Sustainable commercial masonry restoration combines traditional craftsmanship with eco-conscious practices. You'll need to prioritize recycled and locally sourced materials, including salvaged bricks and low-impact mortars like lime-pozzolan blends. Your waste management strategy should incorporate dedicated sorting stations and partnerships with specialized recycling facilities. Consider vapor-permeable insulation systems and environmentally friendly cleaning methods to maintain historical integrity while reducing your carbon footprint. You'll find that initial investments in sustainable materials and techniques yield significant long-term benefits, with restored structures lasting 40-50 years longer than conventional methods. The intersection of preservation and sustainability offers compelling possibilities for your next restoration project.
Environmental Impact Assessment Methods
Environmental impact assessments in masonry restoration require systematic evaluation protocols that measure both direct and indirect ecological effects. You'll need to implement extensive impact metrics that analyze material sourcing, energy consumption, waste generation, and carbon emissions throughout your restoration project. When you're examining a historic structure, these assessments become particularly vital for preserving both architectural integrity and environmental responsibility.
Your assessment frameworks should incorporate both quantitative and qualitative measures. You'll want to document baseline conditions, predict potential environmental impacts, and establish monitoring systems for your restoration work. This includes evaluating the embodied energy in traditional materials, analyzing the lifecycle costs of replacement options, and measuring the carbon footprint of your restoration methods. You're also responsible for evaluating the impact on local ecosystems, groundwater systems, and air quality during the restoration process. Additionally, implementing effective waterproofing techniques can significantly enhance the sustainability of your masonry restoration efforts.
Remember to factor in the long-term environmental benefits of restoration versus replacement. By carefully documenting these metrics, you'll demonstrate your commitment to sustainable practices while maintaining the historical significance of the structure you're restoring.
Green Material Selection
When you're selecting materials for masonry restoration, you'll find that incorporating recycled bricks from carefully deconstructed historic buildings can reduce landfill waste while maintaining period-authentic appearances. You can further minimize environmental impact by choosing alternative mortars made from lime-pozzolan blends or geopolymer compounds, which require considerably less energy to produce than Portland cement. Your stone selection should prioritize eco-certified quarries that demonstrate responsible extraction practices, maintain thorough chain-of-custody documentation, and implement site rehabilitation programs. Additionally, it's vital to consider the use of high-quality materials that ensure the durability and longevity of the restoration project.
Recycled Brick Integration
In accordance with modern sustainability principles, recycled brick integration stands as a cornerstone of responsible masonry restoration. When you're sourcing recycled bricks, you'll find that salvaged materials often carry unique patinas and weathering patterns that enhance your project's character while reducing environmental impact. Your recycled brick sourcing strategy should prioritize local demolition sites and architectural salvage yards, where you'll discover materials that match your region's historical construction methods.
You'll want to evaluate each recycled brick for structural integrity and compatibility with your existing masonry. Consider that historic bricks often possess different dimensions and compositions than modern alternatives. In your aesthetic design phase, you can leverage these variations to create distinctive patterns and textures that honor the building's heritage. You'll need to clean and prepare salvaged bricks carefully, removing old mortar without compromising their structural integrity. When you integrate these materials into your restoration project, you're not just preserving resources – you're continuing the architectural narrative of your community while maintaining the authentic character that makes historic masonry so valuable. Additionally, utilizing tuckpointing techniques during the integration process ensures a seamless blend with existing structures.
Low-Impact Mortar Alternatives
Modern masonry restoration demands thoughtful selection of low-impact mortar alternatives that reduce carbon emissions while maintaining structural integrity. You'll find that replacing traditional Portland cement-based mortars with alternatives like natural hydraulic lime (NHL) or pozzolanic mortars can reduce your project's carbon footprint by up to 50%. Through careful mortar composition analysis, you can identify the best mix that aligns with both preservation standards and environmental goals.
When selecting your mortar alternatives, consider incorporating recycled materials such as ground granulated blast furnace slag (GGBS) or fly ash. These materials enhance the environmental performance of your restoration work while providing comparable strength to traditional mortars. You'll want to evaluate the building's age and existing mortar composition to guarantee compatibility – a critical factor in historic preservation projects. Additionally, utilizing tuckpointing for mortar joint repair can further improve the longevity of your restoration efforts.
For best results, test your chosen low-impact mortar on a small section before full application. This allows you to assess workability, setting time, and color matching. Remember that factors like regional climate and exposure conditions will influence your mortar's long-term performance, so document your findings for future reference within your restoration community.
Eco-Certified Stone Sources
Building upon sustainable mortar practices, responsible stone sourcing forms the backbone of environmentally conscious masonry restoration. When you're selecting replacement stone materials, you'll want to prioritize eco-certified quarries that maintain stringent environmental standards and responsible extraction methods.
You can identify reputable eco-friendly quarries through their certification credentials, including the Natural Stone Council's sustainability certification and ISO 14001 environmental management standards. These quarries employ sustainable extraction techniques that minimize habitat disruption, reduce water consumption, and implement waste management protocols.
As you source your materials, consider working with quarries that utilize modern cutting technologies designed to maximize yield while minimizing energy consumption. You'll find that many certified suppliers now offer detailed environmental impact reports for their stone products, allowing you to track your project's carbon footprint. Additionally, prioritize regional sources when possible – you'll reduce transportation emissions while supporting local economies.
Remember to document your stone sourcing decisions for potential LEED certification points and to maintain records of chain of custody from certified quarries to demonstrate your commitment to sustainable practices.
Energy-Efficient Restoration Techniques
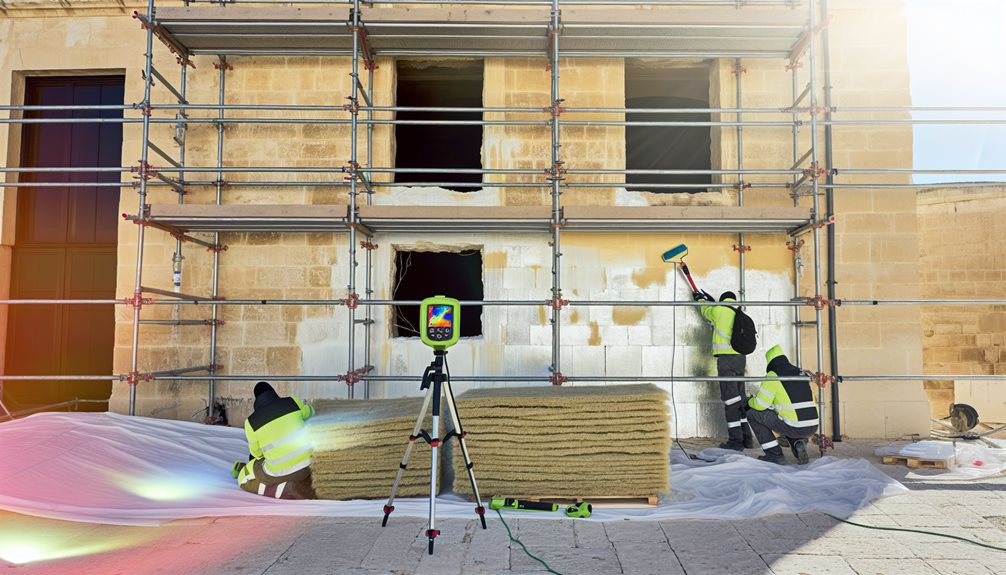
Through careful attention to thermal performance, energy-efficient masonry restoration techniques have evolved considerably since the 1970s energy crisis. You'll find that today's methods focus on maximizing a building's thermal envelope while preserving its historical integrity. Before beginning any restoration work, you'll want to conduct thorough energy audits to identify heat loss points and air infiltration issues in your masonry structure.
You can enhance your building's performance by implementing modern thermal insulation solutions that don't compromise the wall assembly's ability to breathe. When you're restoring historic masonry, you'll need to take into account compatible materials that maintain proper moisture migration while improving thermal resistance. It's essential to select vapor-permeable insulation systems that won't trap moisture within the wall cavity.
Your restoration approach should incorporate strategic repointing with thermally enhanced mortars, careful selection of replacement materials with similar thermal properties, and the installation of discrete weatherization elements. You'll achieve best results by combining traditional craftsmanship with contemporary energy-modeling tools to validate your restoration decisions, ensuring your building meets modern efficiency standards while preserving its architectural heritage. Additionally, working with experienced professionals like Gallery Arrow Masonry can provide insights into masonry restoration techniques that enhance both performance and aesthetics.
Waste Management Solutions
Conscientious waste management during masonry restoration projects typically reduces environmental impact while optimizing material recovery costs. You'll find that implementing thorough waste reduction techniques not only benefits the environment but also enhances your project's sustainability credentials and bottom line.
When you're managing restoration debris, you'll want to establish dedicated sorting stations for different materials. Separate salvageable bricks and stones from mortar debris, and you'll maximize your recycling initiatives' effectiveness. You can often repurpose cleaned historic bricks in the same project or store them for future restorations, maintaining architectural authenticity while reducing waste.
Consider partnering with specialized recycling facilities that can process your masonry waste into aggregate for new construction projects. You'll find that crushed brick and concrete can serve as sub-base material or decorative ground cover. By tracking your waste diversion rates, you're able to document your sustainability efforts and potentially qualify for green building certifications. Remember to factor in local regulations when developing your waste management plan, as many jurisdictions now require specific diversion rates for construction and demolition debris. Additionally, working with a certified, licensed, insured, and bonded contractor like Chicagoland Tuckpointing And Masonry Restoration ensures that your projects adhere to best practices in sustainability.
Traditional Vs Sustainable Practices
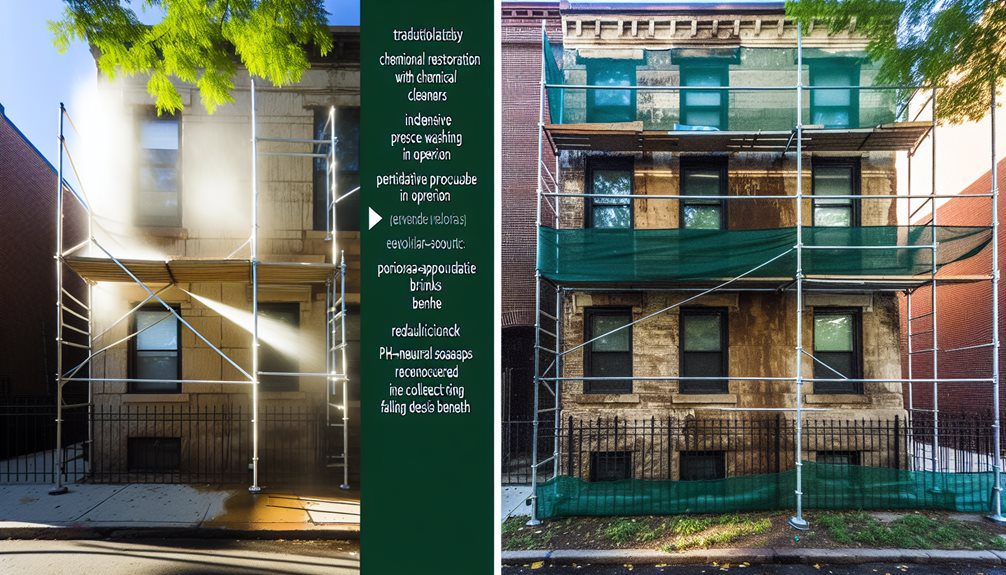
In contrast to traditional masonry methods that often prioritize immediate cost savings over environmental impact, today's sustainable restoration practices emphasize long-term durability and ecological responsibility. You'll notice that traditional methods typically rely on harsh chemical cleaners, non-recyclable materials, and energy-intensive processes that can damage both the historic fabric and the environment.
When you're comparing approaches, sustainable methods incorporate low-VOC cleaning agents, locally sourced materials, and energy-efficient techniques that preserve the building's integrity while reducing your carbon footprint. Traditional methods might use Portland cement-based mortars that are too rigid for historic structures, while sustainable practices favor lime-based mortars that allow masonry to breathe and flex naturally.
You'll find that sustainable methods also prioritize material salvage and reuse, unlike traditional practices that often default to replacement. By choosing sustainable restoration, you're not only preserving architectural heritage but also joining a community of practitioners who understand that responsible stewardship means balancing preservation needs with environmental concerns. These methods may require higher initial investments but deliver superior long-term results and reduced lifecycle costs. Additionally, many commercial masonry restoration companies, such as those in Orland Park, are increasingly adopting these sustainable practices to enhance their service offerings.
Local Sourcing Benefits
When you source your masonry materials locally, you'll greatly reduce the project's carbon footprint by minimizing transportation distances and fuel consumption. Your commitment to regional material markets helps preserve traditional quarrying operations and maintains the availability of geologically matched stones for future restoration projects. By investing in local materials, you're directly contributing to your community's economic importance while ensuring architectural authenticity through the use of regionally appropriate building materials. Additionally, this approach aligns with our commitment to high-quality materials and craftsmanship, ensuring that every project meets the standards of commercial masonry restoration.
Reduced Transportation Carbon Footprint
Local material sourcing stands as a cornerstone of sustainable masonry restoration, greatly reducing the project's carbon footprint through minimized transportation distances. When you're sourcing materials locally, you'll considerably decrease the fuel consumption and emissions associated with long-distance transportation logistics. This reduction can often translate to a 40-60% decrease in transportation-related carbon emissions compared to materials shipped from distant locations.
You'll find that implementing local sourcing strategies creates a ripple effect throughout your project's sustainability profile. By reducing the distance between quarries or salvage sites and your restoration project, you're naturally participating in carbon offsetting without additional investment. The environmental impact becomes even more pronounced when you consider that traditional masonry materials like stone and brick typically weigh several tons per shipment.
To maximize these benefits, you'll want to map out material sources within a 100-mile radius of your project site. This approach not only reduces your carbon footprint but also supports regional economies and preserves the architectural authenticity of your restoration work, as local materials often match the original building materials more accurately. Additionally, utilizing high-quality materials ensures the longevity and durability of the restoration, further enhancing sustainability.
Supporting Regional Material Markets
Beyond the environmental advantages of reduced transportation, regional material sourcing strengthens the economic fabric of local masonry industries. When you choose locally sourced materials for your restoration projects, you're investing in the preservation of traditional craftsmanship and supporting multi-generational quarries and fabrication facilities within your region. Regional sourcing guarantees material availability that's historically appropriate for your area's architectural heritage. You'll find that local suppliers often maintain inventories of stones and bricks that match the distinct characteristics of your region's historic buildings. This compatibility extends beyond mere aesthetics – locally sourced materials typically share similar weathering properties and durability characteristics with the original materials used in historic structures. Additionally, using high-quality materials in restoration projects ensures long-lasting results and enhances overall structural integrity.
Community Economic Growth Benefits
Through strategic local sourcing, masonry restoration projects create ripple effects of economic significance within communities. When you choose to work with local suppliers, craftspeople, and materials, you're fostering community investment that extends far beyond the immediate restoration project. Your decisions help sustain multi-generational masonry businesses, support specialized training programs, and maintain the cultural heritage of traditional building trades.
You'll find that local sourcing directly contributes to job creation across various skill levels. From quarry workers and stone cutters to skilled masons and project managers, each restoration project helps maintain a skilled workforce within your community. These positions often provide stable, well-paying opportunities that support families and encourage apprenticeship programs. Furthermore, when you source materials locally, you're helping to preserve regional architectural characteristics while stimulating the growth of supporting industries like transportation, equipment rental, and material processing facilities.
Water Conservation Strategies
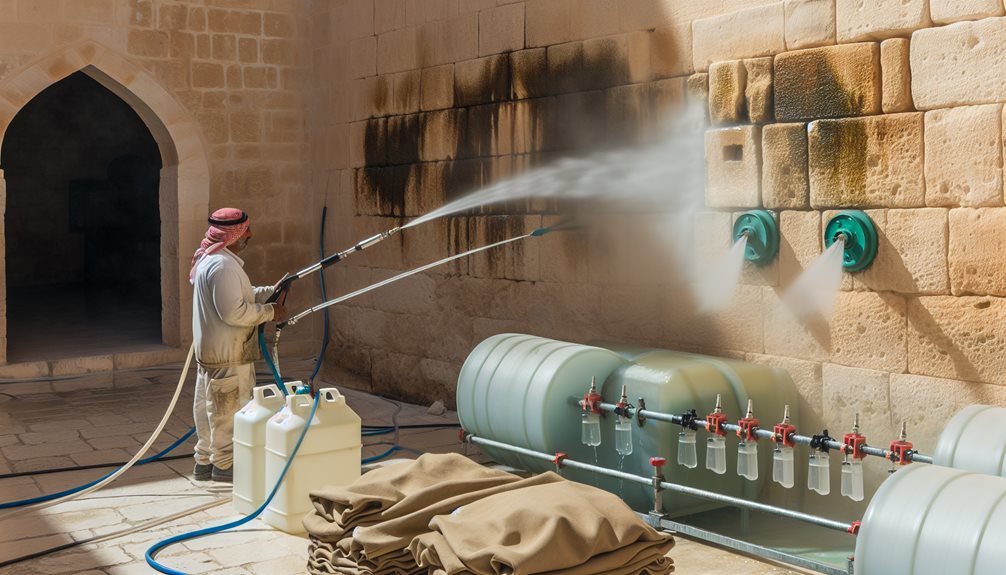
Effective water management stands at the forefront of sustainable masonry restoration, where every drop counts toward both conservation and project efficiency. You'll find that implementing extensive water conservation strategies not only reduces your environmental impact but also considerably cuts operational costs.
Start by integrating rainwater harvesting systems into your restoration project. You can collect runoff from scaffolding covers and temporary roofing, storing it in designated tanks for reuse in mixing mortars and cleaning applications. When you're pressure washing historic facades, you'll want to install reclamation systems that filter and recycle water throughout the cleaning process.
Your irrigation optimization should focus on precise moisture control during the curing phase. You'll need to install moisture meters and automated misting systems that deliver exactly what your masonry needs – no more, no less. Consider incorporating time-based controllers and soil moisture sensors to regulate water distribution efficiently. By implementing these systems, you're joining a community of restoration professionals who understand that water conservation isn't just about sustainability – it's about preserving our architectural heritage while protecting our natural resources.
Life Cycle Cost Analysis
Life cycle cost analysis enables you to evaluate the true financial impact of your masonry restoration project beyond the initial investment, tracking expenses from installation through maintenance and eventual replacement. You'll find that sustainable masonry practices, while potentially costlier upfront, typically yield significant savings through reduced maintenance needs, lower energy costs, and extended material longevity over 50-100 year periods. Your analysis should incorporate both tangible factors like material durability and labor costs, as well as intangible benefits such as historical preservation value and environmental impact reduction.
Cost-Benefit Over Time
When evaluating sustainable masonry restoration projects, an extensive cost-benefit analysis reveals significant long-term advantages over conventional methods. You'll find that initial investments in high-quality, sustainable materials and skilled craftsmanship typically result in substantial cost savings over the structure's lifetime. While traditional repairs might seem less expensive upfront, they often require more frequent maintenance and earlier replacement.
The longevity benefits of sustainable restoration become apparent within the first decade. You're likely to see a 20-30% reduction in maintenance costs when you've invested in materials like natural hydraulic lime mortars and locally sourced stone. These materials aren't just environmentally responsible; they're also more compatible with historic masonry, reducing the risk of accelerated deterioration that's common with modern cement-based repairs.
Your investment in sustainable practices will yield measurable returns through reduced energy costs, extended material lifespan, and enhanced property value. By analyzing performance data from restored buildings, you'll notice that structures implementing sustainable masonry techniques typically maintain their structural integrity for 40-50 years longer than those restored using conventional methods, making the higher initial cost a sound financial decision.
Long-Term Investment Strategies
Strategic planning for masonry restoration requires thorough life cycle cost analysis (LCCA) across multiple decades. You'll need to evaluate initial capital expenditures against projected investment returns, incorporating variables like material durability, maintenance intervals, and energy performance improvements. When you factor in sustainable financing options, including historic preservation tax credits and energy efficiency incentives, you're creating a detailed investment framework that spans 30-50 years.
To enhance your LCCA, you'll want to take into account both direct and indirect cost factors. Direct costs include materials, labor, and equipment, while indirect benefits encompass reduced energy consumption, increased property value, and enhanced building longevity. You'll find that traditional materials often outperform modern substitutes when calculating total ownership costs over extended periods.
Your investment strategy should account for periodic maintenance cycles, typically occurring every 5-7 years for minor repairs and 15-20 years for major interventions. By establishing a dedicated maintenance fund and leveraging sustainable financing mechanisms, you're protecting both the building's historical integrity and your financial interests. This approach guarantees ideal resource allocation while maintaining the structure's cultural and economic value.
Historical Preservation Meets Sustainability
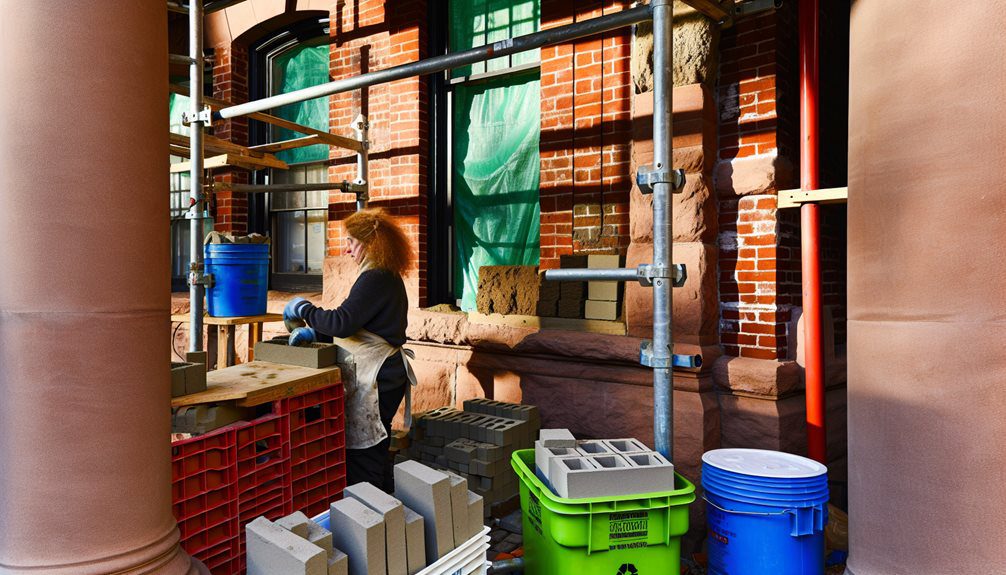
Modern preservation of historic masonry structures presents a delicate balance between maintaining architectural authenticity and implementing sustainable solutions. When you're working on heritage conservation projects, you'll find that sustainable practices often align naturally with traditional building methods, as both emphasize durability and local material sourcing.
You'll want to explore adaptive reuse strategies that preserve original masonry features while upgrading systems for energy efficiency. This means you can retain period-specific brick patterns and mortar joints while incorporating modern insulation techniques and moisture management systems. By focusing on reversible interventions, you're ensuring that future conservators can adapt the structure as preservation technologies advance.
As a preservation professional, you'll discover that traditional lime mortars offer superior breathability compared to modern cement, making them both historically accurate and environmentally sound. You can maximize sustainability by salvaging original materials, sourcing local replacements, and utilizing low-impact cleaning methods. When you integrate these approaches, you're not just preserving history – you're creating a bridge between past craftsmanship and future environmental stewardship, ensuring these structures remain viable for generations to come.
Future-Proof Restoration Planning
Every successful masonry restoration project demands a forward-thinking framework that anticipates decades of structural evolution and climate impacts. You'll need to develop extensive strategies that account for both immediate repairs and long-term adaptive reuse possibilities, ensuring your restored structures remain viable for generations.
When you're creating your resilience planning protocol, you'll want to analyze potential climate stressors, from increased precipitation to extreme temperature fluctuations. Consider incorporating moisture monitoring systems and selecting materials that can withstand these evolving conditions. It's essential to document your restoration decisions meticulously, creating a detailed record that future preservationists can reference.
You should evaluate your building's potential for multiple use scenarios, as adaptive reuse often becomes necessary over time. This means designing flexible solutions that don't compromise historical integrity while allowing for future modifications. Factor in emerging technologies and restoration techniques that might become available, leaving room in your documentation for updates and adaptations. Remember to specify materials that are both historically appropriate and environmentally sustainable, as you're not just preserving the past – you're safeguarding these structures for future generations.
Frequently Asked Questions
How Long Does Sustainable Masonry Restoration Typically Take Compared to Conventional Methods?
You'll find that sustainable masonry restoration often takes 15-25% longer than conventional methods due to careful material sourcing and specialized techniques. Duration comparison varies based on efficiency factors like weather conditions, material availability, and crew expertise. However, you're investing in longevity – these methods typically last 30-40% longer than standard repairs. While the initial timeline extends, you're gaining superior durability and reduced maintenance cycles in your historic structure.
What Certifications Should Contractors Have for Sustainable Masonry Restoration Projects?
You'll want your contractors to hold LEED (Leadership in Energy and Environmental Design) certification as a primary credential. Look for additional Green Certifications like BREEAM or Living Building Challenge. Make certain they're certified in handling Eco Friendly Materials through programs like GreenGuard or Cradle to Cradle. Don't forget local historic preservation certifications, especially in heritage districts. Consider contractors with memberships in sustainable building organizations like the Green Building Initiative.
Are Sustainable Restoration Materials More Susceptible to Weather Damage Over Time?
You'll find that modern sustainable materials often match or exceed traditional options in weather resilience. When you're selecting eco-friendly mortars and sealants, you're actually getting advanced formulations that integrate natural minerals and recycled content while maintaining durability. They're engineered to withstand freeze-thaw cycles, UV exposure, and moisture fluctuations. Your sustainable choice won't compromise longevity – many green materials now come with performance warranties comparable to conventional products.
Can Historic Tax Credits Be Applied to Sustainable Masonry Restoration Projects?
Yes, you'll find that historic tax credits can often apply to your masonry restoration project, provided your building meets tax credit eligibility requirements. You'll need to guarantee your property is listed on the National Register of Historic Places or contributes to a historic district. While pursuing project funding, you'll want to work with a qualified preservation architect who can help document that your sustainable materials and methods meet the Secretary of Interior's Standards for Rehabilitation.
What Maintenance Schedule Should Be Followed After Sustainable Masonry Restoration?
You'll need to implement a preventive maintenance schedule right after your restoration work is complete. Plan for annual inspections in spring and fall, focusing on moisture issues and joint integrity. Your restoration frequency typically spans 15-20 years for major work, but you should conduct minor repairs every 3-5 years. Remember, you're preserving history, so don't skip quarterly cleaning and documentation. Join fellow property stewards by keeping detailed maintenance logs of all interventions.