Tuckpointing high-rise buildings requires specialized access systems and safety protocols that meet OSHA standards, including full-body harnesses and 5,000-pound rated anchor points. You'll need to account for elevation-specific challenges like wind speeds (staying under 20 mph) and temperature variations that affect mortar performance. Select appropriate mortar types (N, S, or M) based on building requirements, and guarantee ASTM C270 compliance. Use specialized equipment including raking tools, portable mixers with dust control, and pneumatic tools when working from swing stages. Quality control demands systematic documentation and elevation inspections at multiple stages. The complexities of high-rise tuckpointing extend far beyond these fundamental requirements.
Safety Equipment and Access Systems
Fall-protection systems and access equipment form the foundation of any high-rise tuckpointing operation. You'll need to verify your safety gear meets OSHA requirements, including full-body harnesses, lanyards with shock absorbers, and anchor points rated for a minimum 5,000-pound load capacity. Your personal fall arrest system (PFAS) must be inspected daily before ascending.
For buildings under 300 feet, you'll typically deploy suspended scaffolding systems with safety lines and mechanical descent devices. When you're working on taller structures, you'll require specialized access ladders or building maintenance units (BMUs) integrated with the structure's facade access system. Don't forget to incorporate two independent anchor points – one for your primary suspension and another for your backup system.
Your toolkit must include proper edge protection, including guardrails and toe boards where applicable. You'll want to establish clearly marked exclusion zones below your work area and implement an all-encompassing communication system between ground crews and elevated workers. Remember, your fall protection plan must account for swing fall hazards and include rescue procedures specific to your working height and building configuration. Additionally, it's crucial to use high-quality materials to ensure the durability and safety of your tuckpointing work.
Weather Considerations for Height Work
Most high-rise tuckpointing operations require strict adherence to weather monitoring protocols, as conditions can change rapidly at elevation. You'll need to monitor wind effects consistently, as speeds typically increase with height and can destabilize scaffolding or affect material application. Don't proceed with work when wind velocities exceed 20 mph, as this compromises both safety and mortar consistency.
Temperature variations between ground level and working height can greatly impact your material performance. You'll find that temperatures can differ by 5-10 degrees Fahrenheit per 1,000 feet of elevation, affecting mortar curing times and workability. It's essential that you maintain proper material temperatures by using heated enclosures when working below 40°F or implementing cooling measures above 90°F.
You'll want to track humidity levels and precipitation forecasts hourly. Your mortar requires specific moisture conditions for proper curing, and excess humidity can lead to efflorescence. Consider installing weather monitoring stations at various heights on your scaffolding system to get accurate readings. Always factor in the possibility of sudden weather changes and keep your communication channels open with ground personnel for immediate updates. Additionally, ensure that you use high-quality materials to enhance the durability of your repairs in varying weather conditions.
Modern Mortar Selection
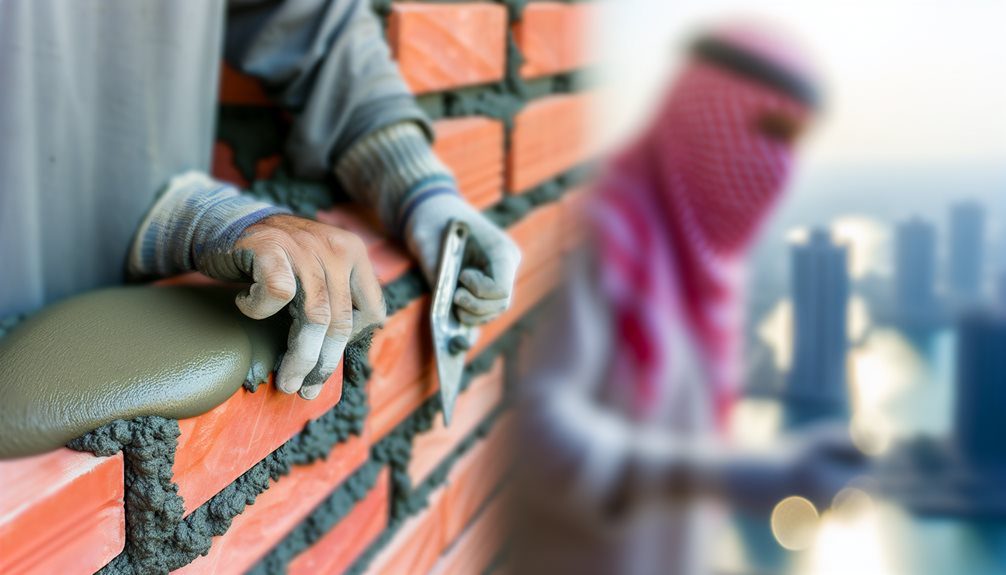
Precision in mortar selection stands as a critical factor for high-rise tuckpointing success. You'll need to take into account Type N, S, or M mortars based on your building's specific requirements and exposure conditions. Each type offers distinct compression strengths and mortar durability characteristics that you'll match to your project's demands.
When you're selecting your mortar mix, you'll want to assess the original mortar's composition through lab testing. You're looking for aggregate ratios, binder types, and compression values that'll guarantee compatibility with existing masonry. Color matching becomes essential here – you'll need to source aggregates and pigments that'll blend seamlessly with weathered joints.
You'll find that modern polymer-modified mortars offer enhanced workability and adhesion properties that you can't get with traditional mixes. They're particularly valuable when you're working on exposed elevations where wind and rain pose constant challenges. Think about using pre-blended commercial products that'll provide consistent batch quality and reduce on-site mixing variables. You'll want to verify that your selected mortar meets ASTM C270 specifications and accommodates thermal movement in your building's facade system. Additionally, consider partnering with a trusted specialist in masonry restoration to ensure the highest quality materials are utilized throughout your project.
Specialized Tools and Techniques
Professional tuckpointing demands an arsenal of specialized equipment tailored for high-rise applications. You'll need raking tools with varying blade widths to match your building's joint profiles, guaranteeing precise mortar removal without damaging surrounding masonry. For efficient mortar mixing at height, you'll want to incorporate portable mixers with dust control systems that meet OSHA compliance standards.
Your joint repair toolkit must include pointing irons of various sizes, allowing you to compress new mortar effectively into joints at different depths. You'll find that pneumatic tools, while expensive, greatly enhance productivity on large-scale projects. They're particularly valuable when you're working with swing stages or suspended scaffolding systems.
Don't overlook the importance of modern joint finishing tools – they're essential for achieving that clean, professional strike that distinguishes quality tuckpointing work. You'll need to maintain a complete set of striking irons, ranging from 3/8" to 3/4", to accommodate different joint widths. For deep joint repairs, you'll want to keep handy a selection of joint packing tools that help guarantee proper mortar consolidation and prevent voids that could compromise the repair's integrity. Additionally, employing techniques for masonry restoration can enhance the overall durability and aesthetic appeal of the structure.
Quality Control at Elevation
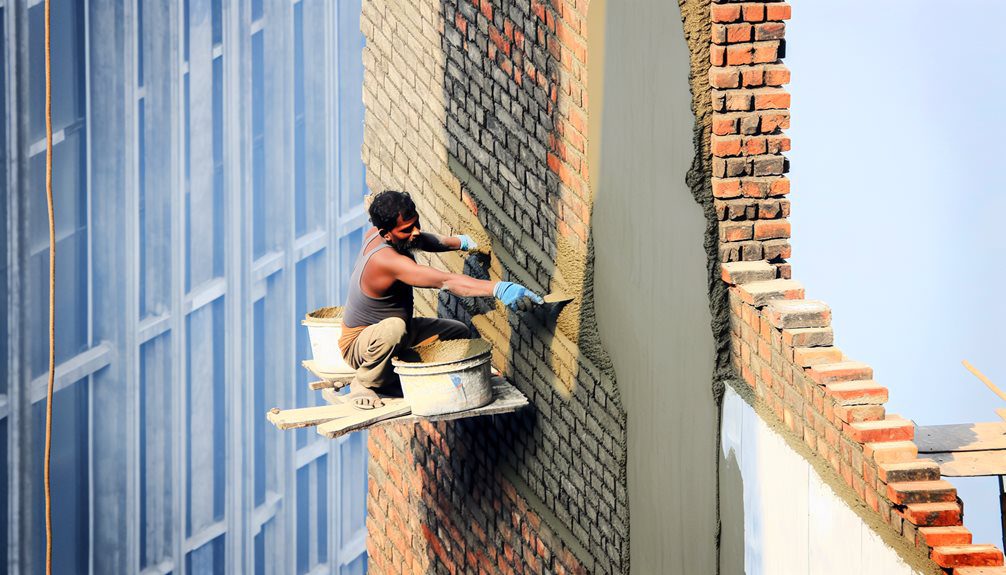
When working at considerable heights, quality control procedures require specific modifications to standard masonry inspection protocols. You'll need to conduct elevation inspections at multiple stages, ensuring each tuckpointing joint meets industry specifications before scaffolding or swing stages are relocated. It's essential to verify material durability through on-site testing at various heights, as environmental conditions can vary greatly from ground level to upper floors.
You'll want to implement a systematic documentation process using high-resolution photography and digital mapping to track joint preparation, mortar consistency, and finished joint profiles. As you progress upward, maintain strict quality controls on mortar mixing stations, whether they're ground-based or elevated platforms. Monitor weather conditions closely, as wind speeds and temperature gradients can affect mortar curing rates differently at higher elevations.
Your inspection points should include checking joint depth consistency, mortar color uniformity, and tooling profile accuracy. Use calibrated depth gauges and color matching standards specific to your elevation zone. Document any deviations immediately and implement corrective measures before moving to adjacent sections to maintain seamless aesthetic continuity across the façade. Proper masonry restoration techniques are vital to ensure the longevity and integrity of high-rise structures.
Frequently Asked Questions
How Long Does Tuckpointing Typically Last on a High-Rise Building?
You'll find that tuckpointing durability typically ranges from 20-30 years when properly executed, though you'll need to factor in your building's exposure to weather conditions. Your maintenance frequency should include inspections every 3-5 years to monitor mortar integrity. If you're managing a structure in harsh climates or coastal areas, you'll likely need to plan for shorter intervals. Professional contractors in your area can help determine your specific timeline based on local conditions.
What Is the Average Cost per Square Foot for High-Rise Tuckpointing?
You'll find tuckpointing costs typically range from $7 to $20 per square foot for high-rise buildings. Your final price depends on several cost factors, including accessibility, scaffolding requirements, and labor rates in your region. Tuckpointing materials like mortar type and color matching compounds will impact your budget, while building height and facade condition can greatly influence overall expenses. You're looking at higher rates above the 10th floor due to additional safety requirements.
Can Tuckpointing Be Done in Sections Over Multiple Years?
You can definitely implement tuckpointing scheduling in phases over multiple years, which is a common approach for budget management and logistical efficiency. When you're planning phased repairs, you'll want to prioritize areas with the most severe deterioration first. It's essential that you coordinate your repair sections logically, ensuring each phase ties in seamlessly with previous work. This strategy lets you spread out costs while maintaining the building's structural integrity and appearance throughout the process.
How Often Should High-Rise Buildings Be Inspected for Tuckpointing Needs?
You'll want to establish regular inspection frequency for your building's masonry, typically conducting thorough assessments every 3-5 years. However, if you're managing properties in harsh climates, you should schedule annual inspections. Your maintenance schedules should include visual surveys from ground level quarterly, complemented by close-up examinations of critical areas. You're better off catching mortar deterioration early, as it'll help you plan interventions and maintain your building's structural integrity more effectively.
Does Tuckpointing Affect the Building's Energy Efficiency and Interior Temperature Control?
You'll notice significant improvements in your building's energy efficiency when you maintain proper tuckpointing. Deteriorated mortar joints create thermal bridges and air leaks that compromise your temperature control systems. By sealing these gaps, you're preventing unwanted air infiltration and heat transfer through the building envelope. Your HVAC system won't have to work as hard, and you'll join other property managers who've reported 10-15% reductions in energy costs after tuckpointing repairs.