To effectively repair and restore stone architectural elements, you'll need to first identify the type of damage through visual inspection and documentation. Common issues include mechanical damage, erosion, chemical deterioration, and biological growth. Start with proper cleaning using pH-neutral solutions or mechanical methods like micro-abrasive blasting, then address structural repairs using compatible materials and techniques. You'll want to guarantee replacement stones match the original's color, texture, and physical properties. Follow up with preventive measures like water penetration control and regular maintenance. Modern technologies like 3D scanning and non-destructive testing can enhance your restoration project's success and longevity.
Common Types of Stone Damage
Identifying stone damage early is essential for preserving architectural elements. When you're evaluating your building's stone features, you'll encounter several distinct types of deterioration that require different restoration techniques.
Mechanical damage presents itself through cracks, spalls, and chips, often resulting from freeze-thaw cycles or structural stress. You'll notice these issues particularly at joints and corners where stone weathering effects are most pronounced. Erosion, another common concern, manifests as a gradual loss of surface detail, especially in areas exposed to wind and rain.
Chemical deterioration occurs when your stone reacts with pollutants or acidic precipitation. You'll see this in the form of crusting, staining, or material dissolution. Salt crystallization can cause significant damage as well, creating a white efflorescence on surfaces and subsurface decomposition.
Biological growth, including algae, moss, and lichens, can penetrate stone surfaces and accelerate deterioration. You'll typically find these organisms in shaded, damp areas. Additionally, you might encounter previous repairs that have failed, such as inappropriate patching materials or mismatched mortar joints, which can lead to accelerated degradation of the surrounding stone.
Assessment and Documentation Methods
Thorough documentation forms the foundation of any stone preservation project. You'll need to employ systematic visual inspection techniques to properly assess the condition of stone elements and create detailed records of damage patterns, previous repairs, and areas of concern. Start by mapping visible defects on scaled drawings or photographs, noting the location and extent of each issue.
You'll want to incorporate digital documentation tools into your assessment process. Use high-resolution photography to capture detailed images of deterioration, and consider employing 3D scanning technology to create precise digital models of complex architectural elements. These tools will help you maintain accurate records and track changes over time.
Document environmental factors that may affect the stone, including exposure to weather, drainage patterns, and nearby mechanical systems. You should measure and record moisture levels, salt content, and surface temperatures at various points. Create condition reports that include detailed descriptions of materials, architectural features, and previous intervention history. Don't forget to note the stone type, tooling marks, and original construction methods, as these details will inform your restoration approach and help you select appropriate repair techniques.
Stone Cleaning Techniques
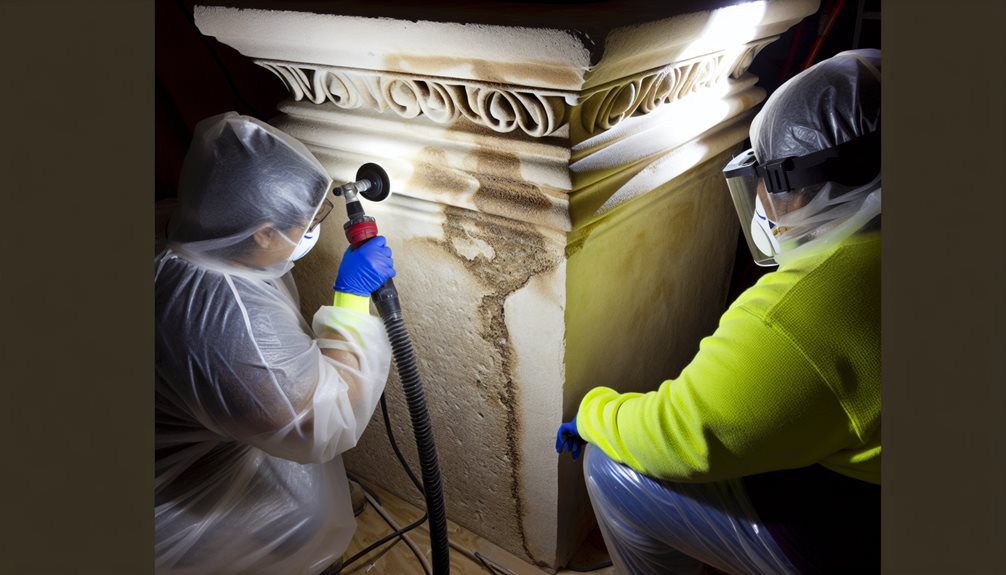
When you're cleaning historic stone architectural elements, you'll need to contemplate three primary approaches: mechanical cleaning methods, chemical solutions, and high-pressure steam applications. Your selection of mechanical techniques might include micro-abrasive blasting, brushing, or laser cleaning, while chemical solutions range from mild detergents to specialized poultices designed for specific stone types. High-pressure steam cleaning offers an effective intermediate option that's particularly useful when you're working with deeply embedded soiling that's resistant to gentler methods but requires minimal chemical intervention.
Mechanical Cleaning Methods
Mechanical cleaning represents a fundamental approach to removing surface deposits and contaminants from stone architectural elements. When you're working with historic or delicate stonework, you'll need to carefully select abrasive techniques that won't compromise the material's integrity. You'll find that controlling the pressure and distance of cleaning equipment is vital for achieving the best results while maintaining surface protection.
Before beginning any mechanical cleaning, you'll want to test your chosen method on a small, inconspicuous area. Start with the gentlest approach possible, such as soft bristle brushes or low-pressure air, before progressing to more aggressive techniques. You'll need to take into account factors like the stone's composition, weathering patterns, and existing damage when selecting your cleaning method.
For stubborn deposits, you can employ micro-abrasive cleaning systems using fine particles like glass beads or walnut shells. It's essential that you maintain consistent pressure and movement patterns to avoid creating uneven surfaces. Remember to always wear appropriate protective equipment and maintain proper ventilation when using any mechanical cleaning systems.
Chemical Cleaning Solutions
Chemical cleaning solutions provide targeted treatment for removing complex stains, biological growth, and mineral deposits from stone surfaces that mechanical methods alone cannot address. You'll find that pH neutral cleaners offer the safest approach for most stone types, preventing etching or surface damage while effectively dissolving contaminants. When selecting cleaners, you'll want to start with the mildest solution possible and gradually increase strength only if necessary.
Before applying any chemical cleaner, you'll need to perform a small test patch in an inconspicuous area to verify compatibility with your stone surface. It's crucial to use eco-friendly solutions whenever possible, as these products protect both the environment and the building's occupants. You'll discover that many modern green cleaners are just as effective as traditional chemicals but pose fewer risks.
When applying chemical cleaners, you'll need to follow specific dwell times, usually between 5-15 minutes, depending on the product and stain type. Always rinse thoroughly with clean water to neutralize the cleaning agents and prevent residue buildup that could attract future soiling.
High-Pressure Steam Applications
Building upon chemical treatments, high-pressure steam cleaning offers a powerful yet controlled method for removing stubborn deposits from stone surfaces. You'll find this technique particularly effective when you're dealing with deeply embedded grime, biological growth, or residual staining that's resistant to conventional cleaning methods.
When you're applying high-pressure steam, you'll need to maintain strict temperature and pressure controls. Start with a pressure setting of 80-100 PSI and gradually increase it based on the stone's condition and hardness. You'll notice the application benefits immediately as the steam penetrates deep into the stone's pores, loosening contaminants without causing physical damage to the surface.
As you work with the steam equipment, you'll want to keep the nozzle moving constantly to prevent overheating any single area. Position your steam wand at a 45-degree angle and maintain a consistent distance of 6-8 inches from the surface. If you're working with delicate ornamental details, you'll need to reduce both pressure and temperature while increasing your working distance to protect intricate carvings and historical features.
Structural Repair Best Practices
Three fundamental principles guide all structural repairs of stone architectural elements: proper load distribution, material compatibility, and minimal intervention. When you're addressing structural issues, you'll need to assess load paths and guarantee your repairs maintain or enhance the building's structural integrity.
To achieve successful crack stabilization, you'll want to begin with non-destructive testing to determine the extent of damage. You'll find that most structural cracks require a combination of epoxy injection and mechanical pinning. It's essential that you select materials that match the original stone's mechanical properties to prevent future stress concentrations.
For joint reinforcement, you'll need to follow industry-standard specifications for both horizontal and vertical joints. You should remove deteriorated mortar to a depth of 2.5 times the joint width, then install appropriate reinforcement materials. When you're retrofitting structural elements, always document existing conditions and monitor repair performance over time.
Remember to coordinate with structural engineers before undertaking major repairs, and guarantee your intervention methods don't compromise the building's historical integrity. Additionally, regular inspections will help identify common masonry issues early on, allowing for timely restoration and maintenance. Your repair strategy should include regular inspection schedules and maintenance protocols to protect your investment.
Material Selection and Matching
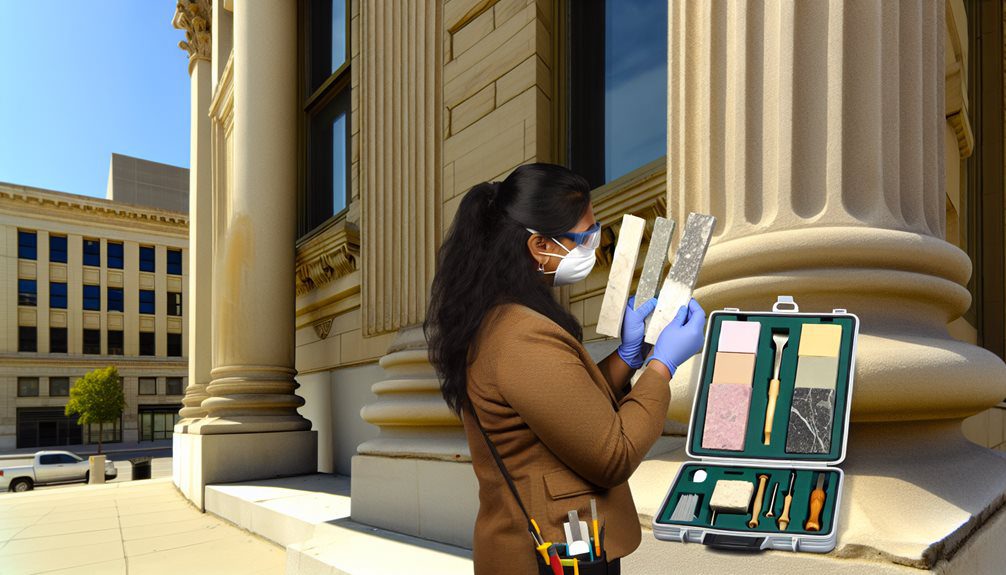
When selecting replacement stone for architectural repairs, you'll need to conduct thorough physical properties testing of both the original and proposed materials to guarantee structural compatibility. You must identify the historical stone's composition, weathering characteristics, and mechanical properties through petrographic analysis and laboratory testing. Your replacement material should match not only the original stone's physical attributes but also its visual characteristics, including color variations, grain patterns, and surface textures.
Physical Properties Assessment
Proper assessment of physical properties stands as the foundation for successful stone repair and restoration projects. You'll need to evaluate multiple characteristics to guarantee your restoration materials align with the existing stonework. Begin with physical testing of both the original stone and potential replacement materials, focusing on compression strength, porosity, and water absorption rates.
When you're conducting durability evaluation, you'll want to assess weathering resistance, thermal expansion coefficients, and frost resistance. These factors directly impact how well your repairs will integrate with the existing structure and perform over time. It is crucial to understand that even minor variations in physical properties can lead to significant compatibility issues.
You'll find that testing laboratories can provide standardized ASTM analysis for:
- Bulk density and specific gravity
- Salt crystallization resistance
- Flexural strength
- Abrasion resistance
- Thermal cycling behavior
Document all test results systematically, as you'll need this data to make informed decisions about material selection and application methods. Remember that your goal is to match not just appearance, but also the fundamental physical characteristics that will secure long-term structural integrity and performance. Additionally, considering the application of waterproofing techniques can further enhance the longevity of your stone restorations.
Historical Stone Identification
Building upon the physical assessment data, accurate historical stone identification serves as the next critical step in your restoration process. You'll need to establish the historical context of your building's original construction, including documentation of quarry sources, architectural specifications, and period-specific building practices. This research forms the foundation for matching replacement materials.
To identify your building's stone type, you'll want to analyze archived building records, historical photographs, and original architectural drawings. Cross-reference these with known stone varieties used during your building's construction period. You'll find that many historical buildings used locally quarried materials, so investigating regional geology and historical quarrying operations can provide valuable insights.
When you're determining stone sourcing options, consider both active quarries that might supply matching stone and salvaged materials from contemporary buildings. You'll need to collect samples of potential matches and compare their mineral composition, color variations, and weathering characteristics to your existing stonework. Remember that even if you can't locate the original quarry, you can often find acceptable substitutes that maintain historical authenticity while meeting modern performance requirements.
Color and Texture Compatibility
Matching replacement stone to existing architectural elements requires meticulous analysis of both color and textural characteristics. You'll need to evaluate the original stone's base color, undertones, and surface variations to guarantee seamless integration. When performing color matching, it is crucial to assess the stone under different lighting conditions, as natural and artificial light can greatly affect its appearance.
For accurate texture analysis, you'll want to examine both macro and micro features of the existing stone. Consider factors such as grain size, surface roughness, and weathering patterns. You can use digital imaging and surface profiling tools to document these characteristics precisely. Remember that your replacement stone should exhibit similar porosity and mineral composition to maintain consistent weathering patterns over time.
When you've identified potential replacement stones, create sample panels for side-by-side comparison. You'll need to evaluate these samples in wet and dry conditions, as moisture can dramatically affect stone appearance. Consider creating a color and texture reference guide for your specific project, documenting acceptable ranges for variations in both characteristics to maintain consistency throughout the restoration process.
Historic Preservation Guidelines
When undertaking repairs on historic stone elements, strict adherence to preservation guidelines guarantees architectural authenticity and structural integrity. You'll need to consult your local preservation board and follow established protocols that protect the building's historic significance. These guidelines typically require you to document existing conditions, maintain original materials whenever possible, and use restoration methods that don't compromise preservation ethics.
Before beginning any work, you must submit detailed restoration plans for approval, including your proposed materials and techniques. You'll find that most preservation guidelines require you to use the gentlest cleaning methods first and avoid harsh chemicals that could damage historic stone surfaces. They'll also specify that any replacement materials must match the original in composition, color, and texture.
You're required to maintain detailed records of all restoration work, including photographs, material specifications, and treatment methods. Remember that you can't make any structural modifications without explicit approval, and you must preserve distinctive features that characterize the building's architectural style. When in doubt, consult with preservation specialists who understand local regulations and historical construction methods. Additionally, ensuring that masonry restoration is performed correctly can further enhance structural integrity and longevity.
Preventive Maintenance Strategies
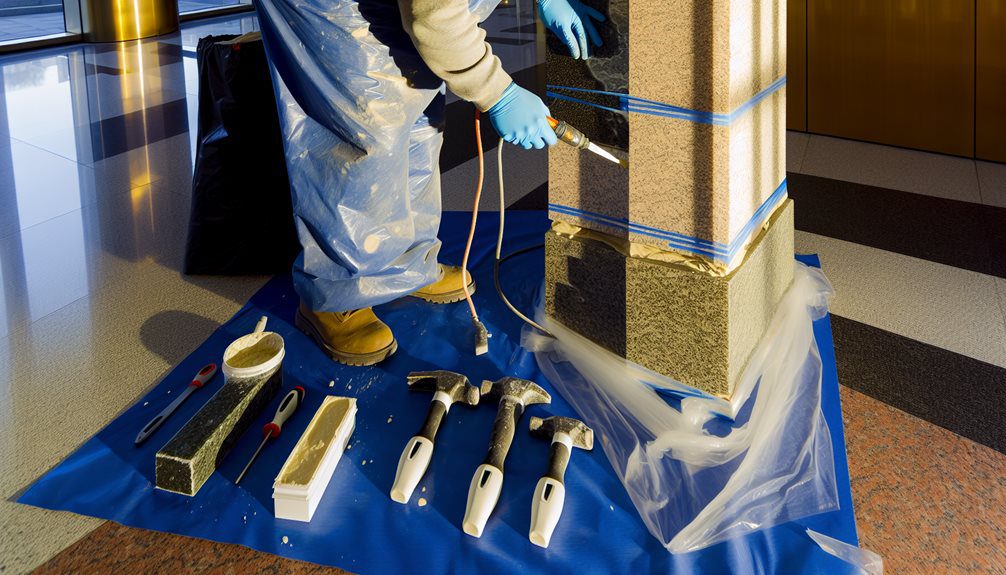
Regular inspections form the foundation of effective stone preservation, requiring you to establish a systematic maintenance schedule that prevents minor issues from escalating into major structural problems. You'll need to conduct preventive inspections at least twice yearly, focusing on areas where water penetration commonly occurs, such as joints, copings, and window surrounds.
As part of your maintenance schedules, you'll want to document all observations thoroughly, tracking changes in the stone's condition over time. This includes photographing problem areas and maintaining detailed records of previous repairs. You should clean your stone surfaces annually using appropriate pH-neutral cleaners, and you'll need to repoint deteriorating mortar joints before water infiltration causes extensive damage.
You'll also need to verify proper drainage systems are functioning correctly by cleaning gutters and downspouts regularly. It's crucial to address any biological growth immediately, as lichens and moss can trap moisture against stone surfaces. When you're implementing these preventive measures, you'll want to coordinate with other building maintenance activities to optimize efficiency and reduce disruption to occupants. Remember to adjust your maintenance schedule based on your building's specific exposure conditions and local climate patterns. Additionally, consider conducting energy efficiency audits to identify flaws that may lead to heat loss and further deterioration of stone elements.
Modern Restoration Technologies
Advanced restoration technologies have revolutionized stone architectural preservation, offering you precise methods for diagnosing and treating deterioration. You'll find that laser scanning and photogrammetry now enable you to create detailed 3D models of damaged elements, helping you plan repairs with unprecedented accuracy. These advanced restoration techniques allow you to identify structural issues that weren't visible to the naked eye.
You can now employ innovative material applications like nano-lime consolidants and mineral-based mortars that are specially formulated to match your building's historical materials. These solutions don't just repair the stone; they integrate seamlessly with existing structures while providing superior durability. You'll also benefit from non-destructive testing methods, including ultrasonic pulse velocity testing and infrared thermography, which help you assess damage without compromising the stone's integrity. Additionally, regular inspections of stone facades are crucial to ensure ongoing maintenance and protection from potential issues.
Digital monitoring systems let you track your restoration project's progress and the building's response to treatments in real-time. When you combine these technologies with traditional craftsmanship, you're able to achieve results that honor the building's heritage while ensuring its longevity through modern scientific approaches.
Frequently Asked Questions
How Long Does a Typical Stone Restoration Project Usually Take?
Your stone restoration project timeline can vary considerably based on several factors you'll need to take into account. For small repairs, you're looking at 2-4 weeks, while extensive restorations might take 3-6 months. Your choice of restoration techniques will impact duration – chemical cleaning is quicker than mechanical methods, and patching requires less time than full stone replacement. Weather conditions and material availability will also affect how long you'll need to complete the work.
What Certifications Should Stone Restoration Contractors Have?
When selecting a stone restoration contractor, you'll want to verify they hold key certification requirements from organizations like the Natural Stone Institute (NSI) or Building Stone Institute (BSI). Look for their Accredited Commercial Contractor credentials and guarantee they've completed specific training in stone restoration. You should also confirm they've obtained general contractor licenses, OSHA safety certifications, and liability insurance. Many top contractors will have earned additional specialized masonry qualifications.
Can Stone Elements Be Restored During Winter Months?
You can perform stone restoration during winter months, but you'll need to account for specific winter challenges. Temperature control is essential – you'll want to maintain worksite temperatures above 40°F (4°C) using temporary enclosures and heating systems. Your restoration techniques must adapt to cold weather conditions, including using specialized cold-weather mortars and sealants. Water-based treatments aren't recommended when freezing is possible, so you'll need to schedule these components strategically or opt for cold-weather alternatives.
How Often Should Building Owners Schedule Professional Stone Inspections?
You'll want to schedule professional stone inspections at least annually, though bi-annual checks are ideal for preferable stone maintenance frequency. Your inspection checklist should include assessment of joints, surface degradation, and structural integrity. If you're managing properties in harsh climates or high-traffic areas, you'd benefit from quarterly inspections. Don't forget to coordinate these evaluations with your building's overall maintenance schedule to stay ahead of potential issues.
What Insurance Coverage Is Needed for Stone Restoration Work?
You'll need extensive liability coverage that specifically includes masonry and façade work. It's crucial to secure project insurance that covers both property damage and worker injuries during restoration. Make sure your contractor carries their own insurance with adequate limits, typically $1-2 million per occurrence. You should also verify that any subcontractors are properly insured and request certificates of insurance before work begins.