When restoring masonry in multi-story commercial buildings, you'll face several key challenges that require careful planning. You must guarantee scaffold safety and OSHA compliance while coordinating with tenant operations to minimize disruptions. Weather conditions will impact your material performance and project timeline, making it essential to implement proper moisture barriers and schedule work strategically. You'll need to assess structural issues thoroughly, including cracks, spalling, and mortar joint failures, while guaranteeing all restoration materials remain compatible with existing masonry. Understanding these interconnected challenges and their technical solutions will help you develop an effective restoration strategy that maintains both building integrity and occupant satisfaction.
Safety and Access Requirements
Safety protocols and access planning form the foundation of any masonry restoration project. You'll need to establish thorough scaffold safety measures before your team begins work, guaranteeing all access equipment meets OSHA standards and local building codes. When you're dealing with multi-story structures, you must implement proper tie-back systems, secure anchor points, and regular inspection schedules for all suspended scaffolding.
You'll find that coordinating access equipment requires careful consideration of both building occupants and pedestrian traffic. You should install debris netting, overhead protection, and clearly marked safety zones to protect people below. Your project planning must include designated material staging areas and equipment zones that don't interfere with daily building operations.
When you're setting up your work platforms, verify they're engineered to handle specific load requirements for both workers and materials. You'll need to maintain proper clearances from power lines and other building systems. Your access plan should include emergency evacuation procedures and weather contingency protocols. Remember that you're responsible for daily safety checks of all access equipment, including guardrails, toe boards, and platform stability components. Additionally, it is crucial to have a solid understanding of masonry restoration techniques to ensure effective repair and maintenance strategies are employed throughout the project.
Weather Impact on Restoration
Weather conditions pose considerable challenges that can dramatically affect masonry restoration timelines and material performance. You'll need to carefully monitor temperature, humidity, and precipitation levels throughout your project, as these factors directly influence mortar curing rates and material adhesion. Weather fluctuations can compromise the integrity of newly applied materials, particularly during the critical initial setting period.
When you're planning restoration work, you must account for moisture infiltration risks during periods of rain or high humidity. You'll want to implement proper moisture barriers and temporary sheltering systems to protect ongoing work. Temperature extremes can affect your restoration schedule considerably – you can't apply most masonry materials when temperatures fall below 40°F (4°C) or rise above 90°F (32°C).
You should schedule your most moisture-sensitive tasks during periods of stable weather and maintain detailed weather logs throughout the project. It's crucial to incorporate weather-related contingencies into your project timeline and budget. By using specialized rapid-setting materials and temporary climate controls, you can minimize weather-related delays while ensuring proper curing conditions for your masonry repairs. Additionally, applying a siloxane clearcoat can help protect newly restored areas from moisture intrusion.
Tenant Operations During Repairs
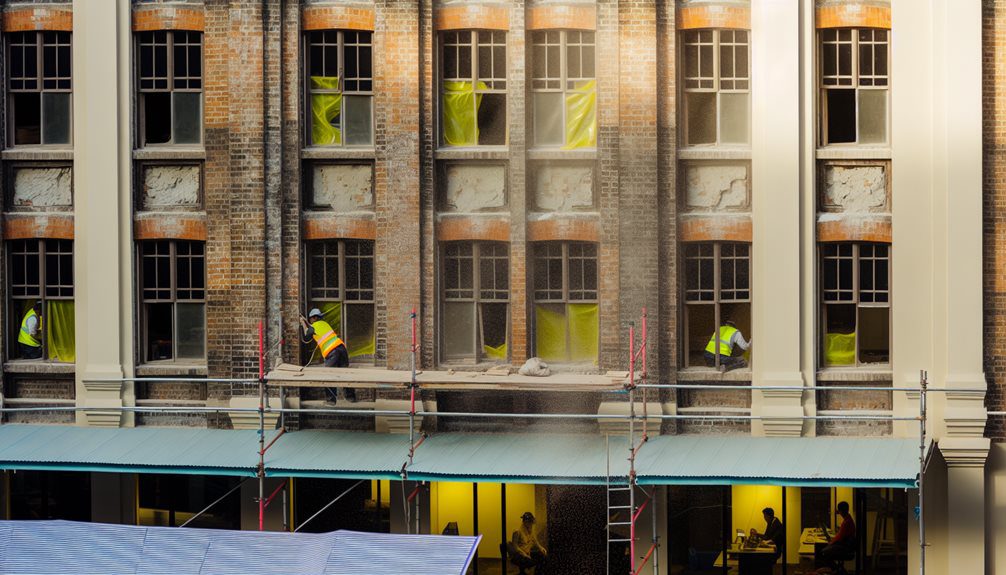
Beyond managing environmental factors, coordinating restoration work with active tenant operations requires strategic planning and clear communication protocols. You'll need to establish a thorough tenant communication system that includes regular updates, progress reports, and immediate notifications about any disruptions to normal business operations. This guarantees all stakeholders remain informed and can adjust their activities accordingly.
Schedule coordination becomes critical when you're managing restoration work around occupied spaces. You'll want to segment the project into phases that minimize impact on tenant operations, potentially including after-hours work for particularly disruptive tasks. Consider creating temporary pathways and protective barriers to maintain safe access to tenant spaces while protecting their assets from dust and debris.
You must also coordinate mechanical system interruptions, such as HVAC shutdowns or water service disruptions, with tenant business hours. It's important to provide advance notice of these interruptions and work with tenants to identify critical operational periods when such disruptions would be most detrimental. By developing detailed workflow plans that account for tenant needs, you'll maintain positive relationships while facilitating restoration work progresses efficiently. Additionally, engaging with a team experienced in masonry restoration will ensure that the project meets high-quality standards and adheres to municipal codes.
Historical Preservation Considerations
Masonry restoration of historic buildings demands strict adherence to preservation standards while meeting modern building codes. When you're working on a historically significant structure, you'll need to document existing conditions thoroughly and research the building's original construction methods before beginning any repairs.
You'll find that preservation guidelines often require you to maintain the building's historical significance by using period-appropriate restoration techniques. This means you'll need to source matching materials, including historically accurate mortar compositions and masonry units that replicate original dimensions and textures. You're also obligated to preserve as much original material as possible, making repairs rather than replacements whenever feasible.
Before starting work, you must obtain approval from local preservation boards and guarantee your restoration plans comply with the Secretary of the Interior's Standards for Historic Preservation. You'll want to engage specialists who understand traditional masonry methods and can execute repairs using both historical and contemporary techniques. Timely intervention is crucial to prevent extensive damage and costly repairs, as you're not just fixing a building – you're preserving a piece of architectural heritage for future generations. Document all your restoration work meticulously, as these records become part of the building's historical record.
Material Selection and Compatibility
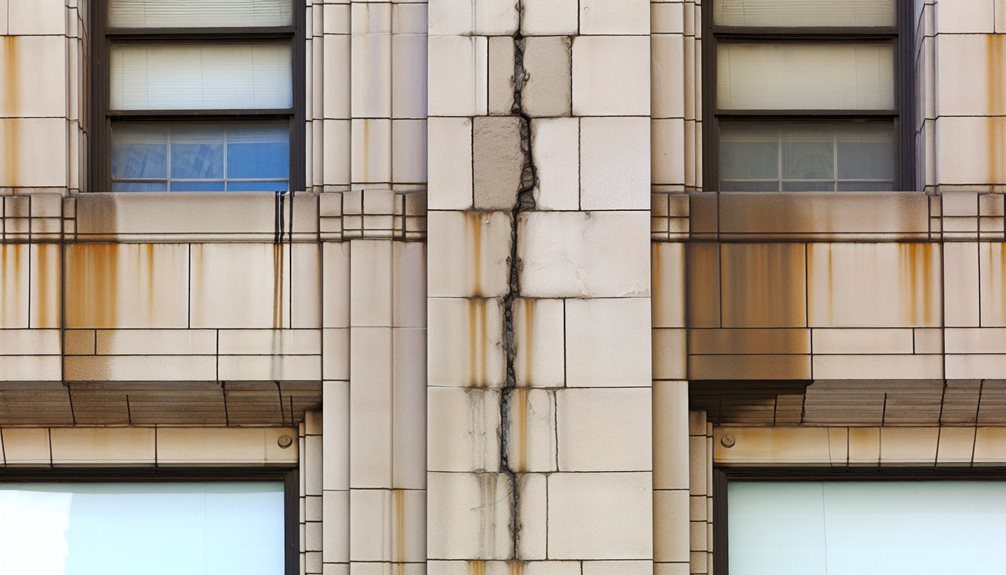
Selecting appropriate materials for masonry restoration requires careful analysis of both existing and replacement components. You'll need to evaluate the physical and chemical properties of original materials to guarantee compatibility with new ones. When you're matching mortars, bricks, or stones, consider both material durability and aesthetic consistency to maintain the building's structural integrity and appearance.
You'll want to test your replacement materials for key properties including porosity, water absorption, and thermal expansion rates. These characteristics must align closely with existing masonry to prevent differential movement and potential damage. If you're working with historic structures, you'll find that modern materials often need modification to match the performance characteristics of original components.
When you're selecting replacement materials, remember to account for weathering patterns and aging processes. It's essential that you choose materials that will age harmoniously with existing masonry. Consider conducting mock-ups and sample installations to verify compatibility before proceeding with large-scale restoration. You can protect your investment by documenting material specifications and maintaining detailed records of testing results for future reference and maintenance work. Additionally, waterproofing treatments should be applied post-repair to mitigate water intrusion and ensure longevity.
Structural Assessment Methods
You'll need to employ systematic visual inspection techniques as your first step in evaluating masonry structural integrity, checking for cracks, displacement, and deterioration patterns. Your thorough examination must include documenting surface conditions, moisture penetration points, and joint integrity through high-resolution photography and detailed mapping of damage locations. To quantify the structure's stability, you'll need to conduct load-bearing capacity tests using non-destructive methods such as flat-jack testing or ground-penetrating radar to evaluate internal stresses and hidden structural weaknesses. Additionally, it is crucial to consider waterproofing measures to protect the building from moisture damage during the restoration process.
Visual Inspection Techniques
Professional structural assessment begins with systematic visual inspection techniques that form the foundation of masonry evaluation. You'll need to examine the building's exterior surfaces methodically, starting from ground level and working your way up, documenting every crack, spall, and displacement you observe. Modern digital imaging technology allows you to capture high-resolution photographs of deterioration patterns and structural concerns for detailed analysis.
When you're dealing with tall commercial structures, you'll find drone technology particularly valuable for accessing difficult-to-reach areas safely. You can identify areas of water infiltration, efflorescence, and mortar joint deterioration through aerial imagery while maintaining detailed inspection logs. As you conduct your visual assessment, you'll want to pay special attention to common problem areas: parapets, cornices, and locations where different materials interface.
You should map all observed defects on elevation drawings, noting their size, location, and apparent severity. This documentation becomes essential when you're developing your restoration strategy and prioritizing repairs. Remember to photograph and document any temporary repairs or previous restoration attempts, as these often indicate recurring issues that'll need addressing. Additionally, understanding the importance of masonry maintenance can help guide your overall approach to the evaluation process.
Load-Bearing Capacity Testing
In evaluating masonry structures, accurate load-bearing capacity testing provides essential data about the building's structural integrity. You'll need to employ both non-destructive and minimally invasive techniques to assess the masonry's current load-bearing capabilities and identify potential weaknesses.
Start your load-bearing analysis by using flat-jack testing, which you'll insert into mortar joints to measure compressive stress and deformation characteristics. You can complement this with core sampling at strategic points, allowing you to analyze the material's composition and strength in laboratory conditions. When you're working with historic structures, you'll want to prioritize non-destructive methods like ground-penetrating radar and ultrasonic pulse velocity testing.
Don't forget to factor in dynamic loading conditions. You'll need to assess how the structure responds to various stress scenarios, including wind loads, seismic activity, and thermal expansion. By collecting data from multiple test points, you're able to create a thorough structural integrity model. This information becomes vital when you're determining the scope of restoration work and selecting appropriate reinforcement methods. Additionally, consider consulting with professionals who specialize in commercial masonry restoration to ensure best practices are followed. Remember to document all test results meticulously, as they'll serve as your baseline for future assessments.
Frequently Asked Questions
How Long Does a Typical Masonry Restoration Project Take to Complete?
Your masonry restoration project's timeline can range from 2-12 months, depending on several key factors. You'll need to account for the project scope, weather conditions, and required permits. The restoration phases typically include assessment (1-2 weeks), preparation (2-4 weeks), repair work (4-16 weeks), and finishing touches (2-4 weeks). You'll find that more complex projects with extensive damage or historical considerations will extend toward the longer end of this range.
What Are the Average Costs per Square Foot for Masonry Restoration?
You'll find that masonry restoration costs typically range from $15 to $60 per square foot, though your specific project may vary considerably. Several cost factors influence this range, including the restoration techniques required, material conditions, and labor intensity. If you're dealing with simple repointing, you might pay closer to $15-25, but when you need extensive restoration involving replacement and structural repairs, you'll likely face costs at the higher end.
Can Damaged Masonry Affect Indoor Air Quality and Building Energy Efficiency?
You'll find that masonry deterioration can greatly impact your building's indoor environment and energy performance. When your masonry develops cracks or gaps, you're likely to experience air infiltration that lets indoor pollutants enter while compromising your HVAC system's efficiency. This can lead to higher energy bills and poor air quality. By addressing these issues promptly, you'll protect both your building's occupants and your energy budget through improved thermal performance.
How Often Should Commercial Buildings Undergo Preventive Masonry Maintenance Inspections?
You'll want to schedule preventive maintenance inspections for your commercial building at least annually, with more frequent checks in severe weather regions. It's best to conduct detailed inspections every spring and fall to catch potential issues early. Your inspection frequency should increase for buildings over 30 years old or those exposed to harsh conditions. Don't forget to document each inspection – this helps you track patterns and plan for future maintenance needs.
What Warranties or Guarantees Typically Come With Masonry Restoration Work?
You'll typically find two main warranty types with masonry restoration work: workmanship and materials. Workmanship warranties usually cover labor and installation for 1-5 years, while material warranties can extend 10-20 years. Your guarantee duration will depend on the scope of work and materials used. It's important that you carefully review warranty terms, as they'll outline specific maintenance requirements you'll need to follow to keep your coverage valid.