Protect your commercial property's masonry through strategic seasonal maintenance. In spring, inspect for winter damage and repair mortar joints. During summer, shield surfaces from heat damage and monitor irrigation near foundations. Fall preparations should include clearing debris, sealing vulnerable areas, and scheduling tuckpointing repairs. Winter requires vigilant monitoring of moisture levels and freeze-thaw cycles. You'll need to conduct quarterly inspections, maintain proper drainage systems, and apply protective sealants during ideal weather conditions. Professional assessments twice yearly will help identify structural issues before they escalate. Understanding these seasonal protocols is your first step toward extending your building's lifespan by up to 40 years.
Spring Cleaning and Inspection Protocol
The arrival of spring presents the ideal time to implement a thorough masonry inspection and cleaning protocol for your commercial property. As temperatures stabilize and winter's harsh conditions subside, you'll want to conduct detailed spring inspections that identify any damage or deterioration to your masonry surfaces.
Begin by creating an extensive cleaning checklist that addresses all masonry components. You'll need to examine mortar joints for signs of cracking, spalling, or deterioration. Check for efflorescence – those white, crystalline deposits that indicate moisture problems. Don't forget to inspect your building's foundation walls, brick facades, and any decorative stonework for structural issues.
Next, assess your drainage systems, including downspouts and gutters, to verify they're directing water away from masonry surfaces properly. You'll want to clean all masonry surfaces using appropriate methods and materials specific to your building's construction. Remove any vegetation growth, particularly in joints or cracks, as these can lead to structural compromise. Additionally, consider professional tuckpointing services to address any significant mortar joint wear. Document all findings and necessary repairs, prioritizing issues that could impact structural integrity or lead to water infiltration. This systematic approach guarantees you're maintaining your property's value while preventing costly future repairs.
Summer Heat Protection Strategies
Durability of masonry structures faces significant challenges during peak summer temperatures, requiring proactive protection measures from commercial property owners. You'll need to implement targeted strategies to protect your building's masonry from sun damage and heat-related deterioration.
Start by applying heat reflective materials to exposed masonry surfaces, particularly those receiving direct sunlight throughout the day. These specialized coatings create a protective barrier that reduces thermal absorption and prevents excessive expansion of your masonry units. You'll want to focus on south and west-facing walls, which typically experience the most intense sun exposure.
For sun damage prevention, install appropriate shading devices or architectural elements where feasible. Consider temporary scaffolding covers during extreme heat waves, especially if you're planning renovation work. You should also monitor your building's irrigation systems to maintain consistent moisture levels in the soil surrounding foundation walls, as extreme heat can cause soil shrinkage and subsequent structural stress.
Don't forget to check your expansion joints regularly during summer months. Verify they're properly sealed and can accommodate thermal movement without compromising the integrity of your masonry system. Replace any deteriorated sealants promptly to maintain effective protection against heat-related stress. Additionally, consider applying a siloxane clearcoat to enhance moisture resistance and protect against thermal fluctuations.
Winter Weather Defense Measures
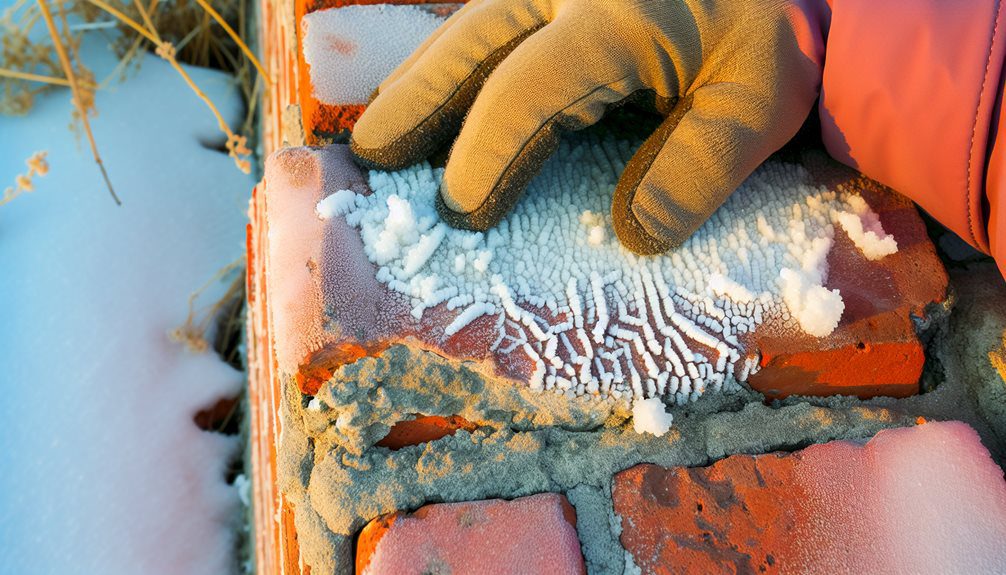
Before winter's harsh conditions arrive, you'll need to thoroughly inspect and seal all surface cracks in your masonry to prevent moisture infiltration and structural damage. You should apply specialized waterproof coatings to your masonry surfaces, ensuring complete coverage of vulnerable areas like joints and connections. Your maintenance team must regularly monitor freeze-thaw cycles throughout the winter season, as these temperature fluctuations can cause existing cracks to expand and new ones to form in untreated masonry. Additionally, consider scheduling tuckpointing for joints to maintain the integrity of your masonry before the winter weather sets in.
Seal All Surface Cracks
Surface cracks in masonry walls can quickly deteriorate into major structural issues during winter's freeze-thaw cycles. When water penetrates these openings and freezes, it expands and widens the cracks, creating a destructive cycle that compromises your building's integrity. You'll need to address these vulnerabilities before winter arrives.
Start by conducting a thorough inspection of your masonry surfaces, paying special attention to areas around windows, doors, and joints. You'll want to identify and mark all visible cracks, no matter how small they appear. Professional crack sealing should be performed using appropriate materials that match your masonry's composition and movement capabilities.
For hairline cracks, you'll need elastomeric sealants that can accommodate thermal movement. Larger surface repairs may require specialized mortar compounds or epoxy-based fillers. Don't overlook the importance of proper surface preparation – all cracks must be cleaned, dried, and free of loose debris before applying sealants. Your repair materials should be compatible with the existing masonry and weather-resistant. Consider scheduling annual inspections to catch and address new cracks before they develop into costly structural problems that could affect your entire building system. Additionally, consulting with a professional masonry restoration service can provide expertise on masonry restoration services to ensure proper repairs are made.
Apply Waterproof Coatings Now
While sealing cracks provides targeted protection, an all-encompassing waterproof coating system creates an additional defensive barrier against winter moisture infiltration. You'll want to apply these protective coatings before temperatures drop below 50°F to guarantee proper adhesion and curing. The waterproof benefits extend beyond basic moisture resistance, helping prevent freeze-thaw damage and reducing long-term maintenance costs.
For peak coating application, you'll need to thoroughly clean and prepare all masonry surfaces, removing any efflorescence, dirt, or deteriorated previous coatings. Select a penetrating sealer for vertical surfaces and a film-forming coating for horizontal areas where ponding might occur. Today's advanced formulations offer breathability while maintaining a strong moisture barrier.
Remember to test the coating on a small, inconspicuous area first to verify compatibility and desired appearance. Apply the product in thin, even layers, following manufacturer specifications for coverage rates and drying times between coats. You'll typically need two coats for complete protection, with special attention to joints, changes, and areas prone to water accumulation. This systematic approach guarantees your building's masonry remains protected throughout the harsh winter months. Additionally, consulting with a certified masonry professional can ensure optimal application and longevity of your waterproofing efforts.
Monitor Freeze-Thaw Impact
Understanding freeze-thaw cycles demands vigilant monitoring throughout winter months, as temperature fluctuations can severely impact masonry integrity. You'll need to regularly inspect your commercial property's masonry surfaces for signs of deterioration, focusing on areas where water tends to collect or seep into the material.
During freeze-thaw cycles, trapped moisture expands and contracts within masonry pores, creating internal pressure that can lead to spalling, cracking, and structural compromise. You'll want to pay particular attention to horizontal surfaces, joints, and areas near downspouts where moisture intrusion commonly occurs. Document any new cracks, chips, or surface deterioration, as these indicate potential freeze-thaw damage requiring immediate attention.
Install monitoring devices to track temperature variations and moisture levels in critical areas of your masonry structure. When you detect early warning signs, such as surface scaling or pop-outs, consult a masonry specialist to assess the damage extent and recommend appropriate repairs. Remember that preventing moisture infiltration is key to minimizing freeze-thaw damage, so maintain proper drainage systems and guarantee all waterproofing measures remain intact throughout the winter season. Additionally, be proactive in scheduling masonry restoration services to address any issues before they escalate into larger problems.
Fall Preparation Guidelines
To protect your masonry's integrity before winter sets in, you'll need to remove all accumulated leaves and debris from your building's exterior surfaces and joint lines. You should conduct a thorough inspection of your drainage systems, ensuring downspouts and gutters are clear and properly directing water away from masonry walls. It's critical to apply sealant to vulnerable surface areas, particularly around windows, caps, and copings where water infiltration commonly occurs. Additionally, consider scheduling a professional tuckpointing for mortar joint repair to ensure your masonry is well-maintained and protected against moisture intrusion.
Clear Debris and Leaves
Neglect in clearing organic debris from masonry surfaces can lead to severe structural deterioration during fall months. When leaves, twigs, and other organic matter accumulate against your building's masonry, they trap moisture and create an environment conducive to moss growth and structural damage. You'll need to implement a systematic debris removal schedule to protect your investment.
Focus on areas where leaf accumulation is most problematic: corners, window wells, and building-to-ground changes. You'll want to clear these zones at least bi-weekly during peak fall seasons. Install protective screens over drainage systems to prevent debris from entering and causing blockages that could lead to water damage.
Don't forget vertical surfaces – wind-blown debris can lodge itself in mortar joints and architectural details. Use soft-bristled brushes or low-pressure air to remove trapped materials without damaging the masonry surface. If you're managing multiple properties, create a rotation schedule that prioritizes buildings with heavy tree coverage or those in wind corridors. Remember, proactive debris management isn't just about aesthetics – it's a vital step in preserving your masonry's structural integrity and preventing costly repairs. Additionally, regular maintenance can help prevent issues related to masonry restoration and ensure the long-term durability of your property.
Inspect Drainage Systems Thoroughly
Along with debris management, extensive drainage system inspections serve as a vital cornerstone of fall masonry maintenance. You'll need to examine all components of your building's water management infrastructure to prevent potential damage during winter months.
Start your drainage system maintenance by checking downspouts and gutters for proper attachment to the masonry walls. Look for signs of rust, separation, or loose fasteners that could compromise water flow during heavy rains or snow melts. You'll want to verify that all drainage outlets direct water at least four feet away from your building's foundation.
Conduct a thorough water flow assessment by inspecting your building's weep holes, ensuring they're clear and functioning properly. These essential openings allow moisture to escape from behind the masonry walls. Check that all through-wall flashing is intact and properly sealed, as compromised flashing can lead to interior water damage.
Don't forget to examine your foundation drainage system, including any French drains or underground pipes. Clear any blockages and verify that water flows freely through these systems. If you notice standing water near your foundation, you'll need to address grading issues before winter arrives. Additionally, consider scheduling professional masonry restoration to ensure that your building remains structurally sound and aesthetically pleasing throughout the seasons.
Seal Critical Surface Areas
Proper sealing of critical masonry surfaces stands as your primary defense against moisture infiltration and freeze-thaw damage. As a commercial property owner, you'll need to identify vulnerable areas where water penetration commonly occurs, including parapet walls, copings, and areas near window frames. These zones require specialized masonry surface treatment before winter arrives.
You'll want to evaluate your protective sealant options carefully, considering both penetrating and film-forming sealers based on your building's specific needs. Penetrating sealers work best for vertical surfaces, allowing the masonry to breathe while preventing water infiltration. Film-forming sealers create a protective barrier that's ideal for horizontal surfaces where standing water is a concern.
Before applying any sealant, verify your masonry surfaces are thoroughly cleaned and repairs are completed. You'll need to schedule this work when temperatures remain between 50-80°F for ideal curing. Don't forget to test your chosen sealant on a small, inconspicuous area first to verify compatibility and appearance. Remember that proper application techniques, including even coverage and appropriate thickness, will greatly impact your sealing project's longevity and effectiveness. Additionally, consider consulting with a professional experienced in commercial masonry restoration to ensure the best results for your property.
Essential Maintenance Tools and Equipment
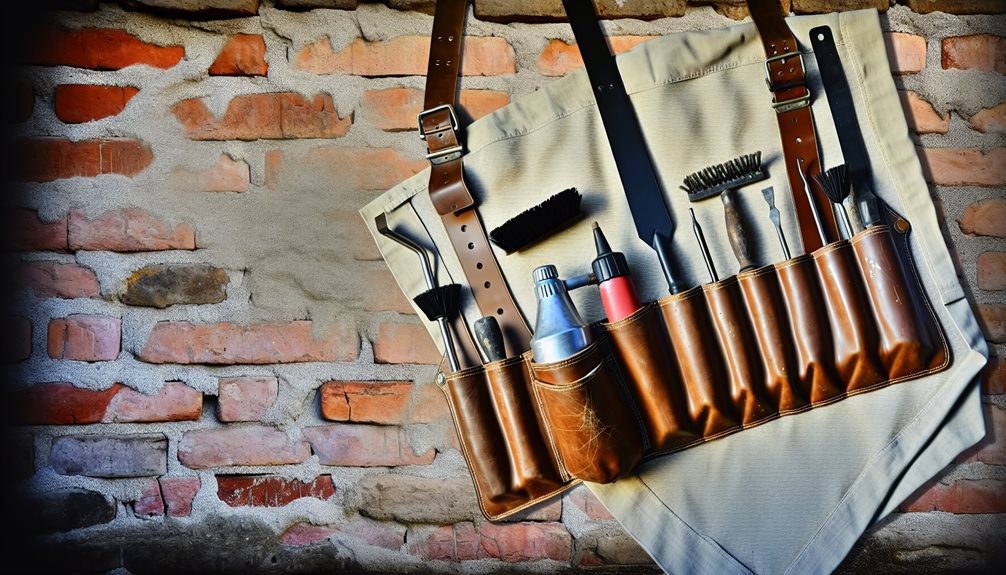
A masonry contractor's arsenal of essential tools and equipment forms the foundation for effective commercial property maintenance. You'll need to invest in quality tools that guarantee precise, professional-grade results for your building's upkeep.
Your essential tools should include tuck-pointing equipment, such as joint rakers, pointing tools, and masonry jointing tools for mortar repair. You'll also require wire brushes, masonry cleaning brushes, and specialized scrapers to remove efflorescence and debris. Maintenance equipment must include pressure washers with adjustable PSI settings, industrial-grade vacuums for dust control, and moisture meters to detect water infiltration.
For structural assessment, you'll want crack monitors, inspection mirrors, and thermal imaging devices to identify potential issues before they escalate. Your toolkit should also contain proper safety equipment: OSHA-approved scaffolding, personal protective gear, and fall protection systems.
Don't forget specialized mixing equipment for mortar and grout preparation, including paddle mixers and material handling tools. Keep your maintenance equipment organized in weather-resistant storage containers, and maintain a detailed inventory system to track tool conditions and replacement schedules.
Professional Assessment Best Practices
Regular professional assessments serve as the cornerstone of effective masonry maintenance programs for commercial properties. You'll need to schedule thorough evaluations at least twice yearly, focusing on both structural integrity and surface conditions. Professional masonry inspection techniques include thermal imaging, moisture testing, and structural load analysis to identify potential issues before they escalate.
When you're working with assessment professionals, guarantee they follow established professional repair guidelines and document all findings systematically. You'll want detailed reports that include photographic evidence, precise measurements, and specific recommendations for repairs. Your assessment team should evaluate mortar joints, inspect for cracking patterns, and assess water drainage systems that could impact your masonry's longevity.
Don't overlook the importance of coordinating these assessments with your building's maintenance schedule. You'll benefit from timing inspections during changing seasons when temperature fluctuations can reveal potential weaknesses. Make sure your assessment team provides you with a clear timeline for recommended repairs and prioritizes issues based on urgency and structural impact. This proactive approach helps you maintain your property's value while preventing costly emergency repairs.
Common Masonry Repair Solutions
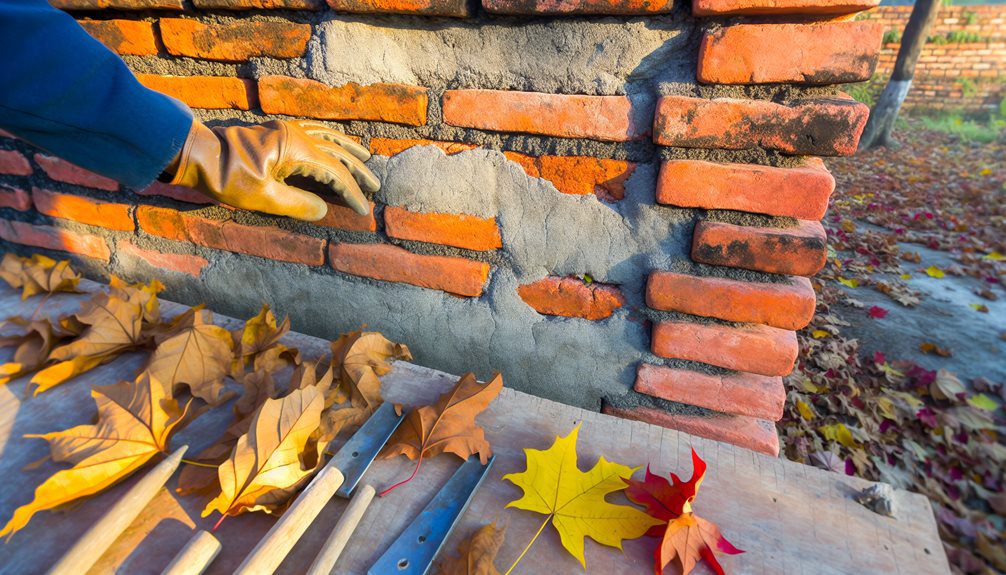
Commonly encountered masonry repair solutions involve repointing deteriorated mortar joints, addressing spalling brick surfaces, and fixing foundation cracks through specialized injection techniques. When you're dealing with mortar repair, you'll need to remove the damaged material to a depth of at least 3/4 inch before applying new mortar that matches the original composition and color. This process requires precision to maintain your building's historical integrity and structural stability.
For brick replacement, you'll want to carefully remove damaged units without disturbing surrounding materials. It's essential to match new bricks with existing ones in size, color, and texture. You'll need to take into account the bond pattern and guarantee proper spacing between units. The installation process must include appropriate moisture control measures to prevent future deterioration.
Advanced repair solutions might include crack stitching with helical ties, application of waterproof coatings, or installation of weep holes for proper drainage. You'll find that implementing these repairs systematically, while maintaining proper documentation of all work performed, helps secure your masonry restoration project's long-term success and compliance with building codes.
Preventative Care Scheduling
While proper repair techniques form the foundation of masonry maintenance, implementing a structured preventative care schedule will protect your investment and minimize future repair costs. By establishing routine checkups, you'll identify potential issues before they escalate into major structural problems.
Your preventative scheduling should include quarterly visual inspections to assess mortar joints, check for cracks, and evaluate water drainage systems. Schedule thorough professional assessments annually, preferably in early spring after winter's harsh conditions have subsided. During these evaluations, technicians will examine your building's entire masonry system, including foundations, walls, and architectural details.
Incorporate seasonal-specific tasks into your maintenance calendar. Plan cleaning and waterproofing applications during dry weather conditions, typically in late spring or early fall. Schedule mortar joint inspections before winter to guarantee your structure's weather resistance. Don't forget to document all maintenance activities, creating a detailed history of your building's care that'll help identify patterns and anticipate future needs.
Cost-Effective Maintenance Planning
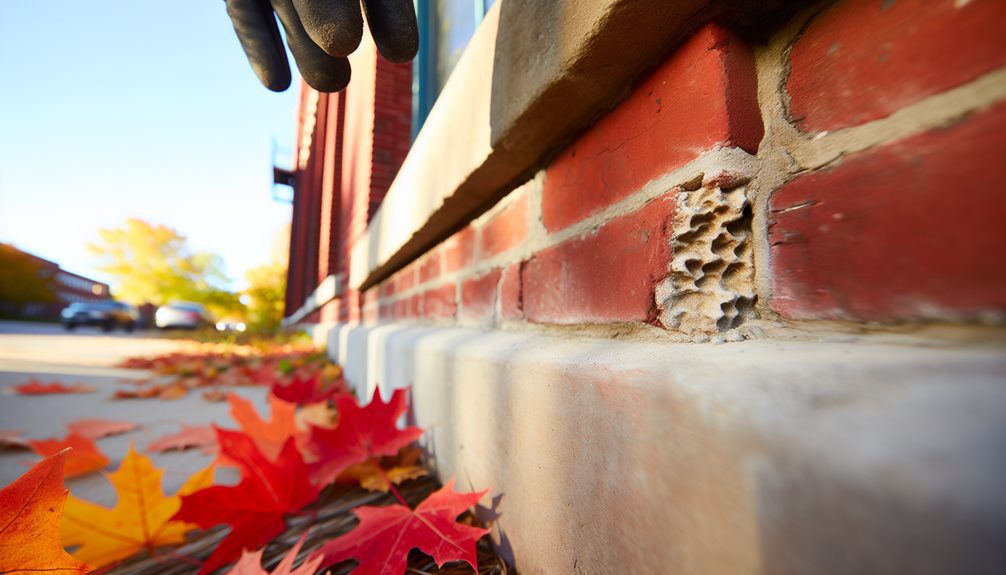
Every masonry maintenance plan must balance quality care with budget constraints. You'll need to conduct a thorough cost analysis of your property's masonry needs, identifying critical repairs that require immediate attention versus those that can be addressed over time. Begin by creating a detailed inventory of all masonry elements and their current condition.
Your budget allocation should prioritize preventative maintenance, as it's considerably less expensive than emergency repairs. Consider dividing your maintenance budget into three tiers: immediate repairs (40%), preventative maintenance (35%), and future planning (25%). You'll find this approach helps prevent costly deterioration while maintaining financial stability.
To maximize your maintenance dollars, bundle similar repair tasks together to reduce contractor mobilization costs. Schedule routine inspections during shoulder seasons when rates are typically lower. You'll also want to establish relationships with reliable masonry contractors who can offer volume discounts for ongoing maintenance work. Document all repairs and maintenance activities to track costs and identify patterns that might help optimize future spending. This data-driven approach guarantees you're making informed decisions about your property's masonry upkeep while maintaining fiscal responsibility.
Frequently Asked Questions
How Long Does Masonry Repair Work Typically Last Before Needing Replacement?
When you invest in quality masonry repair work, you'll typically see repair longevity of 15-25 years, though this can vary based on several factors. Your masonry lifespan depends heavily on the repair method used, environmental conditions, and initial workmanship quality. You'll get the best results when repairs are done by certified professionals using proper materials and techniques. With regular maintenance and protection from moisture damage, you can extend these timeframes considerably.
Can Different Types of Masonry Materials Be Mixed During Repairs?
While you can mix different masonry materials during repairs, you'll need to carefully consider masonry compatibility concerns first. Your repair material selection must match the existing structure's properties, including porosity, strength, and thermal expansion rates. If you don't properly match materials, you'll risk compromising the repair's durability and potentially damage the surrounding masonry. It's best to consult a structural engineer to guarantee your chosen materials will work together effectively.
What Insurance Coverage Should Property Owners Have for Masonry-Related Incidents?
You'll need extensive liability coverage that specifically addresses masonry-related incidents. Make sure your policy includes protection against structural failures, falling debris, and property damage caused by deteriorating masonry. It's essential to have coverage that extends to both your building's occupants and passersby. You'll want to work with an insurance provider who understands commercial masonry structures and can tailor coverage to include both sudden incidents and gradual deterioration issues.
How Do Building Codes Affect Masonry Maintenance Requirements in Different Regions?
Building code compliance for masonry varies considerably based on your location's climate, seismic activity, and environmental factors. You'll need to follow your region's specific masonry standards, which typically address structural integrity, mortar composition, and reinforcement requirements. For example, if you're in an earthquake-prone area, you'll face stricter requirements for wall ties and reinforcement, while coastal regions emphasize salt-resistant materials and moisture protection in their codes.
Are There Historical Preservation Guidelines That Affect Masonry Maintenance Decisions?
Yes, you'll need to comply with historic preservation guidelines when maintaining masonry on designated historic buildings. These regulations often specify approved materials, restoration techniques, and maintenance standards that preserve the structure's historical integrity. You're required to follow the Secretary of the Interior's Standards for historic properties, and many local preservation boards have additional requirements. It's crucial to consult with preservation specialists before undertaking any maintenance work on historically significant masonry structures.