Proper caulking can dramatically reduce your office building's energy waste, which typically accounts for 25-40% of total energy costs. You'll find the most significant air leaks around window frames, door seals, electrical outlets, and plumbing penetrations. By applying appropriate sealants – silicone for metal and glass, polyurethane for exterior joints, and acrylic latex for wall-floor gaps – you can achieve energy savings of 5-20% annually. For a 10,000-square-foot office space, this translates to potential yearly savings of $2,000-$8,000. Understanding the specific materials and application techniques will maximize your energy efficiency investment's effectiveness.
Understanding Air Leakage Basics
Air leakage frequently accounts for 25-40% of energy waste in commercial buildings, making it a critical factor in office energy efficiency. You'll find that air movement through your office space follows basic physics principles, with air pressure differentials driving the flow from high to low-pressure areas. Understanding these dynamics helps you identify and address potential leak points in your workspace.
When examining your office environment, you'll need to evaluate both obvious and hidden air pathways. Air typically escapes through window frames, electrical outlets, door frames, and areas where different building materials meet. Thermal bridging, which occurs when building materials create a direct pathway for heat transfer, often accompanies these air leakage points and compounds energy loss.
You can detect air leakage patterns by monitoring temperature variations across your office space and observing common indicators like drafts, inconsistent heating or cooling, and unusual dust accumulation. By working with your facility team to conduct regular building envelope assessments, you'll identify these issues before they greatly impact your energy costs. Understanding these fundamentals allows you to implement targeted solutions that enhance your office's energy performance.
Common Office Building Leak Points
When examining typical office buildings, you'll encounter several predictable leak points that consistently contribute to energy loss. Your window frames often develop gaps where the frame meets the wall, especially in older buildings where settling has occurred and original caulking has degraded. Door seals, particularly in high-traffic entryways, wear down rapidly and create drafts that affect your building's temperature control systems.
You'll find that roof joints frequently develop leaks where different materials meet, such as around chimneys, vents, and HVAC equipment. These junction points require regular inspection and maintenance to maintain their integrity. Plumbing penetrations through walls and floors create vulnerable areas where conditioned air can escape, while electrical outlets on exterior walls often lack proper insulation and weather-stripping.
To identify these common leak points in your office space, you'll want to conduct a thorough assessment during different weather conditions. Many of your colleagues might notice drafts near these areas, which can serve as valuable indicators of where to focus your air sealing efforts. Understanding these typical leak locations helps you develop a targeted approach to improving your building's energy efficiency.
Caulking Materials and Applications
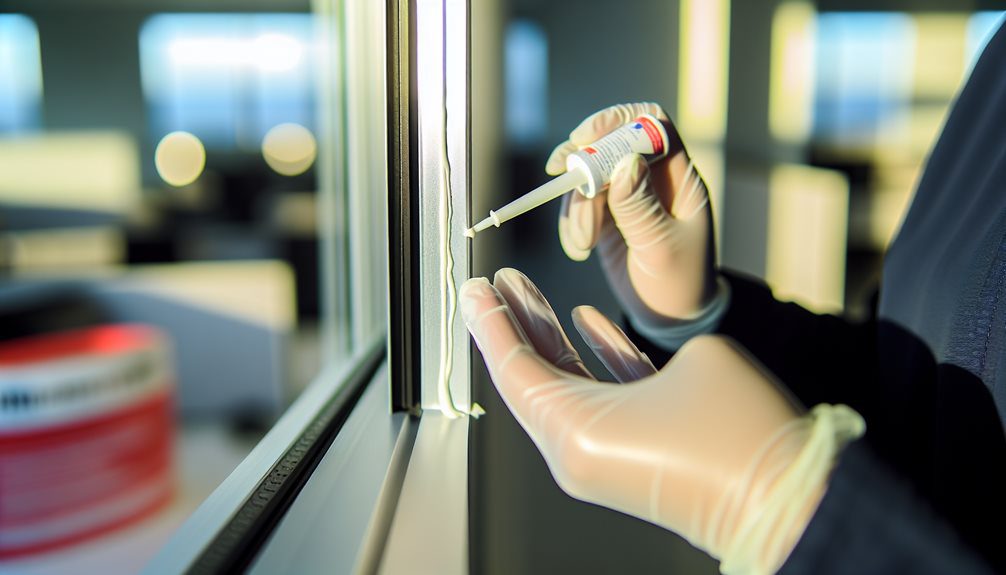
Successful air sealing depends heavily on selecting the right caulking materials for specific applications in your office environment. You'll find that silicone caulking works best for metal, glass, and tile surfaces, offering superior flexibility and water resistance. For exterior joints and areas with significant movement, polyurethane sealants provide excellent durability and adhesion to concrete, wood, and masonry surfaces.
When you're sealing around window frames, you'll want to use a clear silicone caulk that won't yellow over time. For gaps between walls and floors, opt for a paintable acrylic latex caulk that can expand and contract with temperature changes. You'll need to verify proper surface preparation by cleaning the area and removing old caulking residue before application.
Apply your selected caulk in a continuous bead, maintaining consistent pressure on the gun. You can improve the appearance and effectiveness by tooling the caulk immediately after application using a wet finger or specialized tooling device. Remember to work in temperatures above 40°F (4°C) for best curing and adhesion of most caulking products.
Energy Cost Savings Analysis
Calculating potential energy savings begins with a thorough audit of your office's current energy consumption patterns. You'll need to gather at least 12 months of utility bills and analyze seasonal fluctuations in heating and cooling costs. Track your energy consumption before and after implementing caulking improvements to quantify the impact.
Once you've documented baseline data, you can project cost reductions using industry-standard calculators. You'll typically find that proper caulking reduces energy loss by 5-20% annually, depending on your building's age and condition. For a 10,000-square-foot office space, this could translate to $2,000-8,000 in yearly savings.
To maximize your return on investment, focus on high-impact areas first. Air leaks around windows and doors can account for 30% of heating and cooling losses. You'll see the most dramatic cost reduction by addressing these areas initially. Document your findings in a spreadsheet that tracks monthly energy consumption, temperature variations, and cost savings. This data will help you demonstrate the effectiveness of your caulking program to stakeholders and justify future energy efficiency investments.
Professional Installation Best Practices
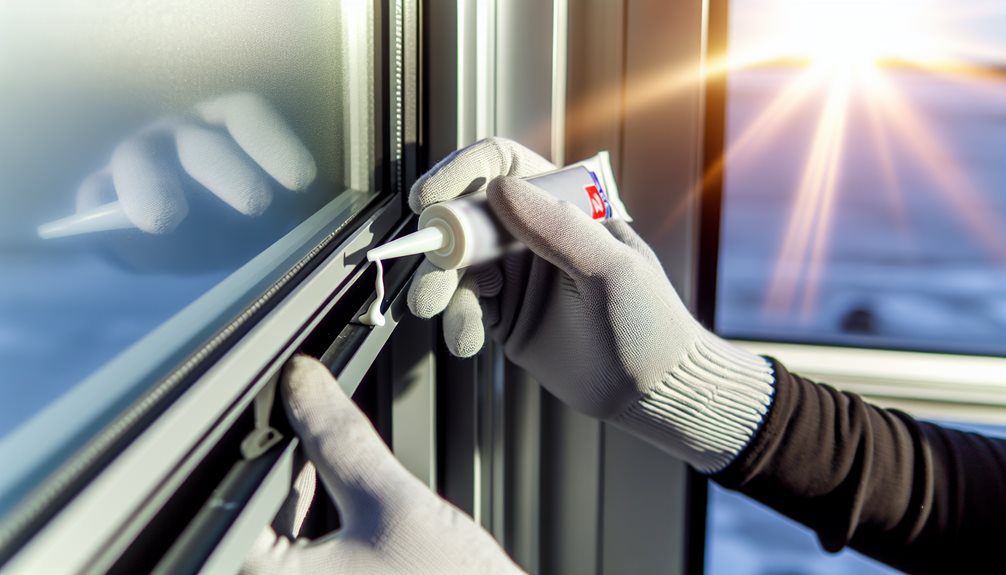
Before initiating any caulking project, proper surface preparation stands as the cornerstone of professional installation. You'll need to thoroughly clean and dry all surfaces, removing any old caulk, dirt, or debris using appropriate solvents and scrapers. Professional techniques require maintaining a consistent workspace temperature between 40-80°F (4-27°C) for ideal adhesion.
When you're ready to apply, cut the caulk tube nozzle at a 45-degree angle, matching the gap width you're sealing. One of the most vital installation tips is maintaining steady pressure while pulling the caulking gun toward you at a consistent speed. You'll want to apply the bead in one continuous motion, avoiding starts and stops that can create weak points.
For professional-grade results, you should tool the caulk immediately after application using a specialized smoothing tool or your gloved finger. Don't forget to protect adjacent surfaces with painter's tape for clean lines. You'll need to allow the caulk to cure completely according to the manufacturer's specifications, typically 24-72 hours, before exposing the area to moisture or stress.
Frequently Asked Questions
How Long Does Commercial-Grade Caulking Typically Last Before Requiring Replacement?
You'll find that commercial-grade caulking lifespan typically ranges from 5-10 years, depending on several factors. Your caulking's durability depends on exposure to UV rays, temperature fluctuations, and movement between building materials. The replacement frequency can be extended if you've chosen high-quality silicone or polyurethane products and they're properly installed. You'll want to inspect your caulking annually for signs of cracking, shrinkage, or separation to determine if it's time for replacement.
Can Caulking Be Applied During Winter Months in Cold-Climate Regions?
You can apply caulk during winter months, but you'll need to follow specific winter caulking techniques. Keep your workspace temperature above 40°F (4°C), and store caulking materials indoors before use. For cold weather considerations, use specialized silicone-based products rated for low temperatures. You'll want to make sure surfaces are completely dry and clean before application. Many pros recommend using a heat gun to warm the application area for best adhesion.
What Are the Signs That Existing Caulking Needs to Be Removed?
You'll know it's time to remove existing caulking when you notice these deterioration signs: cracking, peeling, or gaps forming along the sealed areas. Watch for discoloration or a chalky appearance, which indicates aging material. If you spot moisture intrusion indicators like water stains, mold growth, or dampness around windows and joints, your caulking has failed. You'll also want to check if the material feels brittle or has lost its elasticity when gently pressed.
Are There Specific Caulking Products Designed for Historical Office Buildings?
Yes, you'll find specialized caulking products designed specifically for historical preservation projects. Look for silicone-based or acrylic-latex compounds that won't damage original materials while meeting energy retrofitting standards. Products like Pecora's Historic Sealant Line or DOWSIL's Heritage Restoration Series are formulated to match period-appropriate textures and colors. They'll provide superior adhesion to traditional materials like limestone, terra cotta, and old-growth wood while maintaining the building's historical integrity and improving energy performance.
How Does Humidity Affect Caulking Performance in Open-Plan Office Environments?
You'll notice that humidity levels considerably impact your caulking adhesion in open-plan offices. When humidity's too high, you're likely to see reduced bonding strength and potential mold growth around caulked areas. Too low, and you'll experience premature cracking and shrinkage. To maintain ideal performance, you should aim for relative humidity between 30-50%. Consider installing humidity monitors near critical seal points to track conditions and adjust your HVAC accordingly.