Tuckpointing serves as your commercial building's first line of defense against moisture infiltration and structural deterioration. You'll need to address deteriorating mortar joints promptly, as untreated damage can lead to extensive masonry failures and costly repairs. Professional tuckpointing removes damaged mortar to a depth of at least 3/4 inch and replaces it with fresh, properly matched material, extending your masonry's lifespan by 25-30 years. You'll preserve both structural integrity and market value while ensuring compliance with municipal codes. The right approach to mortar selection and application techniques determines your building's long-term durability and protection from freeze-thaw damage.
What Is Tuckpointing
Deteriorating mortar joints demand tuckpointing, a specialized masonry maintenance technique that involves removing damaged mortar from a building's exterior and replacing it with fresh mortar. You'll find this critical masonry restoration process helps prevent water infiltration and structural damage while extending your building's lifespan.
When you're implementing tuckpointing techniques, you'll need to carefully remove the old mortar to a depth of at least 3/4 inch using specialized tools like joint rakers or grinders. It's crucial to match the new mortar's color and composition to the existing material, ensuring a seamless blend with your building's historical character. The process requires precise application of the fresh mortar in two stages: the base layer and the final pointing mortar.
You'll discover that professional tuckpointing involves more than just filling gaps. It's about understanding the building's age, original construction methods, and environmental factors affecting the mortar. By maintaining your building's mortar joints through regular tuckpointing, you're joining a community of property owners who prioritize preservation and protect their investments through proper masonry maintenance. Additionally, professional tuckpointing services ensure compliance with municipal code violations, safeguarding your property from potential legal issues.
Signs of Deteriorating Mortar Joints
Vigilance in monitoring your building's masonry condition helps identify mortar joint problems before they become severe. Regular inspections can reveal telltale signs that your building's mortar joints need attention.
You'll notice deterioration starting with visible cracking, often appearing as hairline fractures that gradually widen. During your mortar color analysis, watch for areas where the mortar has become lighter or darker than surrounding sections, as this indicates moisture penetration and potential degradation. When performing joint width assessment, look for variations in joint sizes, as expanding gaps suggest underlying structural issues.
Other critical indicators include powdering or crumbling mortar that you can easily scrape away with a key or screwdriver. You'll also want to check for missing chunks of mortar, which create pockets where water can collect. If you spot white, crusty deposits (efflorescence) on your masonry surface, it's a clear sign that water's moving through your mortar joints. Deep erosion patterns, particularly in horizontal joints, indicate serious water damage that requires immediate attention. Don't overlook signs of brick displacement or bulging walls, as these often stem from compromised mortar joints. Additionally, addressing these issues promptly can prevent further structural damage that may jeopardize the integrity of your building.
Benefits of Professional Tuckpointing
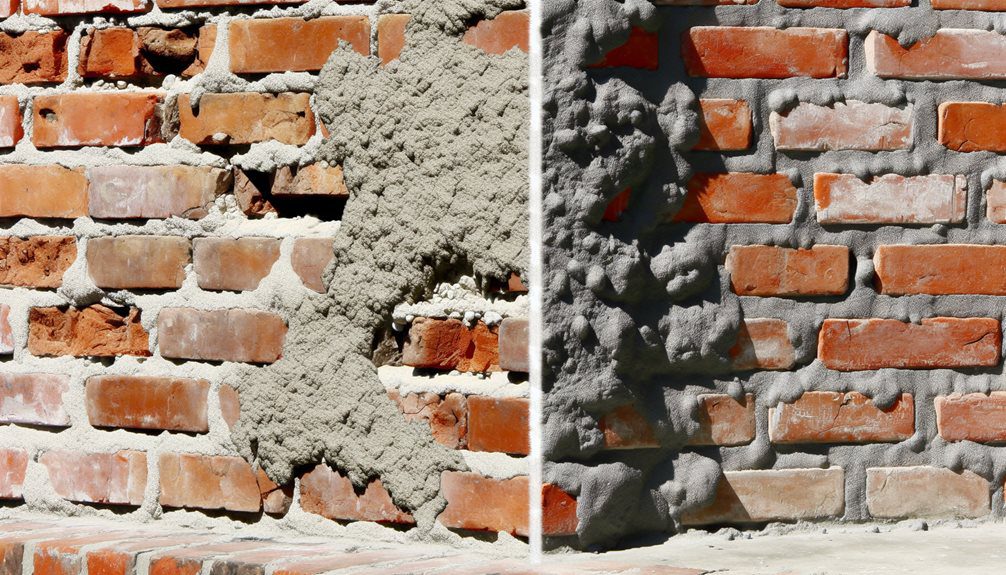
Professional tuckpointing creates significant cost savings by preventing expensive structural repairs that often result from untreated mortar deterioration in your commercial building. You'll maximize your building's lifespan through timely repointing, as restored mortar joints protect the underlying masonry from moisture infiltration and freeze-thaw damage. The restoration of deteriorated joints through professional tuckpointing maintains your building's structural integrity while preserving its market value, making it an essential investment in your property's long-term sustainability. Additionally, tuckpointing services provided by experienced professionals ensure that the architectural beauty of your building is preserved throughout the restoration process.
Cost Savings Over Time
Investing in timely tuckpointing maintenance delivers substantial long-term financial benefits for commercial property owners. When you address mortar deterioration early through professional tuckpointing, you'll prevent extensive structural damage that could cost tens or even hundreds of thousands of dollars to repair later. This cost efficiency approach protects your building's integrity while maintaining its market value.
By implementing regular tuckpointing maintenance, you're avoiding the compounding effects of water infiltration, which can lead to devastating interior damage, mold growth, and compromised structural stability. The long-term savings become evident when you compare the relatively modest cost of periodic tuckpointing to the extensive expenses of major masonry reconstruction or complete wall replacement.
You'll also benefit from reduced energy costs, as properly maintained mortar joints prevent air leakage and improve your building's thermal efficiency. Additionally, you're protecting your investment by extending the life expectancy of your masonry walls by 25-30 years. When you factor in the preservation of architectural aesthetics and the prevention of accelerated deterioration, professional tuckpointing proves to be one of the most cost-effective maintenance investments you can make. Furthermore, regular tuckpointing contributes to structural integrity by ensuring that your masonry remains safe and functional over time.
Enhanced Building Longevity
Regular tuckpointing maintenance directly extends your building's structural lifespan well beyond its original projections. When you invest in professional tuckpointing services, you're actively preserving your building's structural integrity through systematic mortar replacement and joint restoration. The enhanced durability you'll achieve helps your building withstand decades of environmental stress, thermal cycling, and moisture infiltration.
Your building's longevity depends greatly on the mortar quality used during tuckpointing. Professional contractors select specialized mortar compounds that match your building's existing materials while providing superior binding properties. This attention to material compatibility guarantees that your walls maintain their load-bearing capacity and prevent the cascading deterioration that often affects aging commercial structures.
You'll notice that properly tuckpointed buildings consistently outperform their untreated counterparts by 20-30 years. The reinforced masonry joints create an effective barrier against water penetration, preventing internal steel reinforcement from corroding and maintaining the structural stability of your entire building envelope. This thorough protection system helps you avoid costly structural repairs and maintains your property's market value throughout its extended service life. Additionally, regular tuckpointing is essential for maintaining high-quality standards in your building's overall appearance and performance.
Common Tuckpointing Materials
Mortar selection forms the cornerstone of successful tuckpointing projects in commercial buildings. You'll need to choose from several mortar types, including Type N, Type O, and Type S, each offering distinct properties for specific applications. Type N mortar, with its medium compressive strength, serves as your go-to choice for most above-grade exterior walls, while Type O's softer composition makes it ideal for historic restoration work.
When selecting tuckpointing materials, you'll want to take into account both Portland cement-based and lime-based mortars. Portland cement mortars provide superior strength and durability, making them suitable for modern structures. However, if you're working on historic buildings, you'll find that lime-based mortars offer better breathability and flexibility, matching the original construction methods. Don't forget to factor in color-matching aggregates and pigments to guarantee your repairs blend seamlessly with existing mortar joints.
You'll also need specialized tools, including pointing tools, joint rakers, and mixing equipment. The quality of your mixing sand matters considerably – it should be sharp, well-graded, and free from impurities to guarantee proper bonding and long-term durability of your tuckpointing work. Additionally, consider that brick repair is essential for maintaining structural integrity and aesthetic appeal in commercial buildings.
Best Practices for Masonry Maintenance
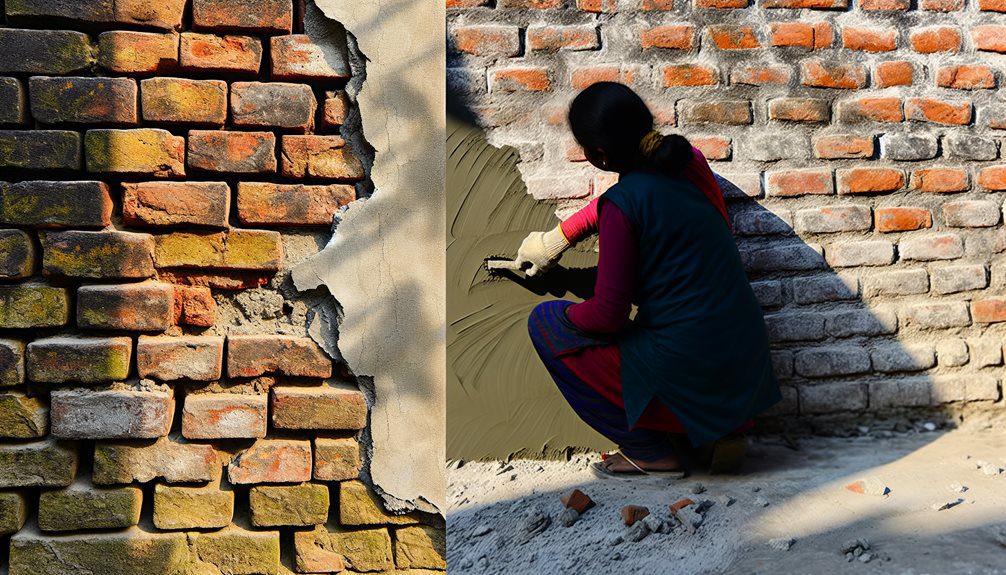
While proper material selection sets the foundation for tuckpointing success, implementing an all-encompassing masonry maintenance program helps prevent deterioration and extends the life of commercial buildings. You'll need to establish a regular inspection schedule, typically bi-annual, to identify early signs of mortar joint failure, brick deterioration, or water infiltration issues.
As part of your masonry care strategy, you should document all observations and maintain detailed records of previous restoration techniques applied. You'll want to clean your masonry surfaces annually using appropriate pH-neutral cleaners and soft-bristled brushes to remove environmental pollutants and prevent the accumulation of harmful deposits.
When you notice deterioration, don't wait to address it. You'll need to prioritize repairs based on severity, focusing first on areas showing water infiltration or structural concerns. Make certain you're maintaining proper drainage systems and waterproofing measures to protect your masonry investment. Additionally, you should seal any cracks promptly and maintain caulking around windows and other penetrations. Remember to coordinate your maintenance schedule with seasonal weather patterns to guarantee ideal conditions for repairs and treatments. Regular maintenance can significantly minimize the risk of future water intrusion and costly repairs.
When to Schedule Tuckpointing
You'll want to schedule your commercial building's tuckpointing during dry weather conditions, typically in late spring or early fall, when temperatures consistently range between 40-90°F. Your first indicators for needed tuckpointing include visible mortar deterioration, such as cracking, crumbling, or recessed joints deeper than 1/4 inch from the masonry face. These warning signs, combined with proper seasonal timing, help guarantee ideal mortar curing and maximum bond strength between your building's masonry units. Regular maintenance, including masonry restoration, ensures the longevity and structural integrity of your commercial property.
Seasonal Planning Considerations
Planning tuckpointing projects requires careful consideration of seasonal weather patterns and temperature fluctuations. You'll want to schedule your tuckpointing work during periods when temperatures consistently remain between 40°F and 90°F, as mortar requires specific conditions to cure properly. Spring and fall typically offer perfect conditions for your maintenance schedule, allowing adequate time for materials to set and bond.
When you're mapping out your project timeline, factor in the likelihood of rain, as moisture can compromise mortar installation and curing. You'll need at least 24 hours of dry weather after application. Additionally, consider that summer's extreme heat can cause mortar to dry too quickly, while winter's freeze-thaw cycles can damage newly applied materials.
For your commercial property's maintenance schedule, it's essential to align tuckpointing with other exterior work. You'll maximize efficiency by coordinating these projects during moderate weather windows. Remember that your geographic location will influence your best scheduling timeframe – coastal areas may require different timing considerations than inland regions due to humidity levels and maritime weather patterns. Additionally, understanding the importance of masonry restoration can help you determine the right time for tuckpointing alongside other maintenance tasks.
Signs of Mortar Deterioration
Identifying early warning signs of mortar deterioration helps prevent extensive masonry damage and costly repairs. As a building owner or facility manager, you'll need to regularly inspect your masonry walls for specific indicators that suggest it's time for tuckpointing.
Watch for discoloration or fading of the mortar color, which often signals the beginning stages of deterioration. You'll notice the joints becoming lighter or taking on a chalky appearance as the cement binder breaks down. Pay close attention to changes in joint width, especially when you observe gaps between the mortar and bricks, or when the mortar begins receding deeper than the brick face.
Other critical signs include:
- Visible cracks or crumbling in the mortar joints
- Loose or missing pieces of mortar
- White, powdery deposits (efflorescence)
- Water stains or dampness on interior walls
- Mortar that's soft enough to scratch with a key
- Uneven joint surfaces or deterioration patterns
When you spot these indicators, especially if they affect more than 25% of your building's mortar joints, it's time to schedule professional tuckpointing services to maintain your structure's integrity. Additionally, prompt attention to these signs can help ensure compliance with municipal codes and prolong the lifespan of your masonry.
Cost Considerations
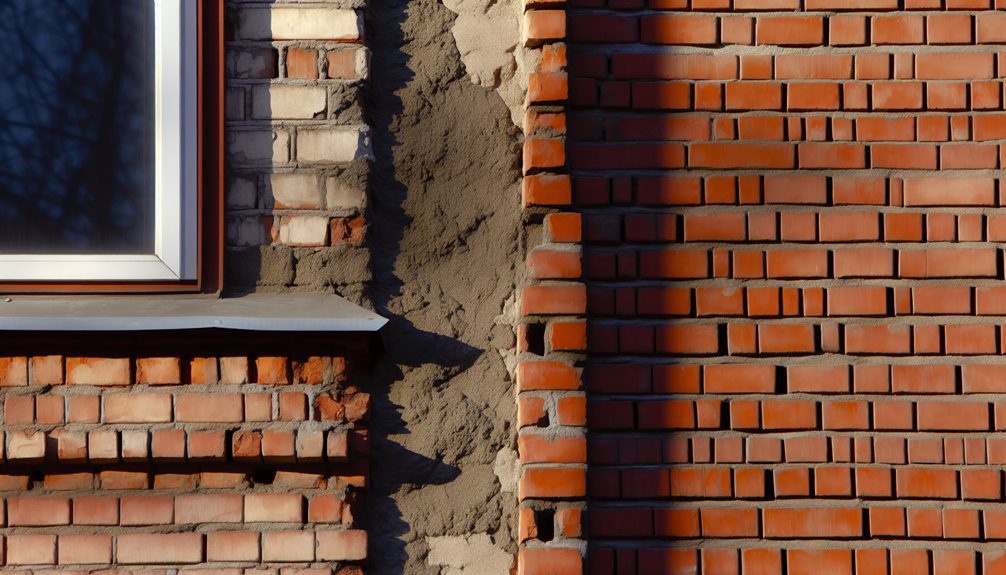
Three major factors drive tuckpointing costs in commercial buildings: labor intensity, material selection, and project scope. You'll need to take into account skilled mason hours, as proper tuckpointing requires extensive manual work and expertise. During your cost analysis, factor in that experienced masons typically charge between $8-15 per linear foot, depending on your location and project complexity.
Material costs will vary based on your mortar selection and whether you're matching historic materials. You'll want to budget $25-40 per bag of specialized mortar, and don't forget to include the cost of color matching if you're working with an older structure. When developing your budget planning strategy, include a 15-20% contingency for unexpected deterioration discovered during the work.
Project scope considerably impacts your final costs. You'll need to take into account scaffolding rental, permits, and whether you're addressing all facades or just problem areas. A thorough inspection can help you prioritize critical sections if you're working with limited funds. For multi-story commercial buildings, you're typically looking at $7-12 per square foot for extensive tuckpointing work, including preparation and cleanup.
Historic Building Preservation
When preserving historic buildings, tuckpointing demands meticulous attention to original construction methods and materials. You'll need to carefully analyze the original mortar composition and match its color, texture, and strength to maintain historical authenticity. Historic preservation techniques require you to document existing conditions thoroughly before beginning any restoration work.
You'll find that historic buildings often require specialized lime-based mortars rather than modern Portland cement. It's crucial to understand that these traditional materials allow proper moisture movement through the masonry, which prevents damage to the historic fabric. When you're implementing adaptive reuse strategies, you must balance modern building requirements with preservation goals.
Before starting any tuckpointing work, you'll want to conduct mortar analysis and create test panels to verify compatibility with existing materials. You're responsible for maintaining the building's character-defining features while addressing structural integrity. Remember that improper materials or techniques can accelerate deterioration and compromise the building's historical significance. Working with preservation specialists who understand period-appropriate tools and techniques will help you achieve authentic results that meet preservation standards.
Weather Impact on Mortar
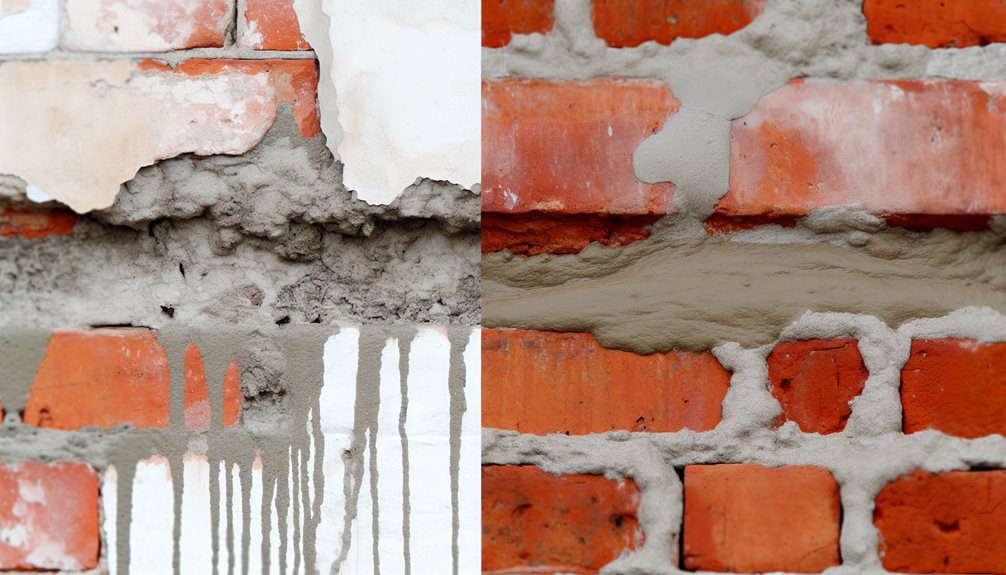
When you're evaluating mortar deterioration in commercial buildings, you'll often encounter freeze-thaw damage that manifests as cracking, spalling, and disintegration of the mortar joints. You'll notice that moisture penetration through compromised mortar joints can accelerate during winter months, as water expands upon freezing and creates internal pressure within the masonry structure. The combination of these weather-related stressors requires you to carefully evaluate both surface deterioration and subsurface damage patterns to determine the appropriate tuckpointing intervention strategy.
Freeze-Thaw Damage Analysis
Seasonal temperature fluctuations pose a significant threat to commercial building mortar through the freeze-thaw cycle. When water infiltrates the mortar joints, repeated freeze-thaw cycles can cause extensive deterioration of your building's masonry structure. You'll notice this damage manifests as cracking, spalling, and eventual disintegration of the mortar joints.
To effectively analyze freeze-thaw damage, you'll need to assess moisture absorption patterns in your building's masonry. Watch for telltale signs like efflorescence (white, powdery deposits), which indicates water migration through the mortar. You can perform simple moisture content tests using a calibrated moisture meter to identify areas of concern.
Understanding your building's exposure to freeze-thaw cycles is vital for maintenance planning. Northern climates typically experience 50 to 150 freeze-thaw cycles annually, while southern regions may see fewer than 20. You'll want to document areas where snow accumulates against walls or where rain consistently hits the façade. This analysis helps you identify vulnerable sections requiring immediate tuckpointing intervention. By monitoring these patterns, you're better equipped to prevent structural deterioration and maintain your building's integrity throughout seasonal changes.
Moisture Penetration Effects
Numerous weather-related factors contribute to moisture penetration in commercial building mortar joints, with wind-driven rain and sustained humidity posing the greatest risks. You'll find that deteriorating mortar joints can quickly compromise your building's moisture barriers, leading to extensive structural damage if left unaddressed.
When you're evaluating moisture penetration, you'll need to examine how water ingress affects different areas of your masonry. The most vulnerable points typically occur at corners, changes between materials, and areas where previous repairs haven't properly bonded. Your building's exposure to prevailing winds and seasonal weather patterns will determine the rate of deterioration in these critical zones.
You can identify early signs of moisture-related damage by looking for efflorescence, spalling brick faces, and deteriorating mortar joints. These indicators suggest that your building's natural moisture barriers have been compromised. The longer you wait to address these issues, the more likely you'll face costly repairs to both the masonry and interior systems. By maintaining proper mortar joint integrity through regular tuckpointing, you're protecting your investment and ensuring your building's long-term structural stability.
Safety and Building Codes
Throughout commercial building maintenance, adherence to safety protocols and building codes remains paramount for tuckpointing operations. You'll need to guarantee your tuckpointing work complies with local safety regulations and passes routine building inspections. When you're maintaining commercial structures, you're responsible for meeting OSHA standards for scaffolding, personal protective equipment, and fall protection systems.
You must follow specific code requirements for mortar composition and joint depths, which typically vary by jurisdiction. Your tuckpointing work should align with the International Building Code (IBC) and local amendments, particularly regarding structural integrity and fire resistance ratings. Don't forget to obtain necessary permits before beginning work, as they're essential for commercial projects.
As a building maintenance professional, you'll need to document your compliance with safety standards and maintain detailed records of your work. This includes photographing before and after conditions, recording mortar mix ratios, and logging safety meetings. Remember that your liability insurance may require specific safety protocols, and failing to follow them could void your coverage during tuckpointing operations.
Frequently Asked Questions
Can Tuckpointing Be Done in Phases to Spread Costs Over Time?
Yes, you can implement a phased approach to tuckpointing to better manage your costs. Start by having a mason assess your building's mortar joints and create a priority-based repair schedule. You'll want to address severely deteriorated areas first, then move to less critical sections over time. This cost management strategy lets you spread your investment across multiple budget cycles while ensuring you're protecting your building's structural integrity and appearance.
What Qualifications Should I Look for When Hiring a Tuckpointing Contractor?
When you're hiring a tuckpointing contractor, you'll want to create a qualifications checklist that includes several key elements. Look for at least 5-10 years of documented experience, proper licensing, and insurance coverage. You'll want to verify their masonry certification and ask about their crew's training. Don't forget to request recent project photos, local references, and warranty terms. Remember, you're joining other property owners who prioritize quality workmanship by choosing certified professionals.
How Long Does the Tuckpointing Process Typically Take for Commercial Buildings?
Your tuckpointing duration will depend on several factors: building size, deterioration level, and weather conditions. For a typical commercial building (10,000-15,000 sq ft), you'll need to plan for a 2-3 week project timeline. However, if you're dealing with extensive damage or a larger structure, it could extend to 4-6 weeks. You'll want to factor in curing time between stages and any weather-related delays that might affect your project's completion.
Will Tuckpointing Work Disrupt Normal Business Operations in My Building?
You'll likely experience some operational disruptions during tuckpointing, but most contractors work strategically to minimize impact. They'll typically section off work areas, install protective barriers, and schedule noisy activities during off-peak hours. While there's dust and equipment noise, you can maintain business operations by coordinating with your contractor on timing and workspace access. Many building owners find that tuckpointing benefits far outweigh temporary inconveniences when properly managed.
Are There Alternatives to Traditional Tuckpointing for Modern Commercial Buildings?
You'll find several modern alternatives to traditional tuckpointing that can protect your building's integrity. Advanced polymer-based mortar alternatives offer enhanced flexibility and durability compared to conventional cement mortars. Flexible sealants, including silicone and polyurethane compounds, can effectively fill smaller joints while accommodating building movement. These innovations often provide better weather resistance and require less frequent maintenance. However, you'll want to consult with a masonry specialist to determine which solution best suits your structure's specific needs.