You'll find modern commercial brick repair has evolved considerably through advanced polymer-modified systems and digital monitoring technologies. These solutions combine elastomeric polymers for superior adhesion with real-time structural analysis to guarantee lasting results. You can implement weather-resistant coatings and flexible joint solutions that accommodate building movement while protecting against environmental damage. Digital sensors now track stress points and moisture levels, enabling predictive maintenance before issues escalate. When you pair these innovations with sustainable practices and aesthetic considerations, you'll transform your building's durability and appearance. The depth of these solutions extends far beyond traditional repair methods.
Advanced Polymer-Modified Repair Systems
Three major advancements in polymer-modified repair systems have revolutionized commercial brick restoration. You'll find that elastomeric polymers now provide superior adhesion, advanced acrylic modifiers enhance durability, and hybrid polymer blends offer unprecedented weather resistance. These innovations have transformed how you'll approach deteriorating masonry.
When you're implementing these repair techniques, you'll notice that polymer applications create molecular bonds that far exceed traditional mortar strength. You can achieve up to 400% greater flexural strength using polymer-modified compounds compared to conventional repair methods. The system's microporous structure allows your masonry to breathe while maintaining waterproof characteristics.
You'll want to focus on proper surface preparation before applying these advanced systems. Start by removing deteriorated material and cleaning the substrate thoroughly. Your polymer-modified repair will then bond seamlessly with existing masonry, creating a unified structural element. The latest formulations incorporate self-curing properties, reducing your installation time by up to 60%. These systems also feature color-matching technology, ensuring your repairs blend naturally with surrounding brickwork. When you're working with high-rise commercial structures, you'll appreciate the enhanced workability and extended pot life these advanced polymers provide. Additionally, the use of weatherproofing techniques is essential in ensuring the longevity of your repairs in varying climates.
Digital Monitoring Technologies
Today's digital monitoring technologies equip you with unprecedented capabilities to assess your building's structural integrity through real-time analysis systems and integrated smart sensors. You'll maximize the efficiency of your brick repair projects by implementing remote monitoring systems that continuously track stress points, moisture levels, and thermal variations across your commercial façade. These advanced digital tools enable you to identify potential issues before they escalate, allowing for precise, data-driven maintenance decisions that protect your architectural investment.
Real-Time Structural Analysis
Digital monitoring technologies have revolutionized structural analysis in commercial brick architecture through sophisticated sensor networks and real-time data collection. You'll find that these advanced systems now enable you to track structural integrity continuously, identifying potential issues before they become critical problems. Through strategically placed sensors, you can monitor stress points, moisture levels, and thermal expansion in your brick structures with unprecedented accuracy.
When you implement real-time monitoring solutions, you're gaining access to data streams that provide immediate insights into your building's performance. The system alerts you to minute changes in brick positioning, joint integrity, and load distribution patterns. You can track displacement measurements down to millimeter precision, while simultaneously analyzing vibration patterns and settlement rates that might affect your structure's stability.
Smart Sensor Integration
Modern sensor integration systems incorporate five essential components that work together to monitor brick structures: environmental sensors, strain gauges, displacement monitors, moisture detectors, and thermal imaging devices. You'll find these systems are revolutionizing how you maintain and repair commercial brick buildings, offering real-time data that's vital for preventive maintenance. Furthermore, integrating these systems can significantly enhance your ability to implement effective waterproofing techniques that protect against moisture-related damage.
To achieve ideal sensor accuracy, you'll need to strategically position your monitoring devices throughout the structure. You can place strain gauges at critical load-bearing points, while moisture detectors should be installed near areas prone to water infiltration. The integration challenges you'll face often stem from calibrating these various sensors to work in harmony, but modern software solutions help streamline this process.
When you're implementing smart sensors, you'll want to focus on creating a thorough monitoring network. Your system should include wireless connectivity options that allow for remote data access and analysis. By connecting these components to a central monitoring platform, you're able to receive instant alerts about structural changes, moisture levels, and thermal variations that could compromise your building's integrity.
Remote Monitoring Systems
Remote monitoring technologies have transformed traditional brick maintenance into a precision-driven discipline through cloud-based observation platforms. You'll find that these systems allow your facility management team to track structural integrity, moisture levels, and thermal performance in real-time, without constant on-site presence.
When you implement remote sensing capabilities, you're gaining access to continuous data streams that detect early warning signs of brick deterioration. Your monitoring system will alert you to microscopic changes in mortar joints, brick displacement, and developing stress patterns before they become visible to the naked eye.
The predictive maintenance algorithms you'll utilize can analyze historical data patterns to forecast potential failure points in your brick façade. You're able to establish customized threshold alerts that trigger automated notifications when specific parameters exceed normal ranges. This means you can schedule interventions precisely when needed, rather than relying on arbitrary maintenance schedules.
Flexible Joint Solutions
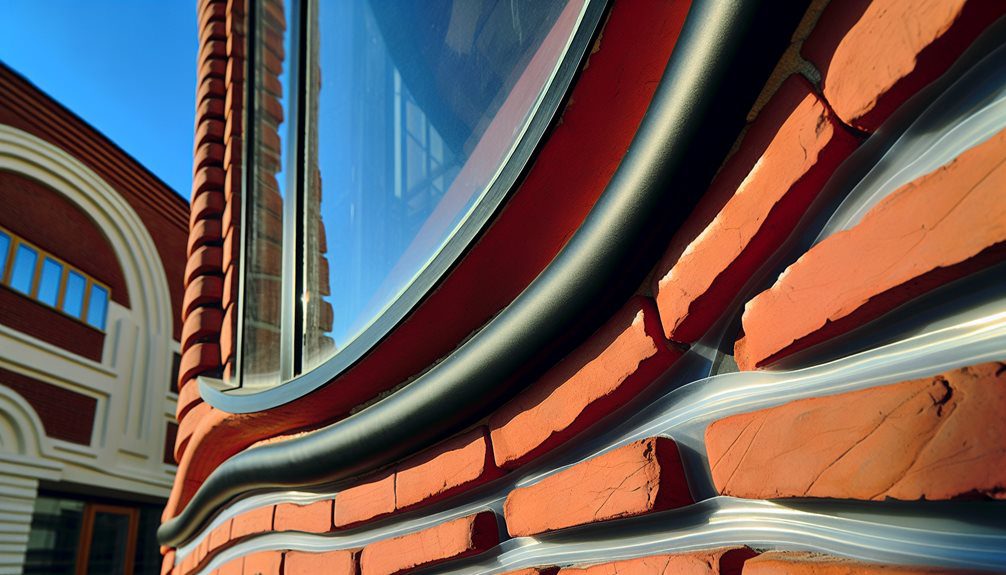
Flexible joints within commercial brick structures serve as critical components for managing thermal expansion, settling, and seismic movement. When you're selecting flexible joint materials, you'll need to take into account factors like weather resistance, compression capacity, and durability under repeated movement cycles. Today's high-performance sealants and compressible fillers offer superior elasticity while maintaining structural integrity.
Your expansion joint design must account for anticipated building movement patterns and local climate conditions. You'll want to implement joints at critical stress points: vertical joints at 20-30 foot intervals, horizontal joints at floor lines, and around openings where stress concentration occurs. Modern flexible joint solutions include pre-compressed foam sealants, hybrid polymer compounds, and multi-component urethane systems.
To optimize joint performance, you'll need to guarantee proper width-to-depth ratios, typically 2:1 for most applications. You can enhance joint durability by incorporating backup materials and bond breakers to prevent three-sided adhesion. Regular inspection of these joints should be part of your maintenance protocol, as early detection of deterioration can prevent more extensive masonry damage and costly repairs. Additionally, applying waterproofing techniques can further protect these joints from moisture damage and extend their lifespan.
Weather-Resistant Coating Applications
When you're protecting commercial brick surfaces, silicone-based sealants offer superior performance through their molecular bonding capabilities and UV-resistant properties. You'll achieve maximum weather protection by applying a penetrating silicone coating that creates an invisible, breathable barrier while maintaining the brick's natural appearance. Your long-term protection strategy should incorporate scheduled reapplication intervals based on exposure conditions, typically every 5-7 years for ideal performance against moisture infiltration and freeze-thaw cycles. Additionally, incorporating waterproofing solutions can further enhance the longevity of your masonry structures.
Silicone-Based Sealant Benefits
Through advanced silicone-based sealant applications, commercial buildings gain exceptional protection against harsh weather conditions while maintaining structural integrity. When you're selecting a sealant solution for your brick structures, silicone-based products offer superior adhesion properties that outperform traditional alternatives. These sealants create a flexible, yet durable barrier that moves with your building's natural thermal expansion and contraction.
You'll find that silicone applications provide remarkable resistance to UV radiation, extreme temperatures, and moisture infiltration. The material's molecular structure guarantees long-term performance, typically lasting 20-30 years with proper installation. Your maintenance teams will appreciate the reduced need for frequent reapplication, cutting down on labor costs and building downtime.
What sets silicone sealants apart is their ability to maintain elasticity without hardening or cracking over time. You can expect excellent performance in joints between brick facades and other building materials, as the sealant's chemical composition creates strong bonds with both porous and non-porous surfaces. This versatility makes it an ideal choice for complex architectural designs where different materials intersect, guaranteeing your building's envelope remains watertight and energy-efficient. Additionally, the use of silicone sealants aligns with best practices in masonry restoration services, ensuring enhanced durability and aesthetic appeal.
Long-Term Protection Methods
Building on the protective qualities of silicone sealants, weather-resistant coating applications represent the next level of extensive brick preservation. You'll find that these advanced solutions provide thorough protection against moisture infiltration, UV damage, and thermal stress when properly applied as part of your preventive maintenance strategy.
To maximize the effectiveness of weather-resistant coatings, you'll need to start with a detailed durability assessment of your existing masonry. This evaluation helps you identify vulnerable areas and determine the best coating system for your specific needs. You can choose from penetrating sealers that maintain the brick's natural appearance or film-forming coatings that offer enhanced protection while altering the surface aesthetics.
For best results, you'll want to implement a three-phase protection approach: surface preparation, coating application, and periodic monitoring. The preparation phase includes cleaning, repairs, and moisture testing. During application, you'll need to maintain consistent coverage and proper mil thickness. Your monitoring program should include quarterly inspections and documentation of coating performance to address any signs of deterioration before they become significant issues. Additionally, partnering with a certified, licensed, and insured contractor ensures that the application meets industry standards and enhances the longevity of your brickwork with high-quality materials.
Structural Reinforcement Methods
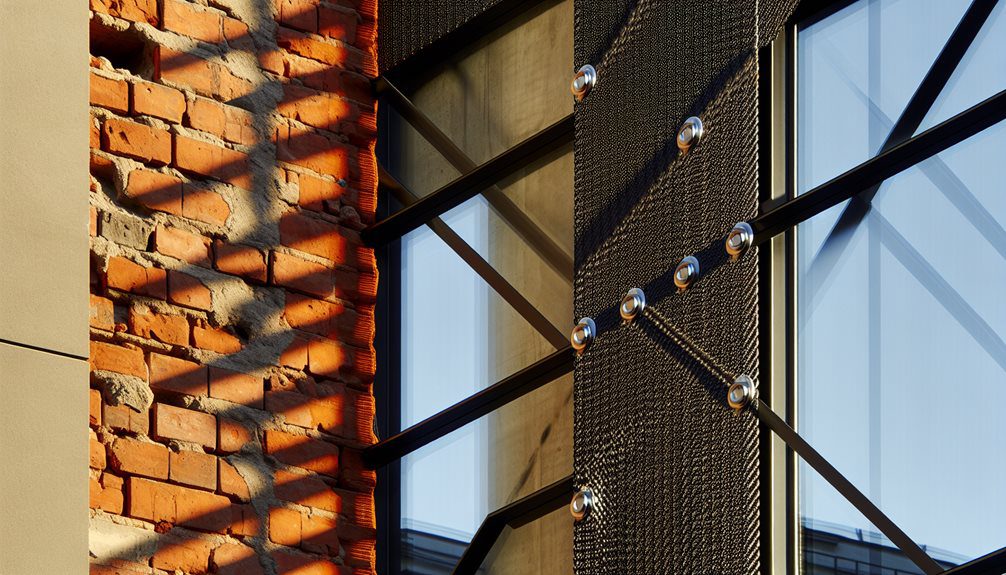
Commercial brick structures often call for robust reinforcement methods to maintain their structural integrity and load-bearing capacity. You'll need to focus on strategic implementation of load-bearing enhancements, which include steel tie rods, reinforced concrete columns, and composite materials that work together with existing masonry.
When you're dealing with seismic retrofitting, it is crucial to integrate lateral bracing systems and moment frames that distribute forces evenly throughout the structure. You can strengthen your building's core by installing helical ties between wythes of masonry or adding carbon fiber reinforcement polymers (CFRP) to critical stress points.
For ideal structural stability, you'll want to implement a combination of traditional and modern reinforcement techniques. Start by analyzing weak points in corner joints and wall intersections, then install appropriate anchoring systems. Consider using epoxy injection for crack stabilization, followed by the installation of bed-joint reinforcement. Your masonry walls will benefit from strategic placement of vertical and horizontal reinforcement bars, ensuring they're properly bonded to maintain the building's structural cohesion while preserving its architectural character. Proper restoration is essential to prevent extensive damage and ensure longevity in masonry structures.
Moisture Control Techniques
Effective moisture control represents a critical defense mechanism for preserving brick structures against water-related deterioration. You'll need to implement a thorough approach that combines both preventive and remedial solutions to protect your building's integrity. By installing proper moisture barriers, you're creating an essential shield that prevents water infiltration while maintaining the structure's breathability.
When you're addressing moisture issues, you'll want to focus on establishing efficient drainage systems that direct water away from the building's foundation and walls. You can integrate weep holes at strategic intervals, making sure they're properly spaced and maintained to facilitate adequate ventilation and water evacuation. Installing through-wall flashing at critical junctions will help you channel moisture outward, preventing it from becoming trapped within the wall assembly.
You'll find that incorporating hydrophobic sealants and vapor-permeable coatings provides an additional layer of protection without compromising the brick's natural ability to release trapped moisture. Remember to maintain clear drainage paths around your building's perimeter and regularly inspect your moisture control systems to verify they're functioning effectively. Additionally, utilizing tuckpointing for restoring mortar joints can further enhance your building's moisture resistance by ensuring that all mortar joints are properly sealed and maintained.
Mixed-Material Interface Solutions
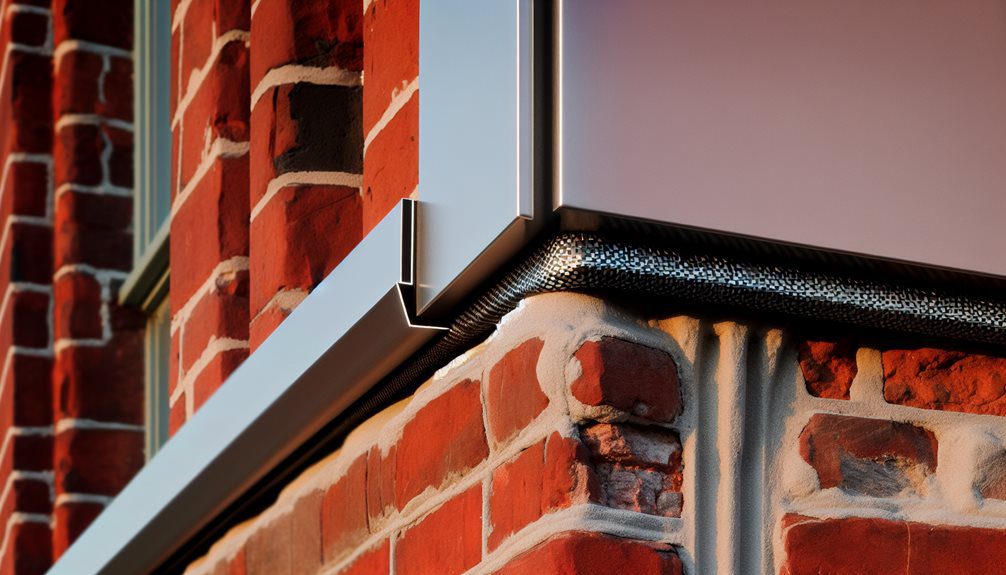
While moisture control safeguards the overall structure, the points where different materials meet brick surfaces present unique challenges that demand specialized attention. You'll need to address these intersections with carefully planned mixed material bonding solutions that maintain both structural integrity and aesthetic compatibility.
When you're dealing with brick-to-metal connections, you'll want to implement flexible sealant systems that accommodate thermal movement while preventing moisture infiltration. For brick-to-concrete interfaces, you'll need to install proper expansion joints and compatible bonding agents that account for different expansion rates. You can achieve superior results by using modified epoxy mortars specifically designed for mixed material applications.
To maintain aesthetic compatibility at these junctions, you'll find success using color-matched connection materials and architectural breaks that turn potential weak points into intentional design features. Consider implementing compression seals at critical interfaces, as they're particularly effective where brick meets modern curtain wall systems. When you're working with these solutions, remember to factor in your building's specific movement patterns and environmental stresses to select interface treatments that'll provide long-term stability while preserving your structure's visual coherence. Additionally, proper waterproofing is essential to protect structures from water damage and enhance the longevity of your repairs.
Sustainable Restoration Practices
Modern restoration practices demand environmentally conscious approaches that balance historical preservation with sustainability goals. When you're planning your brick restoration project, you'll need to take into account both traditional craftsmanship and sustainable materials that meet today's environmental standards. By implementing eco-friendly repair techniques, you can achieve green certifications while maintaining the building's structural integrity.
You'll want to focus on sourcing locally manufactured replacement bricks to reduce transportation emissions and support regional economies. Think about using low-VOC mortars and sealants that don't compromise the building's breathability. You can also incorporate recycled aggregate in your mortar mix, which reduces landfill waste while maintaining necessary structural properties. Additionally, tuckpointing for mortar joint repair is a crucial technique that enhances both the longevity and aesthetics of the brickwork.
Document your sustainable choices throughout the restoration process, as this documentation will support your building's green certifications. You'll find that integrating water-efficient cleaning methods and establishing waste reduction protocols during repairs will markedly lower your project's environmental impact. When you're selecting preservation treatments, prioritize those that extend the lifecycle of existing materials rather than requiring complete replacement, as this approach aligns with both conservation principles and sustainability objectives.
Frequently Asked Questions
How Long Does a Typical Commercial Brick Repair Project Take to Complete?
Your commercial brick repair's project timeline typically ranges from 2-8 weeks, depending on factors you'll need to take into account. Small repairs might take just days, while extensive restorations can extend longer. You'll find repair efficiency varies based on your building's size, damage severity, weather conditions, and crew size. When you're planning, it's best to add a 20% buffer to estimated completion times for unexpected challenges that often arise during repairs.
What Are the Cost Differences Between Traditional and Innovative Brick Repair Methods?
When you're comparing brick repair methods, you'll find traditional approaches typically cost 20-30% less upfront but often require more frequent maintenance. Innovative solutions, while having higher initial costs, offer better repair efficiency and long-term savings. You'll see the most significant cost differences in labor expenses – modern techniques can reduce your working hours by up to 40%. Consider your project's timeline and budget constraints to determine which method best serves your needs.
Can Brick Repairs Be Performed During Winter Months in Cold Climates?
You can perform brick repairs during winter months, but you'll need to take specific precautions. When temperatures drop below 40°F (4°C), you'll want to use cold weather admixtures and heated materials. You'll also need to protect your work area with temporary enclosures and heating systems. While winter repairs are possible, they'll require more planning, monitoring, and specialized materials. Many contractors prefer scheduling non-emergency repairs during warmer months for ideal results and cost efficiency.
How Often Should Commercial Brick Structures Undergo Professional Inspection and Maintenance?
You'll want to schedule thorough brick inspections at least once every 3-5 years for your commercial property, though you may need more frequent checks if you're in areas with harsh weather. Don't skip your annual visual assessments – they're essential for catching early warning signs. Regular maintenance is your best defense against costly repairs, so you're better off establishing a proactive inspection schedule with your building maintenance team.
What Insurance Considerations Apply When Using Experimental Brick Repair Technologies?
When you're implementing experimental repair technologies, you'll need enhanced liability coverage that specifically addresses technology risks. You should update your professional indemnity insurance to cover potential failures of new methods, and guarantee your policy includes both immediate and long-term performance guarantees. It's essential that you work with insurers who understand emerging construction technologies and can tailor coverage to protect against unforeseen complications in both materials and application processes.