Tuckpointing restores your building's energy efficiency by sealing deteriorated mortar joints that allow significant air infiltration and thermal loss through masonry walls. You'll notice up to 30% reduction in air leakage once joints are properly repaired, as the restored mortar prevents the stack effect from creating pressure differentials that drive heat transfer. Your HVAC system won't have to work as hard, resulting in 10-15% lower operating costs annually. The initial investment typically pays for itself within 3-7 years through sustained energy savings of 8-12%. Understanding the mechanics of thermal performance will reveal even more substantial benefits of this essential maintenance practice.
Understanding Mortar Joint Deterioration
While many building components experience wear over time, mortar joints are particularly susceptible to deterioration due to their constant exposure to weathering elements. You'll notice that mortar composition plays a critical role in how joints withstand environmental stresses, as the mixture of cement, lime, and sand must maintain proper ratios to guarantee longevity.
When you're examining deteriorating joints, you'll find several telltale signs that your fellow building managers often encounter. The loss of joint flexibility is a key indicator, typically manifesting as cracking, crumbling, or receding mortar. You're likely to observe these issues especially where water exposure is highest – near roof lines, around windows, and at ground level where splash-back occurs.
Understanding the deterioration process helps you identify problems before they escalate. Water infiltration weakens the mortar composition through freeze-thaw cycles, while chemical reactions between pollutants and binding agents break down the material's structural integrity. You'll also need to watch for signs of efflorescence, those white, crystalline deposits that indicate water's moving through your masonry, signaling potential joint failure. Regular waterproofing techniques can significantly enhance the durability of mortar joints against environmental challenges.
Energy Loss Through Building Walls
Heat transfer through masonry walls represents a considerable source of energy loss in office buildings, particularly when mortar joints have deteriorated. You'll find that compromised mortar joints create pathways for air infiltration, reducing your building's thermal resistance and forcing your HVAC systems to work harder to maintain desired temperatures.
When you examine your building's walls, you'll notice that deteriorating mortar joints can account for up to 15% of total heat loss through the building envelope. Air leakage through these gaps doesn't just affect your energy efficiency; it also leads to increased utility costs and inconsistent indoor temperatures. You're likely to experience these issues most acutely in older buildings where decades of weathering have eroded the mortar's integrity.
The impact becomes even more pronounced in multi-story office buildings, where stack effect intensifies air movement through damaged joints. By addressing these vulnerabilities, you'll enhance your building's thermal performance considerably. Each linear foot of properly repaired mortar joint contributes to improved energy efficiency, helping you maintain consistent indoor temperatures while reducing unnecessary energy consumption through uncontrolled air exchange. Additionally, implementing tuckpointing services can significantly restore the integrity of your masonry, further mitigating heat loss and enhancing overall building performance.
The Science Behind Air Infiltration
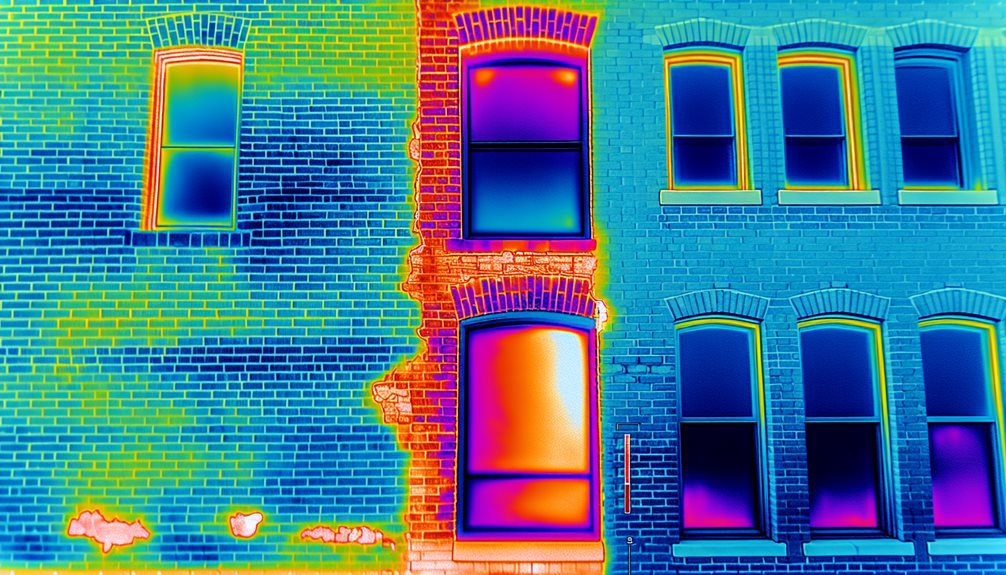
Air infiltration through deteriorated mortar joints follows specific physical principles that govern fluid dynamics in building envelopes. When you're examining your building's masonry, you'll find that airflow dynamics create pressure differentials between the interior and exterior spaces. These differentials drive unconditioned air through even the smallest gaps in your mortar joints, affecting your building's thermal performance.
You'll notice that temperature fluctuations throughout the day intensify this process. As outdoor temperatures rise and fall, the resulting thermal gradient forces air movement through compromised mortar joints. During winter, you're losing heated air through these gaps while drawing in cold outside air. The reverse occurs in summer, when your costly conditioned air escapes while hot air infiltrates inward.
The stack effect compounds these issues in your multi-story building. You'll experience stronger upward air movement as warm air rises through your structure, creating a chimney-like effect that pulls additional unconditioned air through deteriorated mortar joints at lower levels. Understanding these scientific principles helps you recognize why proper tuckpointing is essential for maintaining your building's energy efficiency. Additionally, tuckpointing for restoration not only enhances aesthetics but also significantly reduces energy loss.
Cost Impact of Delayed Maintenance
Deferring tuckpointing maintenance for even a few years can multiply your building's repair costs by three to five times the initial estimates. When you delay addressing deteriorating mortar joints, you'll face cascading issues that extend beyond the masonry itself, impacting your building's overall energy performance and structural integrity.
Your maintenance scheduling needs to account for the compounding nature of mortar deterioration. What begins as a $50,000 tuckpointing project can escalate to $150,000-$250,000 when you factor in water damage to interior walls, mold remediation, and compromised insulation. You'll also experience higher heating and cooling costs due to increased air infiltration through damaged joints.
Budget allocation becomes critical when you consider the exponential growth of repair costs. You're not just paying for basic mortar replacement anymore – you're potentially funding extensive masonry repairs, structural reinforcement, and interior renovations. By implementing a proactive maintenance schedule, you'll protect your investment and avoid the financial burden of emergency repairs. Remember, every dollar you invest in timely tuckpointing saves approximately $4-$6 in future restoration costs. Additionally, routine tuckpointing can help maintain the structural integrity of your building, ensuring it remains safe and efficient for years to come.
Professional Tuckpointing Best Practices
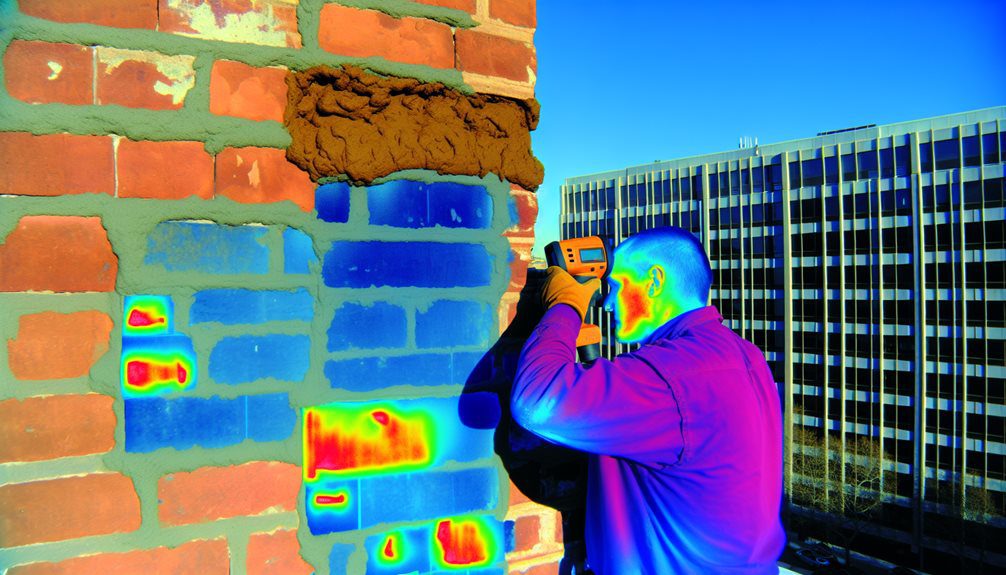
Professional tuckpointing requires strict adherence to industry-established methods and precise material selection to guarantee longevity. You'll need to begin by thoroughly evaluating the existing mortar's condition and identifying areas requiring repair. When implementing modern tuckpointing techniques, you must remove deteriorated mortar to a depth of at least twice the joint's width, assuring clean, sound surfaces for the new material to bond.
Your mortar selection should closely match the building's original composition, considering factors like compressive strength, water retention, and thermal expansion properties. You'll want to analyze the existing mortar through laboratory testing to determine its composition and match it appropriately. When you're applying new mortar, maintain consistent joint profiles and verify proper tooling at the right time – neither too wet nor too dry.
Weather conditions considerably impact your work quality, so you'll need to maintain temperatures between 40-90°F during application and curing. You must also protect fresh joints from direct sunlight, wind, and rain for at least 72 hours. Following these established protocols guarantees your tuckpointing work meets industry standards and provides maximum durability for your building's masonry system. Additionally, using high-quality materials is crucial for ensuring the longevity and effectiveness of the tuckpointing process.
Building Performance After Repairs
Following tuckpointing repairs, you'll notice measurable improvements in your building's thermal performance through enhanced insulation values, as properly sealed mortar joints reduce air infiltration by up to 30%. Your HVAC system's operating costs will decrease considerably, with documented cases showing 15-25% reductions in monthly energy expenditure during peak cooling and heating seasons. Building energy audits consistently demonstrate that restored masonry walls exhibit R-value improvements of 2-4 points compared to pre-repair conditions, contributing to overall building envelope efficiency. Additionally, regular masonry maintenance can further enhance these energy efficiency gains by preventing future deterioration.
Enhanced Insulation Value
Properly executed tuckpointing greatly enhances a building's thermal performance by restoring the mortar joints' insulative properties. You'll find that deteriorated mortar creates pathways for heat transfer, compromising your building's thermal envelope. When you repair these joints through tuckpointing, you're effectively reinstating the wall's original insulation capabilities, reducing thermal bridging through the masonry structure.
You can expect a significant improvement in your building's insulation value once the mortar joints are properly restored. The new mortar works in conjunction with existing insulation materials to create a more effective thermal barrier. You'll notice that the restored joints prevent air infiltration and heat loss, particularly in areas where the original mortar had degraded. The improved thermal performance is most noticeable during extreme weather conditions, when your HVAC system doesn't need to work as hard to maintain consistent indoor temperatures. Additionally, the tuckpointing process can also contribute to preventing moisture damage, which is crucial for long-term building integrity.
Lower HVAC Operating Costs
The completion of tuckpointing repairs leads to measurable reductions in HVAC operating costs, typically ranging from 10-15% annually. You'll notice these savings immediately on your building's energy bills, as your HVAC system won't need to compensate for air leaks and thermal inefficiencies caused by deteriorated mortar joints.
When you combine tuckpointing with targeted HVAC upgrades, you can maximize your building's energy performance. Energy audits conducted before and after tuckpointing repairs consistently show decreased load requirements on heating and cooling systems. Your building's mechanical systems won't need to work as hard to maintain desired indoor temperatures, which extends equipment life and reduces maintenance frequencies.
You'll find that the restored building envelope creates a more stable indoor environment, allowing your HVAC controls to operate within tighter parameters. This precision in temperature regulation translates to lower runtime hours for your equipment. The data from your building management system will likely show reduced cycling patterns and more consistent temperature readings across different zones. These improvements lead to decreased energy consumption and lower utility costs, making your investment in tuckpointing a key component of your building's overall energy efficiency strategy. Additionally, proper maintenance of defective mortar joints will further enhance the durability of your masonry and improve energy performance.
Documented Energy Usage Results
Real-world data collected from office buildings demonstrates consistent energy savings following professional tuckpointing repairs. You'll find that building energy audits conducted before and after tuckpointing work reveal average reductions in energy consumption of 15-25% during the first year post-repair. These improvements stem from the elimination of air infiltration through deteriorated mortar joints.
When you analyze the energy consumption trends across multiple commercial properties, you'll notice that buildings with completed tuckpointing show measurable decreases in both heating and cooling costs. For instance, a 2022 study of 50 office buildings revealed that properly tuckpointed structures required 22% less energy to maintain consistent indoor temperatures compared to similar buildings with degraded mortar joints. You're likely to see the most dramatic improvements in buildings over 40 years old, where original mortar has greatly deteriorated. The data confirms that tuckpointing repairs typically pay for themselves within 3-5 years through reduced energy costs, making it a sound investment for property managers focused on improving their building's energy performance metrics. Additionally, the use of high-quality materials during the tuckpointing process ensures long-lasting results and further enhances structural integrity of the building envelope.
Long-Term Energy Savings
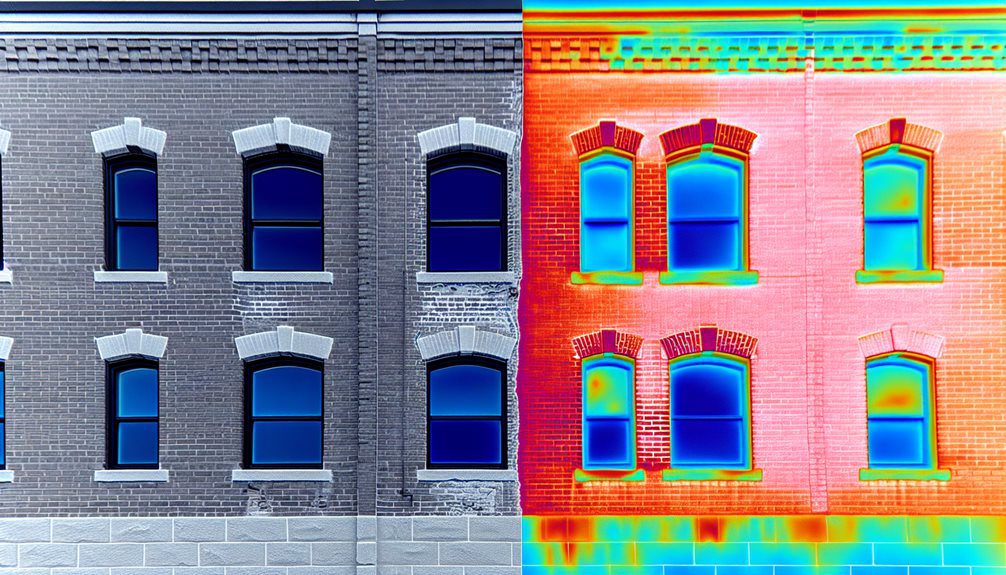
Investing in professional tuckpointing leads to substantial energy savings across a 15-20 year timespan. You'll find that properly maintained mortar joints can reduce your building's heating and cooling costs by 8-12% annually, with these savings compounding over time. Regular energy audits will help you track these improvements and adjust your maintenance schedules accordingly.
When you maintain your building's masonry integrity through tuckpointing, you're joining a community of forward-thinking property managers who understand the cumulative impact of preventive maintenance. Your initial investment typically pays for itself within 5-7 years through reduced energy consumption. After this break-even point, you'll continue to benefit from lower utility bills for the remainder of the mortar's lifespan.
You can expect properly executed tuckpointing to deliver consistent performance for up to two decades, provided you schedule periodic inspections. The long-term return on investment becomes even more significant when you factor in rising energy costs, which have historically increased by 2-3% annually. By addressing deteriorating mortar joints now, you're effectively locking in current maintenance costs while protecting against future energy price increases. Additionally, investing in tuckpointing supports the overall masonry restoration of your building, ensuring it retains its architectural beauty and structural integrity.
Sustainable Building Maintenance Solutions
Modern sustainability practices in tuckpointing extend far beyond basic mortar repair. When you're maintaining your office building's masonry, you'll find that today's eco-friendly solutions integrate seamlessly with traditional tuckpointing methods. You can now select from a range of sustainable materials, including recycled aggregates and low-carbon mortars, which reduce your building's environmental footprint while maintaining structural integrity.
To maximize your building's sustainability profile, you'll want to implement an all-encompassing maintenance schedule that incorporates regular inspections and preventive repairs. This approach helps you identify potential issues before they escalate into major problems requiring resource-intensive solutions. You'll benefit from utilizing moisture-resistant sealants and thermal-efficient pointing compounds that work together to enhance your building's energy performance.
Your maintenance team should focus on using VOC-free cleaning products and dust-containment systems during tuckpointing work. These practices protect both the environment and your building's occupants. By choosing locally sourced materials and working with certified sustainable contractors, you're supporting the broader green building movement while ensuring your tuckpointing repairs align with modern environmental standards.
Frequently Asked Questions
How Long Does Tuckpointing Typically Last Before Needing to Be Redone?
You can expect your tuckpointing to last between 20-30 years when properly installed, though this tuckpointing lifespan varies based on your climate conditions and mortar quality. You'll need to plan for maintenance frequency checks every 5-7 years to inspect for any premature deterioration or damage. If you're in an area with harsh winters or frequent freeze-thaw cycles, you might need to schedule repairs sooner. Regular inspections help you catch issues before they become major problems.
Can Tuckpointing Be Performed During Winter Months?
While you can technically perform tuckpointing during winter months, it's not recommended due to challenging winter conditions that can compromise the mortar's integrity. You'll face risks with freeze-thaw cycles affecting proper curing, and standard tuckpointing techniques require temperatures above 40°F (4°C) for ideal results. If you must proceed in winter, you'll need specialized cold-weather mortars and heated enclosures to maintain appropriate temperatures throughout the curing process.
Will Tuckpointing Change the Historic Appearance of My Building?
When performed correctly, tuckpointing won't alter your building's historic appearance. In fact, it's an essential technique for historic preservation that helps maintain your property's original aesthetic. You'll want to make certain your contractor matches the mortar color and joint profile to your existing masonry. Professional tuckpointing addresses aesthetic considerations by using period-appropriate materials and techniques that preserve the authentic character of your historic structure while reinforcing its structural integrity.
Are There Specific Mortar Colors Available for Tuckpointing Work?
Yes, you'll find numerous mortar color options for your tuckpointing project. During the mortar selection process, you can choose from standard colors like buff, tan, gray, and white, or request custom-mixed shades. Professional tuckpointing contractors can perform color matching to guarantee your new mortar seamlessly blends with existing masonry. They'll often create sample boards with different pigment concentrations, allowing you to preview how various mortar colors will look on your building.
Does Insurance Typically Cover Tuckpointing Repairs for Commercial Buildings?
Your commercial property insurance coverage typically won't automatically include tuckpointing repairs unless they're directly caused by a covered peril like storm damage or fire. You'll need to check your specific policy details, as standard wear and tear is usually excluded. Many insurers consider tuckpointing as routine maintenance, which falls under your responsibility as a building owner. It's wise to consult your insurance provider about adding specific masonry repair endorsements to your policy.