitting existing walls, consider installing weep holes at 24-inch intervals to facilitate proper moisture evacuation.
You'll need to maintain relative humidity levels between 35-45% in adjacent interior spaces to prevent moisture migration through the brick. It is crucial to monitor your wall's moisture content regularly using calibrated moisture meters, keeping readings below 16% to prevent structural degradation. Remember that every 1% increase in moisture content above this threshold can reduce your wall's compressive strength by approximately 5%. Consider applying penetrating sealers that maintain 85% breathability while providing hydrophobic protection.
Retrofitting Historical Brick Structures
Retrofitting historical brick structures demands three key engineering considerations: structural reinforcement, material compatibility, and load distribution analysis. When you're undertaking structural reinforcement, you'll need to assess the existing brick's compressive strength, which typically ranges from 1,500 to 20,000 psi in historical buildings. Installing steel reinforcement plates or carbon fiber strips can enhance load-bearing capacity by 40-60%.
Material compatibility is essential for historical preservation. You'll want to match the original mortar's composition, guaranteeing your retrofit materials don't create adverse chemical reactions or differential thermal expansion. Modern mortars should maintain a compressive strength within 10% of the historical mortar to prevent stress concentrations.
For load distribution analysis, you'll need to calculate current dead loads and anticipated live loads. Install load cells at critical points to monitor pressure distribution, and verify your retrofitting solutions don't exceed 75% of the wall's rated capacity. Use non-destructive testing methods like ground-penetrating radar to identify hidden structural weaknesses before implementing reinforcement strategies. This approach maintains structural integrity while preserving the building's historical character for future generations.
Frequently Asked Questions
How Does Brick Color Variation Affect the Structural Integrity of Load-Bearing Walls?
Brick color variations don't directly impact your wall's structural integrity. While brick aesthetics may vary due to firing temperatures (ranging from 1,800°F to 2,400°F), these color differences primarily affect thermal properties rather than strength. You'll find that properly manufactured bricks, regardless of their hue, maintain consistent compressive strengths (2,500-15,000 psi). What matters most for your structure's stability is the manufacturing quality and installation technique, not the color.
Can Electromagnetic Fields From Nearby Power Lines Weaken Mortar Bonds Over Time?
You don't need to worry about electromagnetic exposure from power lines affecting your mortar bonds. There's no scientific evidence showing that electromagnetic fields cause mortar deterioration or weaken masonry structures. While mortar can degrade from various environmental factors like moisture, temperature cycles, and chemical exposure, electromagnetic fields aren't a contributing factor. Your focus should remain on traditional maintenance concerns that we've proven affect structural integrity.
What Role Do Neighboring Building Vibrations Play in Brick Wall Stability?
You'll need to monitor neighboring building vibrations carefully, as they can considerably impact your wall's stability. When external vibration frequencies match your wall's structural resonance, you're facing potential amplification of movement forces. Think of it like pushing a swing – even small but consistent vibrations at the right frequency can build up destructive energy. You'll want to measure these frequencies regularly and consider installing vibration dampeners if they exceed acceptable thresholds.
How Do Underground Transportation Systems Impact Load-Bearing Brick Wall Foundations?
You'll find that underground transit systems create cyclical vibrations that can trigger soil erosion and progressive foundation settlement beneath your building's load-bearing walls. When trains pass within 50-100 feet, they generate frequencies between 5-15 Hz that compress surrounding soil particles. Over time, you'll notice this compression can lead to differential settlement rates of 0.5-2mm annually, potentially compromising your wall's structural stability if you don't implement proper monitoring and reinforcement measures.
Are Specific Brick Patterns More Resistant to Seismic Activity Than Others?
You'll find that certain brick patterns offer superior seismic resistance through enhanced bond strength and load distribution. The English bond pattern, with alternating courses of headers and stretchers, provides up to 15% more lateral stability than running bond. For maximum seismic protection, you'll want to take into account stack bond with continuous vertical joints reinforced by steel ties, which can increase your wall's shear resistance by 20-30% during seismic events.