You'll need a thorough approach to restore industrial masonry effectively. Start by evaluating deterioration signs like cracking, efflorescence, and spalling to determine the scope of work. You'll want to implement chemical cleaning methods appropriate for your masonry type, followed by proper surface preparation for repairs. Focus on detailed mortar joint repointing, using materials that match historical compositions while meeting modern performance standards. Don't forget to address structural cracks and implement proper waterproofing systems. A systematic quality control process, combined with detailed documentation and regular maintenance, will guarantee your industrial facility's masonry remains structurally sound for decades to come.
Common Masonry Deterioration Signs
Numerous visible indicators can alert you to masonry deterioration before structural damage becomes severe. When you're examining your industrial facility's masonry surfaces, look for cracking patterns, which often indicate structural movement or thermal stress. You'll notice these masonry aging indicators primarily at mortar joints and around openings where stress concentrates.
Environmental impact plays a vital role in deterioration. You'll want to check for efflorescence, those white crystalline deposits that signal water infiltration and salt migration within the masonry. Spalling, where the brick face flakes or peels, indicates freeze-thaw damage that's compromising your wall's integrity. Watch for mortar erosion, particularly on surfaces exposed to prevailing winds and rain.
You should also inspect for biological growth like moss or algae, especially in shaded areas where moisture persists. These organisms accelerate deterioration by retaining water against the masonry surface. Check for displacement or bulging in wall sections, which suggests potential structural issues. If you observe dark patches or staining, you're likely seeing water penetration points that require immediate attention to prevent further degradation of your masonry system. Additionally, addressing these issues swiftly can enhance the overall structural integrity of your buildings and prolong their lifespan.
Chemical Cleaning and Surface Preparation
Before initiating any masonry restoration work, proper chemical cleaning and surface preparation establish the foundation for successful repairs. You'll need to select appropriate chemical agents based on your masonry type and deterioration conditions, as different materials respond uniquely to various cleaners. Start with the gentlest cleaning method and progress to stronger solutions only when necessary.
When you're applying surface treatments, you'll want to protect adjacent materials and guarantee proper ventilation. Test your chosen chemical agents on a small, inconspicuous area first to evaluate their effectiveness and prevent potential adverse reactions. Remember that historical masonry often requires specialized approaches that won't compromise the material's integrity or historical value.
You must thoroughly rinse treated surfaces to remove all chemical residue, as leftover cleaning agents can continue to react with the masonry and cause further deterioration. Document your cleaning process, including dwell times and dilution ratios, to maintain consistency across the project. Once you've completed the cleaning phase, allow adequate drying time before proceeding with repairs or applying any protective coatings. This guarantees ideal adhesion and long-term restoration success. Additionally, it is crucial to consider waterproofing solutions to protect buildings from water damage during the restoration process.
Mortar Joint Repointing Methods
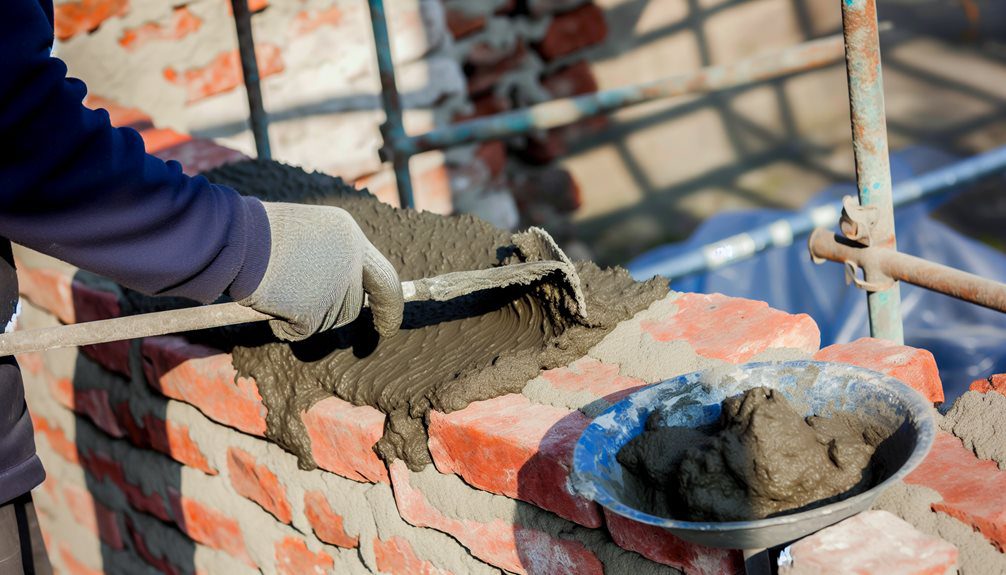
You'll need to begin repointing by properly preparing the deteriorated joints through careful removal of old mortar to a minimum depth of 2-2.5 times the joint width using appropriate hand tools or power tools. When applying new mortar, you must match the historic mortar's composition and color while ensuring the joints are damp but not wet before application. You should install the new mortar in layers, allowing each layer to become thumbprint-hard before applying the next, and finish with proper tooling to match the original joint profile. Additionally, selecting high-quality materials is essential for achieving a durable and aesthetically pleasing result, as high-quality materials significantly impact the longevity of masonry restoration.
Joint Preparation Guidelines
Proper joint preparation serves as the cornerstone of successful mortar repointing work. You'll need to begin by removing all deteriorated mortar to a minimum depth of 2-3 times the joint's width, typically ¾ to 1 inch deep. It's crucial to maintain consistent depth while avoiding damage to surrounding masonry units during this process.
Before applying any joint filling materials, you must thoroughly clean the cavity using compressed air or water to remove all debris and dust. You'll want to verify the joint surfaces are sound and free from any loose particles that could compromise adhesion. When implementing joint sealing techniques, you'll need to pre-wet the joints to prevent rapid moisture loss from the new mortar, but avoid oversaturation.
For best results, you should inspect each prepared joint for uniform depth and square-cut backs. Historic structures require special attention – you'll need to document the original joint profile and verify your preparation methods don't compromise the building's architectural integrity. If you encounter any embedded metal or unusual materials during preparation, consult a preservation specialist before proceeding with the repointing work. Additionally, consider the benefits of waterproofing solutions to protect against moisture damage after repointing.
Proper Application Procedures
Mastering mortar joint repointing requires strict adherence to proven application techniques. You'll need to work in small sections, typically 3-5 feet at a time, to guarantee proper mortar consistency and bond strength. Start by applying your restoration materials to the back of the joint first, then work forward in layers not exceeding 1/4 inch thickness.
When using your masonry tools, you'll want to pack each layer firmly, making sure there aren't any voids that could compromise the joint's integrity. You're aiming for full contact between the new mortar and the existing masonry surfaces. Don't forget to maintain consistent pressure while tooling the joints to achieve uniform compression and appearance.
As you work, you'll need to match the original joint profile using appropriate tooling techniques. If you're working on a historic structure, you'll want to replicate the original joint finish precisely – whether it's concave, weathered, or flush. Time your tooling carefully; the mortar should be thumbprint-hard before final finishing. You're part of a long tradition of craftspeople who've preserved these structures, so maintaining these time-tested application procedures is essential to successful restoration. Additionally, using top-grade materials ensures durability and longevity in your work.
Structural Crack Assessment and Repair
Structural crack assessment begins with detailed photographic and diagrammatic documentation of crack patterns, which you'll need to map across all affected masonry surfaces using standardized notation methods. You'll then classify the damage severity using a three-tier system that evaluates crack width, depth, and potential structural implications through both visual inspection and diagnostic tools such as crack monitors and ultrasonic testing. For load-bearing wall repairs, you must determine whether the cracks indicate active movement or stabilized damage before implementing appropriate repair strategies such as crack injection, mechanical pinning, or full section reconstruction. Regular maintenance can help mitigate common masonry issues that may exacerbate crack formation over time.
Crack Pattern Documentation Methods
A spider's web of cracks across aging masonry tells a detailed story of structural stress and material fatigue. You'll need to capture this information systematically using proven crack identification techniques that industrial restoration specialists have refined over decades. Start by creating detailed sketches that map each crack's location, direction, and width using a standardized notation system that you and your team can easily reference.
When you're implementing photographic documentation methods, you'll want to use high-resolution digital cameras with macro lens capabilities. Position reference markers or crack gauges in your shots to provide precise scale measurements. You'll find it helpful to establish a grid system across the affected area, photographing each section methodically and recording the date, time, and environmental conditions for each image.
Digital mapping tools now let you overlay these photos with CAD drawings, creating a thorough record that you can share with your restoration team. You'll need to document both the surface patterns and, where possible, the depth of penetration using specialized inspection tools. This data becomes invaluable when you're developing your repair strategy and monitoring the effectiveness of your interventions over time. Additionally, engaging a licensed and insured masonry restoration specialist can ensure that the repair work adheres to industry standards.
Damage Severity Classification System
Within established restoration protocols, damage severity classification follows a systematic five-tier assessment framework that you'll need to master before undertaking any masonry repairs. You'll find that Level 1 represents superficial or cosmetic damage with hairline cracks under 0.1mm, while Level 2 indicates minor structural concerns with cracks ranging from 0.1-2.0mm. As a restoration professional, you'll recognize Level 3 damage by moderate structural issues, featuring cracks between 2.0-5.0mm and potential mortar joint deterioration.
When you're conducting your damage categorization, you'll need to document Level 4 conditions carefully, as these represent severe structural compromise with cracks exceeding 5.0mm and possible displacement. The most critical classification, Level 5, demands immediate intervention due to imminent structural failure risks. Your severity assessment must account for crack width, pattern distribution, and underlying causes like foundation settlement or thermal expansion.
In addition, understanding the importance of waterproofing techniques can greatly enhance the longevity of your masonry repairs. You'll want to document each level thoroughly using standardized assessment forms that include photographic evidence, measurement data, and detailed observations of surrounding masonry conditions. This systematic approach guarantees consistency across your restoration team and enables proper repair strategy development.
Load-Bearing Wall Repairs
Building upon the damage classification system, load-bearing wall repairs require precise structural analysis and methodical intervention protocols. You'll need to begin with a thorough assessment of the wall's structural integrity, examining both visible cracks and potential hidden damage that could compromise the building's stability.
When you're dealing with load-bearing materials, it's essential to implement temporary support systems before initiating any repairs. You'll want to install steel shores or needle beams to redistribute the structural load while you work. Modern reinforcement techniques include the installation of helical ties, crack stitching, and grouting systems that you can adapt to your specific masonry conditions.
You'll find that historical structures often require specialized approaches that honor original construction methods while incorporating contemporary strengthening solutions. When you're repairing structural cracks, you'll need to take into account the building's age, settlement patterns, and load distribution characteristics. Start by removing deteriorated mortar and masonry units, then implement your chosen reinforcement technique, whether it's through steel plates, fiber-reinforced polymers, or traditional masonry methods. Remember that successful load-bearing wall repairs depend on maintaining structural continuity throughout the restoration process. Additionally, seeking assistance from a certified and insured masonry restoration company can ensure that the work meets industry standards and preserves architectural beauty.
Waterproofing Industrial Masonry Walls
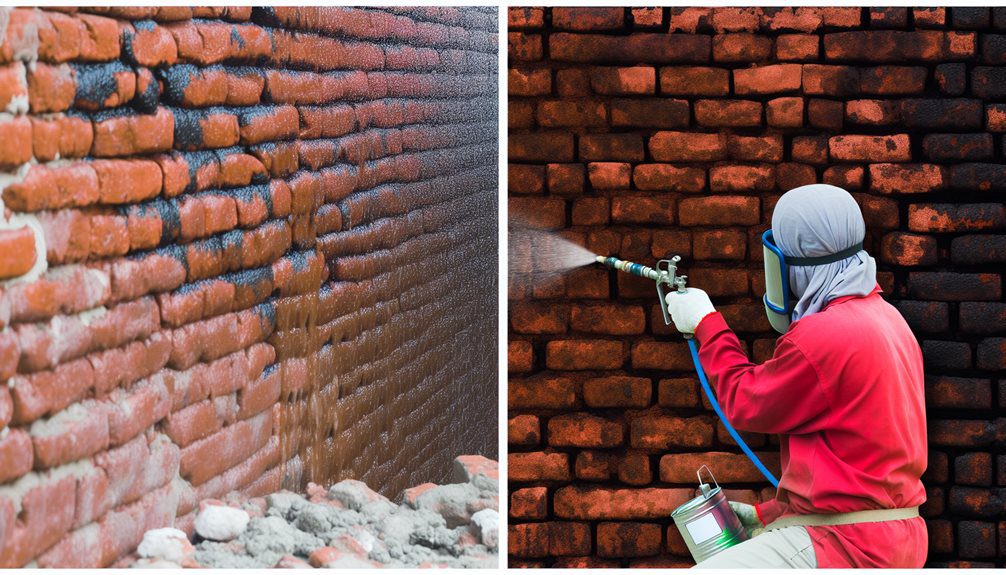
Through decades of industrial application, waterproofing masonry walls in manufacturing facilities has evolved from simple sealant applications to extensive moisture management systems. You'll find today's methods incorporate multiple layers of protection, including waterproof membrane technologies that prevent moisture infiltration while allowing walls to breathe.
When you're planning your industrial masonry waterproofing project, you'll need to start with a thorough assessment of your facility's moisture exposure patterns. You can identify problem areas by conducting dye tests and analyzing historical moisture data. Modern moisture barriers now include crystalline treatments that penetrate deep into the masonry's pore structure, creating a permanent waterproof barrier.
You'll want to implement a systematic approach: first applying a primary waterproof membrane, followed by drainage mats and moisture barriers at critical junctions. You're not just protecting against visible water damage – you're preventing costly equipment corrosion and product contamination. Your facility's specific requirements will determine whether you'll need positive-side or negative-side waterproofing applications. Remember to take into account seasonal temperature fluctuations when selecting your waterproofing materials, as thermal expansion can affect long-term performance. Additionally, consider incorporating effective waterproofing techniques to enhance the durability of your masonry structures.
Historic Brick Restoration Considerations
Preservation of historic brick structures demands meticulous attention to period-specific materials and techniques. You'll need to carefully document existing conditions and identify original construction methods before beginning any restoration work. Understanding your building's historic significance helps you make informed decisions about which elements to preserve, repair, or replace.
When you're facing restoration challenges, you'll want to analyze the original mortar composition through laboratory testing. This allows you to match the historic mix ratio, guaranteeing compatibility with existing materials. You'll find that period-appropriate lime mortars are often softer than modern Portland cement, which is essential for maintaining proper moisture movement through the masonry system.
Your restoration work should prioritize salvaging original bricks whenever possible. If you need replacement units, you'll want to source materials that match the historic bricks' size, color, texture, and composition. Don't forget to take into account weather exposure patterns and structural loading when evaluating brick conditions. You'll also need to address any underlying causes of deterioration, such as water infiltration or foundation settlement, before proceeding with repairs to guarantee your restoration work's long-term success.
Preventive Maintenance Strategies
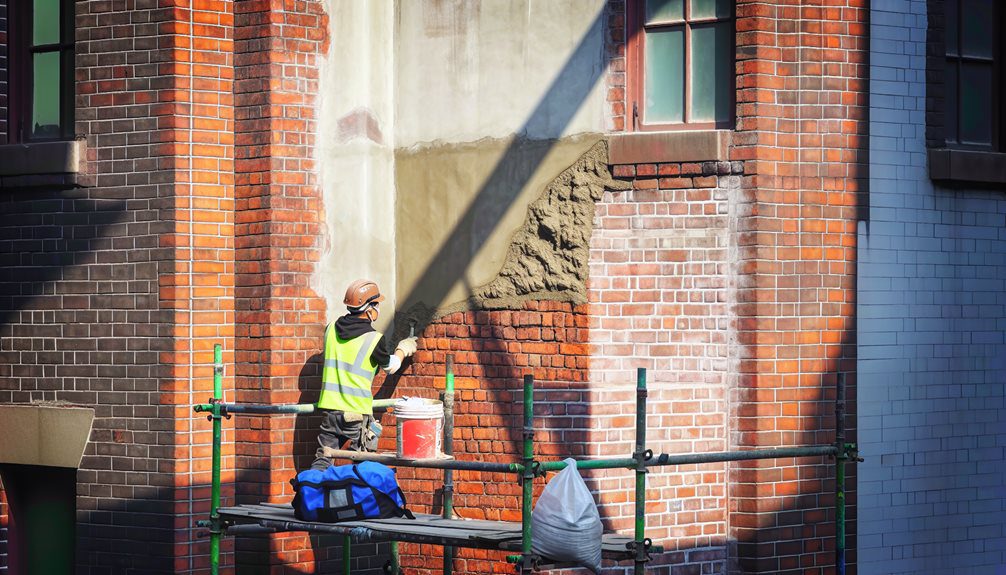
Once you've completed a historic brick restoration, implementing a robust preventive maintenance program becomes your next critical step. You'll need to establish regular preventive inspections that examine mortar joints, brick surfaces, and structural integrity at least twice annually – typically in spring and fall. These systematic evaluations help you identify potential issues before they escalate into costly repairs.
Develop detailed maintenance schedules that account for your facility's specific environmental conditions and usage patterns. You'll want to include quarterly cleaning of drainage systems, annual resealing of water-resistant coatings, and periodic tuck-pointing of deteriorating mortar joints. Document all observations and interventions in a standardized format that your maintenance team can easily access and update.
Monitor environmental factors that affect your masonry's condition, including freeze-thaw cycles, moisture levels, and chemical exposure. Install data loggers at key points to track temperature and humidity fluctuations. When you notice early signs of deterioration, such as efflorescence or hairline cracks, address them promptly. Remember, your proactive approach to maintenance preserves both the historical integrity and structural stability of your restored masonry.
Quality Control in Masonry Restoration
Quality control stands at the forefront of successful masonry restoration, requiring rigorous testing protocols and systematic documentation at every project phase. You'll need to implement thorough quality assurance measures, including material testing, mortar analysis, and structural assessments throughout your restoration project.
When you're establishing your quality control program, you'll want to align your processes with established restoration standards, such as those set by the Secretary of the Interior and ASTM International. You should regularly conduct compressive strength tests on mortar samples, verify material compatibility, and document all findings in detailed inspection reports.
Your quality control measures must include regular monitoring of environmental conditions, as temperature and humidity greatly impact masonry restoration outcomes. You'll need to maintain precise mixing ratios for mortars and make sure proper curing times are observed. It's crucial to verify that your restoration team follows historical matching techniques while meeting modern performance requirements.
Frequently Asked Questions
How Long Does a Typical Industrial Masonry Restoration Project Take to Complete?
You'll find that restoration timelines typically range from 3-6 months for standard projects, though you should anticipate that complex industrial sites might require 8-12 months. Project delays can occur due to weather conditions, material availability, or unforeseen structural issues you discover during work. You're looking at shorter timelines for localized repairs, but thorough façade restorations of your facility will need extended scheduling to guarantee proper curing periods between phases.
What Certifications Should Masonry Restoration Contractors Have for Industrial Projects?
You'll want your contractors to hold essential certification requirements, including OSHA safety certifications and Historic Masonry Certification from the Masonry Certification Program. Contractor qualifications should also include IMI (International Masonry Institute) credentials and state-specific licenses. For specialized industrial work, look for MCAA (Mason Contractors Association of America) certification. It's vital that your team's qualified professionals maintain up-to-date memberships in recognized industry organizations and complete regular continuing education programs.
Can Production Continue During Masonry Restoration Work in Industrial Facilities?
You can maintain production schedules during masonry restoration, but you'll need careful planning and coordination. You should implement strict safety protocols to isolate work areas from active production zones using containment barriers and negative air pressure systems. It's essential that you coordinate restoration activities with your facility's operational times, often scheduling intensive work during off-peak hours or planned maintenance windows. You'll want to develop a phased approach that minimizes disruption to your core operations.
What Are Typical Cost Ranges per Square Foot for Industrial Masonry Restoration?
You'll find that industrial masonry restoration costs typically range from $15 to $45 per square foot, though these figures can vary considerably based on several cost factors. Your project scope will heavily influence the final price – simple repointing might cost $10-20/sq ft, while structural repairs can exceed $60/sq ft. Consider that your facility's accessibility, material conditions, and regional labor rates will impact costs. Many of your fellow facility managers budget $25-35/sq ft as a baseline.
How Often Should Industrial Facilities Schedule Professional Masonry Inspections?
You'll want to schedule professional masonry inspections annually, though your specific inspection frequency may vary based on your facility's age and environmental exposure. It's best to conduct thorough evaluations every spring to catch masonry deterioration before it worsens. You're looking at semi-annual inspections if your building is over 50 years old or faces harsh conditions. Remember, you're protecting your investment – most of our colleagues in facility management follow this inspection timeline for ideal results.