Protect your below-grade commercial spaces through extensive waterproofing systems that combine membrane barriers and strategic water management. You'll need to select between sheet-applied or fluid-applied membranes based on your substrate conditions and exposure levels, with liquid membranes ideal for complex geometries and sheet membranes perfect for large flat surfaces. Implement proper drainage solutions, including foundation drains and French drains, to divert water away from your building's perimeter. Regular maintenance and inspections can extend system life by 15-25 years, while quality installations reduce repair costs by 60-80%. Understanding your specific waterproofing requirements will determine the most effective long-term solution for your facility.
Understanding Below-Grade Waterproofing Systems
Protection against water infiltration begins with a thorough understanding of below-grade waterproofing systems. When you're designing waterproofing solutions for your commercial space, you'll need to take into account both hydrostatic pressure and soil composition as primary factors that affect system performance. These systems work together to create a protective barrier between your building's foundation and groundwater.
You'll find that below-grade waterproofing typically consists of multiple components working in harmony. The primary membrane – whether it's a sheet-applied or fluid-applied system – serves as your first line of defense. You'll want to pair this with proper drainage materials and protection boards to manage water movement around your foundation walls.
Understanding the relationship between hydrostatic pressure and your chosen system is essential. You'll need to factor in varying pressure levels at different depths and how your soil composition affects water movement. Clay soils retain more moisture and create higher pressure points, while sandy soils allow for better drainage. By selecting appropriate materials and installation methods based on these factors, you'll guarantee your waterproofing system performs effectively throughout your building's lifecycle.
Common Water Infiltration Issues
Commercial buildings face several critical water infiltration challenges that can compromise structural integrity and interior conditions. You'll encounter multiple water sources threatening your building's foundation, including surface runoff, rising groundwater, and lateral water pressure. Understanding these threats is essential for implementing effective waterproofing strategies.
When you're dealing with moisture migration, you'll need to address both hydrostatic pressure and capillary action. These forces can drive water through microscopic concrete pores, creating persistent dampness and potential structural issues. Your building's vulnerability increases in areas with high water tables or poor soil drainage conditions.
Common infiltration points you'll need to monitor include wall-floor joints, utility penetrations, and expansion joints. These areas often develop problems due to settlement, thermal movement, or initial construction defects. You'll also find that cracks in foundation walls, whether from structural movement or curing, create direct pathways for water intrusion. By identifying these typical entry points, you can develop targeted remediation strategies that protect your investment and maintain ideal building performance. Regular inspection of these vulnerable areas helps prevent costly water damage and maintains your building's long-term integrity. Furthermore, utilizing effective waterproofing techniques can significantly enhance your building's resistance to moisture penetration.
Essential Waterproofing Materials
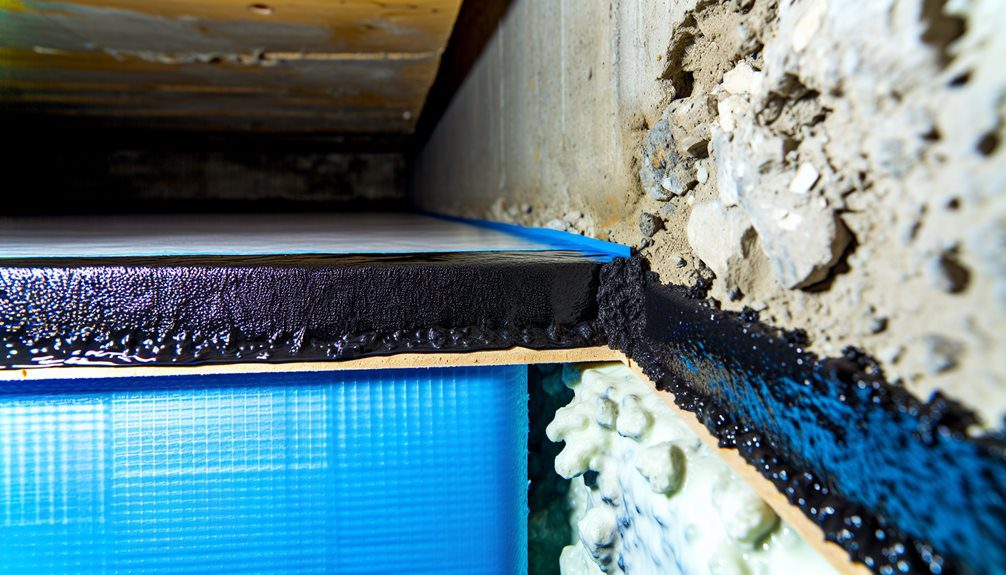
When you're selecting waterproofing materials for your commercial project, you'll need to understand the key differences between sheet membranes, liquid-applied membranes, and bentonite systems – each serving specific architectural requirements. Water-stop products, including PVC waterstops, hydrophilic strips, and injectable systems, create critical barriers at construction joints and penetrations where water intrusion commonly occurs. These essential materials work together as an integrated waterproofing strategy, with membrane selection typically driven by substrate conditions and exposure levels, while water-stop placement focuses on vulnerable connection points in your structure.
Membrane Types and Applications
Waterproofing membranes serve as the primary defense against water intrusion in commercial buildings, with several distinct types available for specific applications. You'll find that liquid membranes offer seamless coverage and are ideal for complex geometries and irregular surfaces. These systems cure to form a continuous barrier and can be applied using spray equipment or rollers, making them particularly effective for foundation walls and podium decks.
Sheet membranes, including modified bitumen and thermoplastic variants, provide consistent thickness and are excellent for large, flat surfaces. You'll want to take into account these for plaza decks and green roofs where reliability and puncture resistance are vital. When you're working with pre-applied systems, they're typically installed before concrete placement, creating a strong mechanical bond with the structure.
For best performance, you'll need to match membrane type to your specific project conditions. Reflect on factors like hydrostatic pressure, substrate condition, and installation environment. Self-adhering membranes work best in temperatures above 40°F, while hot-applied systems can be installed in colder conditions. Always verify compatibility between your chosen membrane and any protection boards or drainage components you'll be using.
Water-Stop Products Overview
A thorough water-stop system forms an integral part of your building's waterproofing strategy, incorporating multiple product types to prevent water infiltration at construction joints and penetrations. You'll need to select from several water stop types, including PVC waterstops, hydrophilic rubber strips, and injectable hydrophilic grouts, each serving specific functions in your waterproofing assembly.
PVC waterstops are your primary defense in concrete joints, featuring ribbed profiles that create a mechanical barrier against water intrusion. When you're dealing with pipe penetrations, hydrophilic rubber strips expand upon contact with moisture, forming a tight seal around the penetration point. For existing structures requiring remediation, injectable hydrophilic grouts offer a solution by filling voids and cracks through pressure injection.
Installation techniques vary by product type. You'll need to secure PVC waterstops at the correct position before concrete placement, ensuring they're properly aligned and supported. Hydrophilic strips require clean, smooth surfaces and must be fully adhered using manufacturer-approved adhesives. When you're installing injectable grouts, proper port placement and injection pressure are critical for achieving complete void filling and effective water stopping.
Drainage and Water Management
Proper drainage and water management form the backbone of any effective commercial waterproofing system. You'll need to implement multiple drainage techniques to guarantee water moves away from your building's foundation effectively. Start by installing a thorough foundation drainage system that includes both interior and exterior components working in tandem to protect your investment.
Your primary water diversion strategy should incorporate French drains positioned strategically around the building's perimeter, connected to a main collection system that channels water away from the structure. You'll want to confirm your drainage mat provides adequate compressive strength while maintaining high flow capacity under load. Install filter fabrics to prevent soil particles from clogging your drainage pathways, and position your drains at the lowest point of the excavation.
Don't overlook the importance of proper grading – you'll need a minimum 2% slope away from your foundation walls. Your subsurface drainage system should include clean-outs for maintenance access and connect to either a storm sewer system or daylight discharge point, depending on your local codes and site conditions.
Application Methods and Techniques
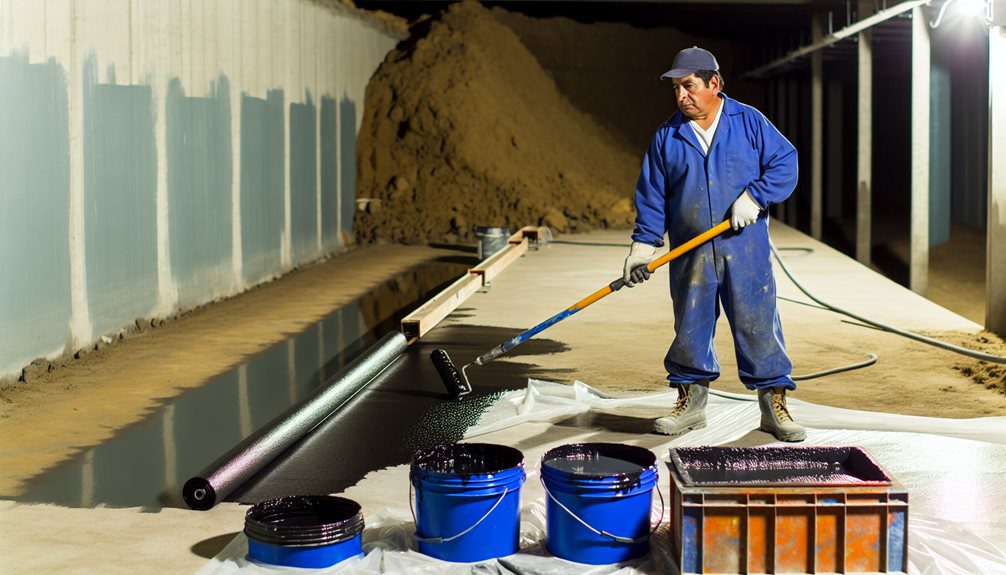
Successful application of commercial waterproofing materials demands strict adherence to manufacturer specifications and environmental conditions. You'll need to monitor temperature, humidity, and surface moisture levels throughout the application process to guarantee peak membrane performance. Before beginning any application, you must properly prepare the substrate by cleaning, repairing cracks, and addressing surface irregularities.
For large-scale commercial projects, spray application offers the most efficient coverage and consistent mil thickness. You'll achieve better results by maintaining proper pressure settings and application distance while guaranteeing uniform coverage across the substrate. When working with detailed areas or smaller surfaces, roller application provides better control and precision, though it's more time-consuming.
You must apply multiple coats in a cross-hatch pattern to eliminate pinholes and guarantee complete coverage. Between coats, you'll need to observe manufacturer-specified cure times and conduct mil thickness tests. Don't forget to protect freshly applied waterproofing materials from precipitation and mechanical damage during the curing period. Once cured, you should perform flood testing or electronic leak detection to verify the integrity of your waterproofing system before proceeding with subsequent construction phases.
Maintenance and Inspection Protocols
Regular maintenance and inspection of commercial waterproofing systems will extend their service life and prevent costly failures. You'll need to establish a clear inspection frequency, typically conducting thorough assessments quarterly and after severe weather events. Your maintenance checklist should include examining surface coatings, joint sealants, and drainage systems for signs of deterioration or damage.
During inspections, you should document any cracks, blistering, or separation in waterproof membranes. Check drainage points for proper water flow and clear any blockages in gutters or downspouts immediately. Pay special attention to penetrations, changes, and termination points where water infiltration commonly occurs.
You'll want to test your below-grade waterproofing systems annually using electronic leak detection or flood testing methods. Monitor interior walls and floors for water stains, efflorescence, or increased humidity levels, as these indicate potential system failures. Keep detailed records of all inspections, repairs, and maintenance activities, including photos and moisture readings. When you spot issues, address them promptly to prevent water damage from compromising your building's structural integrity and your waterproofing investment. Additionally, consider consulting professionals for masonry restoration to ensure your waterproofing systems are integrated effectively with the building's overall structure.
Cost Analysis and ROI
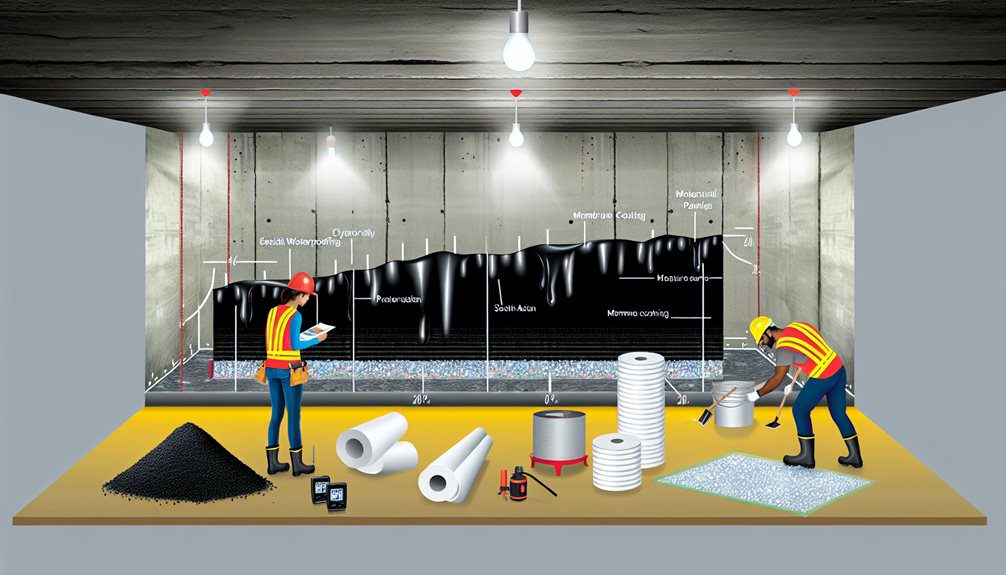
Comparing initial waterproofing investments requires you to evaluate multiple system types, including membrane systems ($8-15/sq ft), crystalline solutions ($5-12/sq ft), and liquid-applied coatings ($6-10/sq ft). You'll need to factor in regional labor costs, substrate preparation requirements, and specific building conditions to determine your total project expenditure. The long-term ROI calculation must account for the system's expected lifespan, maintenance costs, and potential damage prevention, which typically shows premium systems yielding 15-25% better returns over a 20-year period.
Initial Investment Comparisons
The initial investment in commercial waterproofing systems varies considerably based on square footage, substrate conditions, and chosen materials. You'll find that crystalline systems typically range from $3-7 per square foot, while bentonite sheet membranes can cost $8-15 per square foot. Liquid-applied membranes fall somewhere in between at $5-10 per square foot.
When evaluating budget considerations, you'll need to factor in substrate preparation costs, which can add 15-30% to your base expenses. Labor costs vary by region but generally account for 40-50% of the total investment. You'll also want to explore financing options, as many suppliers offer flexible payment terms for large-scale commercial projects.
Your comparison should include ancillary costs such as drainage boards ($1.50-3 per square foot), protection courses ($0.75-2 per square foot), and joint treatments ($3-8 per linear foot). Most commercial projects require an extensive system rather than a single solution, so you'll need to budget for a complete waterproofing assembly. Remember that value-engineered solutions often combine different products to achieve ideal cost-effectiveness while maintaining performance standards.
Long-Term Value Assessment
Professional waterproofing solutions deliver significant returns over their operational lifespan, with quality systems providing 15-25 years of protection before requiring major maintenance. When you're conducting a value assessment, you'll need to factor in not just the initial installation costs, but also the reduced maintenance expenses, prevention of structural damage, and protection of valuable interior assets.
You'll find that properly installed commercial waterproofing systems demonstrate exceptional long-term durability, often reducing repair costs by 60-80% compared to non-waterproofed structures. Your investment typically pays for itself within 5-7 years through prevented water damage, reduced energy costs, and maintained property value. Consider that every dollar spent on prevention saves $4-6 in future repairs.
To maximize your ROI, you'll want to focus on three key metrics: annual maintenance savings, extended structural lifespan, and reduced insurance premiums. By implementing extensive waterproofing solutions, you're joining other forward-thinking property managers who've documented 30-40% reductions in building operation costs over a 10-year period. Your building's market value will also benefit, typically increasing by 10-15% with certified waterproofing systems in place.
Frequently Asked Questions
How Long Does Below-Grade Waterproofing Typically Last Before Needing Replacement?
Your below-grade waterproofing's longevity typically ranges from 20-50 years, depending on several replacement factors. You'll find that proper installation, material quality, and environmental conditions greatly impact durability. If you've used high-grade membranes and followed manufacturer specifications, you can expect 30+ years of protection. However, you'll need earlier replacement if you're dealing with hydrostatic pressure issues, poor drainage, or settlement problems that compromise the system's integrity.
Can Waterproofing Be Applied During Winter Months or Freezing Temperatures?
You'll need to carefully consider cold weather application limitations when planning winter waterproofing projects. Most membrane systems require temperatures above 40°F (4°C) for proper adhesion and curing. If you're working in freezing conditions, you'll want to use specialized cold-weather formulations or create a heated enclosure around your work area. Some two-component products can be applied at lower temperatures, but you'll need to verify manufacturer specifications and adjust curing times accordingly.
What Warranties Are Typically Available for Commercial Below-Grade Waterproofing Systems?
You'll typically find two main warranty options for below-grade systems: manufacturer's material warranties and contractor's workmanship guarantees. Coverage duration usually ranges from 5-20 years for materials, while workmanship warranties often extend 1-5 years. You'll want to verify if your warranty includes labor for repairs and maintenance. Premium systems might offer extended coverage up to 30 years, but they'll require certified installers and documented maintenance protocols.
Are There Green or Eco-Friendly Waterproofing Solutions for Below-Grade Spaces?
You'll find several eco-friendly materials for below-grade waterproofing that align with sustainable practices. Consider bentonite clay systems, which are naturally occurring and biodegradable. You can also opt for water-based crystalline solutions that penetrate concrete without harmful VOCs. Plant-based liquid membranes and recycled rubber products offer effective alternatives to traditional petroleum-based systems. Look for products with environmental certifications like LEED points to guarantee you're making responsible choices.
How Does Soil Type Affect the Choice of Waterproofing System?
You'll need to carefully match your waterproofing system to your soil's characteristics. Clay soils with low permeability can trap water against foundations, requiring robust drainage systems and hydrostatic pressure resistance. Sandy soils with high permeability might affect foundation stability but allow better natural drainage. You'll want to conduct soil testing to determine composition, drainage patterns, and pH levels before selecting your waterproofing approach. This guarantees you're choosing a system that's optimized for your specific site conditions.